220v proximity sensor
- time:2025-07-07 14:13:57
- Click:0
Unlocking Industrial Efficiency: The Power & Precision of 220V Proximity Sensors
In the relentless heartbeat of modern industry, where automated lines hum and robotic arms dance with precision, unseen sentinels stand guard. These silent workhorses ensure seamless operation, prevent costly collisions, and orchestrate intricate movements. Among the most crucial, yet often overlooked, are proximity sensors. And when the demands are high-voltage and the environment unforgiving, the 220V proximity sensor emerges as the undisputed champion for robust, reliable industrial detection.
What Exactly is a 220V Proximity Sensor?
At its core, a proximity sensor is an electronic device designed to detect the presence or absence of an object without physical contact. It achieves this through various physical principles, primarily electromagnetic fields or capacitance changes. The defining characteristic of a 220v proximity sensor is its operating voltage: it’s engineered to function reliably within standard industrial AC power systems, typically rated for 110V to 240V AC (alternating current). This makes it fundamentally different from lower-voltage DC (direct current) sensors common in smaller electronics or vehicles.
How the Industrial Workhorse Operates: Inductive & Capacitive Principles
The vast majority of industrial 220v proximity sensors are inductive. Here’s the elegant science in action:
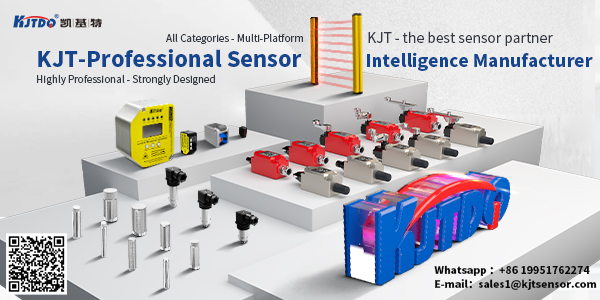
- The Oscillator: Inside the sensor’s face, an oscillator circuit generates a high-frequency electromagnetic field.
- Field Disturbance & Eddy Currents: When a conductive metal target (like steel, aluminum, copper) enters this field, it induces tiny circulating electrical currents within the target material – known as eddy currents.
- Energy Absorption & Damping: These eddy currents absorb energy from the sensor’s oscillating field. This energy loss dampens the oscillation amplitude.
- Detection Circuit: A monitoring circuit within the sensor detects this drop in amplitude (or a shift in frequency, depending on the design).
- Signal Switching: Upon detecting the sufficient amplitude/frequency shift caused by the target, the sensor’s solid-state output switch changes state. For a normally open (NO) sensor, this means it “closes,” allowing current to flow; for normally closed (NC), it “opens,” stopping current flow. This switch is what controls external devices like PLCs, relays, or motor starters.
Capacitive 220v proximity sensors operate on a different principle. They detect changes in capacitance formed between the sensor face and a target object. When any material (metal, plastic, wood, liquid, granules) approaches the sensor face, it alters the dielectric constant and thus the capacitance of the sensing field. This change is detected, triggering the output switch. While less common than inductive types at 220V AC, capacitive sensors are vital for detecting non-metallic objects on production lines.
Why Choose a 220V Proximity Sensor? The Compelling Advantages
The dominance of 220v proximity sensors in heavy industry stems from several powerful benefits:
- Direct AC Line Integration: Seamlessly integrates into standard industrial control panels powered by 110V/220V/240V AC mains. Eliminates the need for separate, lower-voltage DC power supplies required for many DC sensors, simplifying wiring and reducing costs.
- Exceptional Durability & Robustness: Built specifically for harsh industrial settings, these sensors offer outstanding resistance to vibration, shock, moisture, dust, oils, and chemicals. Their enclosures are typically rugged metal or high-impact industrial plastics.
- High Immunity to Electrical Noise: Industrial environments are electrically noisy. 220v proximity sensors are engineered with superior electromagnetic compatibility (EMC) characteristics, minimizing false triggers from nearby motors, drives, or welding equipment.
- Long Sensing Ranges: Compared to many low-voltage DC sensors, inductive 220v proximity sensors often offer longer nominal sensing distances for equivalent sensor sizes, providing more flexibility in mounting.
- Reliability & Long Lifespan: Employing solid-state electronics with no moving parts to wear out, these sensors boast an exceptionally long operational life and require minimal maintenance. Their contactless nature inherently prevents mechanical wear.
- High-Speed Operation: Capable of detecting objects passing by at very high speeds, making them perfect for high-throughput production lines and fast-moving machinery.
Where 220V Proximity Sensors Shine: Critical Applications
Their robustness and direct AC compatibility make 220v proximity sensors indispensable across countless industrial sectors:
- Material Handling & Packaging: Detecting the position of pallets, boxes, bottles, cans on conveyors; verifying case packer operation; presence/absence detection in filling lines.
- Metal Fabrication & Machining: Tool position verification on CNC machines; monitoring robotic arm end effectors; detecting metal sheets or parts entering presses or stamping machines; checking spindle position.
- Automotive Manufacturing: Precision positioning of components on assembly lines; verifying robot paths; detecting vehicle bodies entering paint booths or assembly stations; end-of-stroke detection.
- Food & Beverage Processing: Monitoring ingredient levels in hoppers (capacitive); detecting cans/bottles on fillers; verifying cap placement; position sensing on processing equipment (often requiring food-grade housings).
- Heavy Machinery & Construction Equipment: Position feedback on hydraulic cylinders (end-of-stroke detection); bucket or blade position sensing; overload protection systems; safety interlock verification.
- Pulp & Paper Mills: Roll diameter monitoring; web break detection; position control in cutters and winders.
Selecting the Right 220V Proximity Sensor: Key Considerations
Choosing the optimal sensor is crucial. Ask these questions:
- Target Material: Is the target metallic (requires inductive) or non-metallic (requires capacitive)?
- Required Sensing Distance: How far away does the target need to be reliably detected? Factor in the sensor’s nominal range (Sn) and ensure adequate real-world clearance.
- Mounting Constraints: Barrel style (threaded)? Block style? What size threads or dimensions fit the application?
- Output Configuration: Normally Open (NO) or Normally Closed (NC)? PNP or NPN switching logic? (Crucial for PLC compatibility - AC sensors typically mimic discrete switching states).
- Environmental Conditions: Exposure to extreme temperatures, washdowns, corrosive chemicals, welding sparks, or strong magnetic fields? Select the appropriate housing material (stainless steel, nickel-plated brass, specific plastics - IP67/IP68 ratings are common for protection) and inherently shielded designs if needed.
- Electrical Specifications: Confirm the specific voltage range (e.g., 20-250V AC) and current rating (mA) matches your control circuit.
Installation & Safety: The 220V Imperative
Working with 220v proximity sensors demands respect for electrical safety:
- Always de-energize circuits before starting installation or maintenance. Lockout/Tagout (LOTO) procedures are mandatory.
- Ensure proper grounding of both the sensor (if metallic-bodied) and the