inductive proximity sensor switch
- time:2025-07-07 14:06:54
- Click:0
The Invisible Detectives: Unlocking the Power of Inductive Proximity Sensor Switches
Imagine a factory humming with relentless precision. Robot arms weld, conveyors glide, and machines stamp with unwavering rhythm. Ensuring this ballet of metal and motion operates flawlessly, often without a single physical touch, are unsung heroes: inductive proximity sensor switches. These robust, non-contact workhorses silently safeguard efficiency and reliability in countless automated processes. But what exactly are they, and why are they indispensable in modern industry?
Demystifying the Core Technology
At its heart, an inductive proximity sensor switch is an electronic device designed to detect the presence of metallic (primarily ferrous) objects without any physical contact. It achieves this remarkable feat through the principles of electromagnetic induction, famously discovered by Michael Faraday.
Here’s the elegant science simplified:
- Generating the Field: An internal high-frequency oscillator generates a fluctuating electromagnetic field emanating from the sensor’s sensing face.
- The “Invisible” Interaction: When a metallic target (like steel, iron, aluminum, brass, copper) enters this active field, eddy currents are induced on its surface. Think of these as tiny swirling electrical currents created within the metal itself by the sensor’s changing magnetic field.
- Detecting the Difference: These eddy currents draw energy from the sensor’s oscillator circuit. This energy loss causes a measurable change, typically a reduction in the amplitude of the oscillations.
- Triggering the Switch: Built-in signal processing circuitry continuously monitors the oscillator’s state. Once the change caused by the target reaches a pre-defined threshold, the sensor’s solid-state output switch changes state. This is the crucial “switch” aspect – it flips from OFF to ON (or vice-versa, depending on configuration), sending a clean electrical signal to the control system (e.g., a PLC).
It’s truly contactless magic – the target doesn’t need to hit a lever or button; its mere presence within the detection zone does the job.
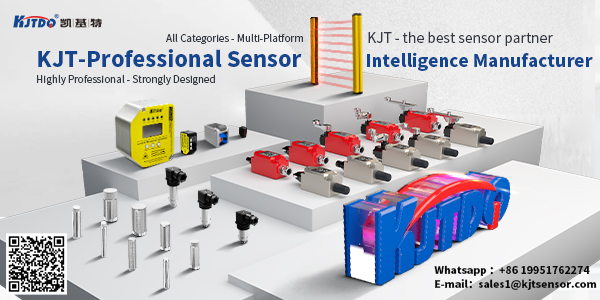
Key Characteristics Defining Their Value
Inductive sensors are prized for specific advantages that make them ideal for industrial environments:
- Non-Contact Sensing: The core benefit. No moving parts touch the target, eliminating mechanical wear, friction, and the need for physical force. This translates directly to remarkable longevity and minimal maintenance.
- High Reliability & Repeatability: Solid-state electronics and the absence of physical contact points ensure highly consistent operation over millions of cycles. Once installed and set, they deliver dependable detection time after time.
- Robust Construction: Typically housed in sturdy metal or industrial-grade plastic casings, they are inherently resistant to dirt, dust, oil, water (often IP67 or IP68 rated), vibration, and electromagnetic interference. They thrive where mechanical switches would fail.
- High Switching Speed: Capable of detecting objects moving at high speeds, reacting in milliseconds. This is vital for fast-paced automation and high-speed counting applications.
- Output Flexibility: Common outputs include NPN (sinking), PNP (sourcing), NO (Normally Open), NC (Normally Closed), and sometimes analog (0-10V/4-20mA) proportional to distance. This allows seamless integration into diverse control systems.
- Simple Installation and Operation: Generally easy to mount and configure, requiring only power and a connection to the control input.
- Target Specificity: Designed primarily for metals. While this might seem a limitation, it’s actually a strength where avoiding false triggers from non-metallic objects (like plastic, wood, or operator hands) is critical.
Understanding the Detection Zone: Shielded vs. Unshieldened
A critical specification for any inductive sensor is its nominal sensing distance (Sn). This is the ideal distance at which a standard target (usually a 1mm thick square of mild steel) is consistently detected. However, the shape of the electromagnetic field is just as important:
- Shielded Sensors (“Flush Mountable”): These sensors have a metal ring surrounding the coil, focusing the electromagnetic field radially forward from the sensing face. This allows them to be mounted flush with surrounding metal structures without the metal interfering with their operation. The sensing range is generally shorter, but the focused field is ideal for tight spaces or when embedding the sensor is necessary.
- Unshielded Sensors: Lacking the surrounding metal shield, these sensors generate a larger, more lateral electromagnetic field. This results in a longer sensing range compared to shielded types of the same size. However, they require a specific clearance (free space) around them when mounting – typically 1-2 times their sensor diameter – as surrounding metal can disrupt the field and reduce effective range. Choosing between shielded and unshielded is crucial for optimal performance in any application.
Where the Action Is: Ubiquitous Industrial Applications
The unique blend of ruggedness, reliability, and non-contact operation makes inductive proximity sensors ubiquitous across industry:
- Position Verification & End-of-Travel Detection: Confirming a cylinder is fully extended/retracted, a slide has reached its endpoint, or a part is correctly positioned in a fixture. Feedback loops rely heavily on this.
- Object Counting: Accurately tallying bottles, cans, packages, or manufactured parts moving on a conveyor belt. High speed and non-contact are essential.
- Level Detection: Monitoring levels of metallic liquids or granular materials within tanks or hoppers (using specialized designs).
- RPM Monitoring & Speed Sensing: Detecting rotating teeth on gears or sprockets to calculate rotational speed.
- Presence/Absence Checking: Ensuring a part is present on a pallet, a tool is loaded correctly in a CNC machine, or a metal component has been assembled.
- Machine Safety: Used as part of safety interlock systems to verify guards are closed or dangerous areas are clear before machinery starts.
- Conveyor Control: Tracking the position of products, triggering diverters, or controlling accumulation.
Selecting the Right Tool: Key Considerations
Choosing the optimal inductive sensor involves several factors beyond shielded/unshieldened:
- Required Sensing Distance (Sn): Ensure the sensor’s Sn exceeds the maximum operating gap needed in your application, providing a safety margin.
- Target Material: Most sensors are calibrated for steel. Detection ranges for non-ferrous metals like aluminum or copper can be significantly reduced (often 30-60% of Sn). Check sensor specifications for the specific target material.
- Target Size: The minimum detectable target must be large enough to effectively interact with the sensor’s field. A very small screw head might not trigger a sensor designed for large machine parts. Sensor datasheets usually specify minimum target requirements.
- Environmental Factors: Consider extremes of temperature, potential exposure to chemicals, high-pressure washdown (requiring IP69K rating), or strong magnetic fields. Select a sensor with suitable IP ratings and environmental specifications.
- Electrical Output & Wiring: Match the sensor’s output type (NPN/PNP, NO/NC) and voltage rating to your controller’s inputs. Ensure the correct wiring configuration.
- Physical Size & Mounting: Choose a form factor (e.g., cylindrical M8, M12, M18, M30, or block-style) that fits the available space and mounting constraints. Consider shielded vs. unshielded needs.
The Indispensable Sensor
Inductive proximity sensor switches are far more than simple on/off devices. They are the fundamental, reliable eyes of automation, providing critical binary feedback about the presence, position, or absence of metallic objects in the most demanding environments. Their contactless operation, inherent robustness, and versatility make them an irreplaceable component in achieving efficiency, safety, and precision across the vast landscape of modern manufacturing, packaging, material handling, and beyond. Wherever metal moves or must be detected without touch, you’ll likely find an inductive proximity sensor silently and reliably doing its job.