banner inductive sensor
- time:2025-07-07 11:24:51
- Click:0
Banner Inductive Sensors: The Unsung Heroes of Robust Industrial Automation
In the gritty, demanding world of factory floors and automated machinery, reliability isn’t just a bonus – it’s the bedrock of productivity. Where vibrations shake, metal chips fly, and liquids threaten, a sensor that falters means production stops. This is precisely the environment where Banner inductive sensors shine. Far more than just another component, they are fundamental, rugged workhorses designed to detect metal presence with unwavering consistency. Understanding their capabilities and applications is crucial for engineers and technicians building resilient, efficient systems.
So, what is a Banner inductive sensor? It belongs to the broad family of proximity sensors, specifically leveraging electromagnetic induction for non-contact metal detection. Unlike mechanical switches that wear out or optical sensors easily blinded by grime, inductive sensors operate without physical touch. They generate a high-frequency electromagnetic field from their sensing face. When a metallic target (like a machine part, actuator, or pallet) enters this field, it induces small eddy currents within the metal. These currents create a counter-electromagnetic field, which the sensor detects. This interaction causes a change in the sensor’s internal oscillation circuit, triggering a solid-state electronic switch (output). The target doesn’t need to touch the sensor; simply entering the defined sensing range is enough.
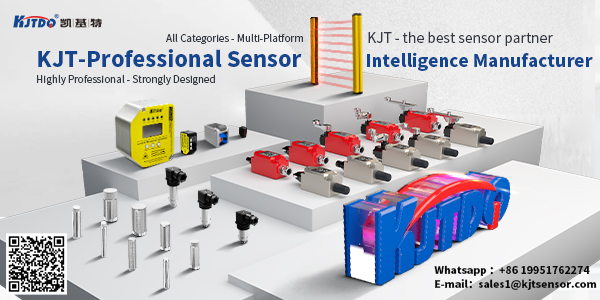
Why choose Banner Engineering for inductive sensors? The answer lies in their relentless focus on performance, durability, and innovation tailored for harsh industrial realities:
- Legendary Robustness: Banner sensors are renowned for their tough-as-nails construction. Featuring high-quality stainless steel or nickel-plated brass housings and advanced sealing techniques (typically IP67, IP68, or IP69K rated), they shrug off impacts, resist corrosion from coolants and chemicals, and remain operational even when submerged or subjected to high-pressure washdowns. This resilience translates directly to reduced downtime and maintenance costs.
- Exceptional Reliability & Longevity: By eliminating moving parts and relying on solid-state electronics, Banner inductive sensors offer an exceptionally long operational life, often rated for millions of operation cycles. They are immune to contact bounce issues and unaffected by most oils, dirt, dust, and non-metallic particles that commonly plague other sensing technologies.
- Extended Sensing Ranges: Banner consistently pushes the envelope in achieving longer operating distances for a given sensor size. Their advanced designs allow for generous sensing ranges, providing greater installation flexibility and simplifying machine design. You might find a compact M12 sensor offering ranges competitive with larger sensors from other brands.
- Versatility in Outputs and Formats: Whether you need a simple DC 3-wire PNP or NPN transistor output, analog outputs (current or voltage) for distance measurement, or specialized versions like NAMUR for hazardous areas, Banner offers a comprehensive range. They come in industry-standard threaded barrels (M5, M8, M12, M18, M30), rectangular block styles, and specialized form factors to fit virtually any mounting constraint.
- Smart Features & Enhanced Diagnostics: Modern Banner inductive sensors often incorporate features like teach-in functions for easy setup adjustment, IO-Link communication for advanced diagnostics, remote configuration, and process data integration, and visual status indicators (LEDs) for immediate troubleshooting at the sensor head.
The applications for Banner inductive sensors are vast across virtually every industrial sector involving metal detection and position feedback:
- Machine Automation: Detecting piston rod positions on cylinders, confirming end-of-travel on slides or actuators, verifying part presence on pallets or conveyors, monitoring tool changer positions.
- Material Handling: Verifying pallet presence, detecting metal containers on conveyors, sensing forks on AGVs, confirming position in sorting systems.
- Packaging Machinery: Confirming lid placement on cans, detecting metalized packaging elements, verifying cap presence, controlling filling levels (using metal dip tubes or floats).
- Automotive Manufacturing: Detecting fixture clamping/unclamping, confirming robot tooling engagement, sensing metal parts through paint booths or during assembly stages.
- Metal Forming & Cutting: Monitoring press ram positions, detecting slugs or finished parts, verifying tool positions.
- Food & Beverage (where applicable): Detecting metal caps, lids, cans, or trays.
Selecting the right Banner inductive sensor involves considering several key factors specific to your application:
- Target Material: While primarily for ferrous metals (like steel), many Banner sensors are optimized for detecting non-ferrous metals (like aluminum, brass, copper) or even offer universal detection capabilities. Sensor range varies significantly based on target material type and size (typically specified using a standard square steel target size, e.g., 1mm thick x 1”x1”).
- Required Sensing Range: How close can the target be reliably brought to the sensor face? Banner provides detailed specifications for each model’s nominal sensing range (Sn) under standard conditions.
- Mounting Constraints & Environment: Consider the physical space available. Threaded barrel sizes (M5, M8, M12, M18, M30) are common, but rectangular block styles or special mountings exist. Crucially, match the sensor’s IP rating to the environmental hazards present – dust, water jets, oils, chemicals, high temperatures. Banner sensors are known to operate reliably in ambient temperatures ranging from -40°C to +85°C (-40°F to +185°F) and beyond in specialized models.
- Electrical Requirements: Voltage supply (typically 10-30V DC), output type (PNP/NPN NO/NC), current rating, and circuit configuration must match your control system. IO-Link offers significant advantages for data-rich applications.
- Performance Needs: Do you require high switching frequencies for rapid part counting? Is immunity to surrounding metal (flush vs. non-flush mounting) critical? Is analog position feedback needed? Banner’s extensive portfolio caters to diverse performance criteria.
Installation best practices ensure peak performance and longevity. Adhere to recommended mounting clearances to avoid interference from surrounding metal (“side-by-side” and “face-to-face” spacings matter!), ensure stable power supply, protect wiring in conduits or cable carriers, and follow Banner’s specific mounting instructions. Regularly cleaning the sensing face of debris is also simple, effective preventative maintenance.
Banner inductive sensors represent the culmination of decades of engineering excellence focused squarely on solving real-world industrial sensing challenges. They deliver critical, reliable detection where it matters most – in the heart of demanding automation systems. Their combination of rugged construction, proven reliability, extended sensing capabilities, and versatile feature sets makes them a cornerstone technology. From simple presence checks to complex position monitoring in the harshest environments, specifying a Banner inductive sensor is often a decisive step towards achieving robust, low-maintenance, high-uptime automation. When metal needs to be sensed dependably, day in and day out, Banner provides the confidence engineers rely on.