ferrous proximity sensor
- time:2025-07-07 11:17:48
- Click:0
Ferrous Proximity Sensors: The Essential Guide to Reliable Metal Detection
Imagine a hyper-sensitive guardian that silently watches over your machinery, instantly knowing when any piece of iron or steel approaches – without ever touching it. No levers, no buttons, just an invisible field of awareness. That’s the fundamental magic of the ferrous proximity sensor, a workhorse of industrial automation. These unsung heroes perform millions of detection tasks daily, ensuring safety, precision, and efficiency in countless applications. How do they achieve this seemingly simple yet critical feat? Let’s delve into the world of inductive proximity switches specifically tuned for ferrous metals.
The Core Principle: Electromagnetism in Action
At the heart of every ferrous proximity sensor lies a simple principle: electromagnetism. The sensor contains an oscillator circuit generating a high-frequency electromagnetic field that radiates out from its active face. This field constantly probes the space immediately in front of the sensor.
Here’s the key differentiator: When a ferrous metal target (iron, steel, etc.) enters this electromagnetic field, it interacts with the field in a unique way. Unlike non-ferrous metals which primarily induce eddy currents, ferrous metals possess high magnetic permeability. This means they concentrate the sensor’s magnetic field lines. This concentration drastically changes the characteristics of the oscillator circuit within the sensor itself – typically causing a decrease in oscillation amplitude or a shift in frequency.
An internal circuit meticulously monitors these changes in the oscillator. Once the disturbance caused by the ferrous metal reaches a predetermined threshold (the sensing point), the sensor’s output state switches. This switch could involve turning a solid-state transistor ON or OFF, or changing the state of a relay. Crucially, this all happens without any physical contact.
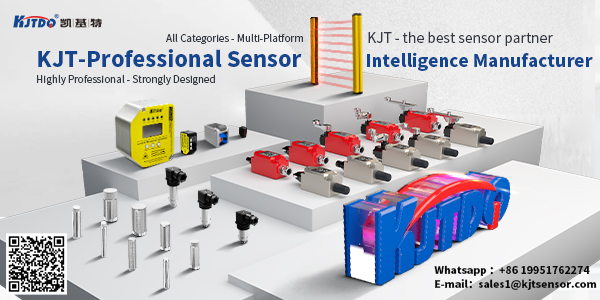
Defining Characteristics of Ferrous Proximity Sensors
While they share the inductive principle with sensors designed for non-ferrous metals, ferrous proximity sensors boast distinct features:
- Non-Contact Operation: Their core advantage. They detect targets reliably through wear and tear, dust, oil, and other contaminants that would plague mechanical switches.
- Exceptional Reliability: With no moving parts to break or wear out, they offer incredibly long operational lifespans and minimal maintenance needs. This makes them ideal for demanding industrial environments.
- High Switching Speed: These sensors can detect targets and switch outputs incredibly fast – often thousands of times per second. This speed is essential for modern high-throughput automation and position sensing.
- Resilience to Harsh Environments: Generally housed in robust materials like stainless steel, nickel-plated brass, or tough engineering plastics (PBT), they boast high IP ratings (Ingress Protection), shielding them from dust, moisture, and chemicals. Many are also resistant to vibration and shock.
- Hysteresis: A built-in feature preventing output chattering when a target is right at the sensing point. Once triggered, the target must move slightly further away than the nominal sensing distance to turn the output off again. This ensures clean, stable switching signals.
- Directional Sensitivity: The sensing field is focused primarily perpendicular to the face of the sensor. This allows for precise positioning and detection without interference from nearby metallic objects.
Where They Shine: Powering Industrial Applications
The unique ability to detect iron and steel reliably makes ferrous proximity sensors indispensable across numerous sectors:
- Manufacturing & Assembly Lines: Detecting the presence or absence of ferrous components (brackets, gears, shafts), verifying correct positioning before welding or machining, counting parts on conveyors, and monitoring end-of-travel for actuators and cylinders. Position sensing is critical here.
- Material Handling: Confirming the position of ferrous pallets, containers, or doors; protecting overhead cranes by detecting obstructions made of steel.
- Automotive Industry: Monitoring engine components, verifying gear positions in transmissions, detecting brake disc presence, and controlling robotic arms working with steel parts.
- Machine Tooling: Tool presence detection in CNC machines (e.g., confirming a steel drill bit is loaded), chuck jaw position verification, and protecting against collisions.
- Packaging Machinery: Detecting metal lids, caps, or foil seals on containers.
- Security Systems: Often used as hidden door sensors on metal doors or gates to detect unauthorized opening.
Advantages Over Alternatives: Why Choose Ferrous Detection?
Compared to other sensor types targeting metals, ferrous proximity sensors offer specific benefits:
- Higher Sensing Distance for Ferrous: Generally, for the same physical size, an inductive sensor offers a significantly longer sensing distance when detecting ferrous metals compared to non-ferrous metals like aluminum or copper.
- Simplicity & Robustness: Their solid-state design makes them simpler and often more robust than mechanical limit switches or vision systems for basic presence detection tasks.
- Cost-Effectiveness: They are typically a highly cost-effective solution for reliable ferrous metal detection, especially in volume applications.
- Immunity to Surface Conditions: Dust, oil, water, frost, and light surface coatings generally do not affect their ability to detect the underlying ferrous material.
Selecting the Right Ferrous Proximity Sensor: Key Considerations
Choosing the optimal sensor requires careful assessment:
- Sensing Range: The nominal sensing distance (Sn) must be sufficient for the application, factoring in installation tolerances and any required mounting distance (e.g., behind metal). Remember, the actual sensing distance is rated for mild steel; it reduces for other ferrous alloys and is significantly less for non-ferrous metals.
- Target Size & Material: The sensor must detect the specific ferrous alloy involved. Smaller targets require sensors designed for shorter ranges or potentially shielded designs. Confirm detection capability.
- Output Type: Most common are DC 3-wire types (NPN or PNP transistor outputs sourcing/sinking current). AC models and 2-wire AC/DC versions also exist. Relay outputs are less common nowadays. Choose based on your control system input requirements.
- Housing Size & Shape: Cylindrical (threaded barrel) is most common, but rectangular block and specialized shapes exist. Size dictates sensing range and fit constraints. Consider flush or non-flush mounting capabilities.
- Environmental Protection (IP Rating): Select an IP rating (e.g., IP67, IP68, IP69K) suitable for the environment (dust, water jets, washdowns, chemicals). Stainless steel housings are preferred for aggressive environments.
- Electrical Specifications: Ensure compatibility with the supply voltage (e.g., 10-30V DC, 20-250V AC) and check the output current rating is sufficient for the load.
- Temperature Rating: Verify the sensor operates reliably within the ambient temperature range of the application.
The Unseen Enabler of Precision Automation
From ensuring a robotic arm picks up the correct steel component to verifying a gear has engaged correctly in a transmission, ferrous proximity sensors provide the essential digital eyes for iron and steel in the automated world. Their blend of robust non-contact detection, high reliability, and straightforward integration makes them a fundamental building block of modern industrial systems. By understanding their unique operating principle centered on magnetic permeability, distinct advantages, and careful selection criteria, engineers can harness the silent power of these inductive proximity switches to build smarter, safer, and more efficient machinery. The next time you see a complex machine operating flawlessly, chances are a humble ferrous proximity sensor is playing a vital role deep within its workings.