rectangular inductive proximity sensor
- time:2025-07-06 00:24:11
- Click:0
Rectangular Inductive Proximity Sensors: The Robust Workhorses of Industrial Detection
In the relentless clash of metal, the unforgiving environments of factories, and the demanding pace of automated lines, reliable object detection isn’t just convenient—it’s critical. Amidst dust, oil, vibration, and electromagnetic noise, a specific type of sensor consistently delivers: the rectangular inductive proximity sensor. Often overshadowed in casual discussion by their cylindrical counterparts, these unsung heroes offer unique advantages that make them indispensable for countless industrial applications demanding durability, precise mounting, and dependable non-contact sensing.
Understanding the Core Technology: How Induction Works
At its heart, an inductive proximity sensor, rectangular or otherwise, operates on the principle of electromagnetic induction. It contains an oscillator circuit generating a high-frequency electromagnetic field emanating from its active face. When a metallic target object enters this field, eddy currents are induced within the metal. These eddy currents draw energy from the oscillator, causing its amplitude to decrease. An integrated evaluation circuit meticulously monitors this amplitude change. Once the reduction surpasses a predefined threshold (the sensing distance or operating point), the sensor triggers its output signal – solid-state switching (like PNP or NPN transistors) to indicate the presence of the target. This entire process happens contactlessly, making these sensors ideal for applications with rapid movement or where physical contact would cause wear and tear.
Why Rectangular? Unpacking the Form Factor Advantage
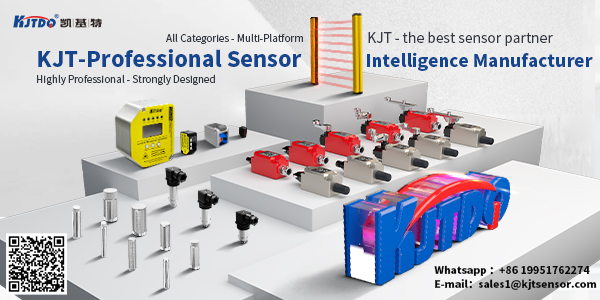
While cylindrical sensors are prevalent, the rectangular inductive proximity sensor offers distinct mechanical and practical benefits:
- Optimized Mounting & Space Utilization: The flat sides and defined corners of a rectangular sensor simplify installation. They are inherently more stable when mounted on flat surfaces or within machined slots, minimizing the risk of rotation during operation or installation. This shape maximizes sensing range relative to the often necessary mounting space constraints compared to similarly sized cylinders. Their profile allows for efficient side-by-side mounting where space is tight.
- Enhanced Robustness & Protection: Rectangular sensors frequently feature robust, IP-rated enclosures (like IP67, IP68, or IP69K) crafted from resilient materials such as nickel-plated brass or high-grade stainless steel (V4A/AISI 316L). This robust construction provides superior resistance to impacts, mechanical stress, crushing forces, and harsh chemicals encountered in demanding industrial settings like machine tools, heavy machinery, and material handling systems. The flat face design can also be inherently better at shedding debris.
- Flush Mounting Prowess: Many rectangular inductive sensors are designed specifically for flush mounting (embedding into metal structures). Their shape allows them to be mounted flush without requiring extra clearance, enabling installation directly within machine frames, guides, or actuators. Crucially, their shielding ensures they are immune to surrounding metal, meaning the mounting bracket or surrounding structure does not interfere with their sensing field when installed correctly.
- Stable Sensing Field: The rectangular coil geometry often produces a well-defined sensing field shape, potentially offering advantages in specific detection scenarios where the target’s orientation or approach path is predictable.
Key Capabilities and Specifications
Rectangular inductive sensors share core capabilities with other inductive types, but their form factor often enables specific performances:
- Non-Contact Metal Detection: Their primary function is detecting the presence (or absence) of ferrous metals (like iron, steel) and often non-ferrous metals (like aluminum, brass, copper), though typically with a shorter sensing range for non-ferrous materials. This is fundamental for position verification, counting, or end-of-travel detection.
- Operating Principle: Relies purely on electromagnetic induction.
- Sensing Range (Sn): Specified in millimeters, varies significantly based on sensor size, coil design, and target material. Larger rectangular sensors can achieve longer ranges, while smaller ones are suitable for tight positions. Ranges typically range from 1-2mm for very compact units up to 40mm or more for larger industrial sensors.
- Output Types: Primarily solid-state DC outputs (3-wire):
- PNP (Sourcing): Outputs positive supply voltage (+V) when active.
- NPN (Sinking): Outputs ground (0V) when active.
- Some models offer Analog (current or voltage) or IO-Link outputs for more data.
- Switching Frequency: Indicates how rapidly the sensor can reliably detect objects passing by. High switching frequencies (up to several kHz) are common, making them suitable for high-speed counting or presence detection on fast-moving production lines. The robust construction helps maintain performance at speed.
- Repeatability: The precision with which the sensor consistently detects the target at the same point. High repeatability is crucial for precision automation. Rectangular sensors often achieve excellent repeatability due to stable mounting.
- Hysteresis: This is the difference between the operating point (where the sensor turns ON as the target approaches) and the release point (where it turns OFF as the target moves away). Hysteresis prevents rapid switching (“chatter”) if the target is vibrating near the sensing point – a vital feature in harsh environments.
- Voltage Range: Designed for industrial DC supplies, commonly 10-30 V DC.
The Indispensable Role in Harsh Environments
It’s in challenging conditions that rectangular inductive proximity sensors truly prove their worth:
- Immunity to Contaminants: Unlike optical sensors, they are immune to surface contamination like dust, dirt, oil, grease, and water. The electromagnetic field penetrates these non-metallic layers, ensuring reliable detection even on dirty or oily machine parts. Their sealed housings further protect internal electronics.
- Vibration & Shock Resistance: Their robust build quality and stable mounting make them exceptionally resistant to the constant vibrations found in machinery, conveyors, presses, and vehicles. They can withstand significant mechanical shock without damage or performance degradation.
- Temperature Resilience: Engineered to operate reliably across broad temperature ranges, typically from -25°C to +70°C or even wider, catering to foundries, freezers, and outdoor applications.
- Electrical Noise Immunity: Designed with shielding and robust circuitry to resist interference from common industrial electrical noise sources like variable frequency drives (VFDs), motors, and welding equipment.
Selecting and Implementing Rectangular Inductive Sensors
Choosing the right sensor involves considering several factors:
- Target Material: Ferrous or non-ferrous? This significantly impacts the required sensing range.
- Required Sensing Distance (Sn): Select a sensor with a rated Sn slightly greater than your actual needed distance to account for installation tolerances, temperature effects, and voltage fluctuations.
- Mounting Constraints: Does the application demand flush mounting? Is space extremely limited? The rectangular form excels in flush and tight-space scenarios.
- Environmental Conditions: Assess temperature extremes, presence of chemicals, level of dust/water ingress (IP rating), and vibration/shock levels.
- Output Type & Wiring: Choose PNP or NPN based on your control system’s input requirements (PLC, controller). Ensure correct wiring for power connections.
- Housing Material: Nickel-plated brass offers good corrosion resistance, while stainless steel (V4A) is essential for highly corrosive or washdown environments (food & beverage, chemical processing).
- Electrical Specifications: Match the voltage supply and ensure the load current is within the sensor’s capacity.
Mounting Best Practices: