waterproof proximity sensor
- time:2025-07-06 00:30:12
- Click:0
Waterproof Proximity Sensors: The Unsung Heroes of Harsh Environment Sensing
Imagine a robotic arm precisely assembling car parts on a mist-filled factory floor. Or a food processing line reliably detecting cans whizzing by under high-pressure washdowns. What enables seamless operation amidst splashes, dust, steam, and constant cleaning? The answer often lies in a remarkably resilient workhorse: the waterproof proximity sensor. Far more than just “splash-proof,” these sensors are engineered to perform consistently where moisture and demanding conditions would cripple ordinary electronics. Understanding their capabilities is crucial for designing robust industrial automation, agricultural systems, marine equipment, and countless other applications requiring reliable non-contact object detection in wet or dirty settings.
Demystifying the Waterproof Proximity Sensor
At its core, a proximity sensor detects the presence or absence of an object without physical contact. Common types include inductive sensors (for metals), capacitive sensors (for both metals and non-metals like liquids or plastics), and photoelectric sensors (using light beams). A waterproof proximity sensor builds upon this foundation by incorporating specialized sealing and construction techniques. Its primary purpose is to provide unwavering performance when exposed to:
- Water Immersion: Functioning even when temporarily or permanently submerged.
- High-Pressure Washdown: Resisting the force and penetration of cleaning jets, common in food & beverage or pharmaceutical production.
- Condensation & Humidity: Preventing internal fogging or corrosion from saturated air.
- Dust & Particulate Ingress: Keeping contaminants out to maintain sensing integrity.
- Chemical Exposure: Withstanding corrosive cleaners or process fluids depending on housing material (e.g., stainless steel).
Why Waterproofing is Non-Negotiable in Many Industries
The consequences of sensor failure in harsh environments are significant. In manufacturing, a single faulty sensor can halt an entire production line, causing costly downtime. In food processing, moisture ingress can lead to contamination risks and sanitation issues. Outdoor applications, from agricultural machinery to marine systems, face relentless exposure to rain, splashes, and humidity. Waterproof proximity sensors mitigate these risks, ensuring:
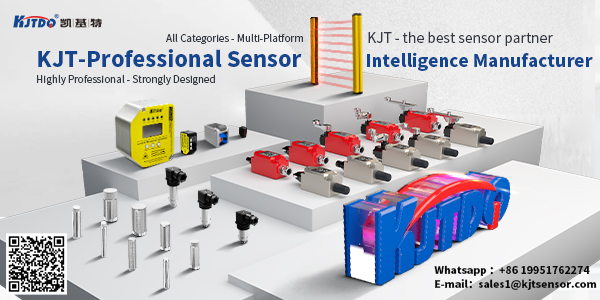
- Enhanced Reliability & Uptime: Minimizing production stoppages due to sensor failure.
- Reduced Maintenance Costs: Lowering the frequency of repairs and replacements.
- Improved Safety: Ensuring critical detection functions operate reliably in wet conditions (e.g., preventing machinery from activating near personnel).
- Longer Lifespan: Protecting sensitive internal electronics from environmental degradation.
- Process Integrity: Guaranteeing consistent detection in applications where condensation or splashing is inevitable.
Engineering Resilience: How Waterproofing is Achieved
Achieving true waterproofness isn’t accidental; it’s meticulously engineered. Key design elements include:
- Robust Housing: Materials like stainless steel (V2A, V4A) or high-grade engineering plastics (e.g., PBT) provide structural integrity and chemical resistance.
- Precision Sealing: Critical junctures, especially between the housing and sensing face and around cable entry points, are sealed using special O-rings, gaskets, or potting compounds designed to resist water pressure and temperature cycling.
- Potting/Encapsulation: Often, the sensor’s internal electronics are completely encased in epoxy resin or similar inert compounds. This creates a solid barrier against moisture, vibration, and shock, while also dissipating heat generated by the sensing coil.
- Potted Cable Glands: The point where the cable enters the sensor housing is a potential weak spot. Potted cable glands fill this entry point with sealing material, creating a monolithic seal impervious to water ingress.
The Language of Protection: Understanding IP Ratings
Not all “waterproof” claims are equal. The International Protection (IP) rating system provides a standardized way to understand the level of sealing effectiveness against solids (first digit) and liquids (second digit). For waterproof proximity sensors, the second digit is paramount:
- IP65: Dust-tight and protected against low-pressure water jets from any direction. Suitable for washdown areas where immersion isn’t expected.
- IP67: Dust-tight and protected against immersion in water up to 1 meter deep for up to 30 minutes. Common for sensors needing to withstand temporary submersion or deeper washdown.
- IP68: Dust-tight and protected against continuous immersion in water under conditions specified by the manufacturer (often deeper and longer than IP67). Essential for permanent submersion or high-pressure underwater applications.
- IP69K: Dust-tight and protected against close-range high-pressure, high-temperature water spraying. Designed for the most aggressive washdown cleaning procedures.
When selecting a sensor, always verify its specific IP rating for the intended environment – IP67/IP68 are typically the targets for true waterproof proximity sensor applications.
Choosing the Right Waterproof Proximity Sensor
Beyond the essential waterproof rating, several factors guide selection:
- Sensing Principle: Inductive for metals? Capacitive for liquids, powders, or non-metals? Photoelectric for presence/absence over distance? Choose based on the target material.
- Sensing Range: How far away does the sensor need to detect the object? Ranges vary significantly.
- Output Type: NPN/PNP transistor outputs (3-wire), Analog signals (4-20mA, 0-10V), or specialized outputs like NAMUR (for hazardous areas)? Match to your control system’s input requirements.
- Housing Material & Size: Stainless steel for high corrosion resistance or plastic? Cylindrical (threaded barrel) or block/rectangular? Consider chemical exposure and mounting constraints.
- Operating Temperature Range: Ensure the sensor can handle the ambient temperatures in your application.
- Supply Voltage: Match to your system voltage (typically 10-30V DC).
Installation Best Practices for Maximum Performance
Even the toughest sensor performs best with proper installation:
- Follow Mounting Instructions: Respect specified recessed mounting distances for shielded sensors or standoff distances for unshielded variants.
- Ensure Secure Connections: Use the correct cable glands and connectors certified for the sensor’s IP rating. Ensure terminals are tight and wiring is correct.
- Avoid Mechanical Stress: Don’t overtighten mounting nuts or strain the cable. Use cable ties properly.
- Consider Target Material & Environment: Ensure the target falls within the recommended size/material specs and that buildup (dirt, ice) isn’t interfering. Be mindful of extreme temperatures affecting sensing range.
The Future is Wet (and Safe)
From ensuring bottles are filled correctly on a wet conveyor to protecting underwater robotics, waterproof proximity sensors are indispensable components enabling automation to thrive in demanding real-world conditions. Their ability to operate reliably amidst water, steam, dust, and rigorous cleaning underpins efficiency, safety, and quality across countless industries. By understanding their technology, protection ratings, and selection criteria, engineers can confidently deploy these robust sensors as the reliable eyes and triggers within even the most unforgiving environments.