turck prox sensors
- time:2025-07-05 03:18:57
- Click:0
Turck Proximity Sensors: The Unseen Guardians of Industrial Reliability and Efficiency
In the relentless hum of modern manufacturing, where precision is paramount and downtime is devastating, unsung heroes quietly ensure smooth operations. Among these critical components, Turck proximity sensors stand out as fundamental pillars of industrial automation. These sophisticated yet robust devices provide the essential “eyes” for machinery, detecting the presence, absence, or position of objects without physical contact. Choosing the right sensor isn’t just a technical decision; it’s a strategic investment in operational resilience.
Understanding the Core: What Are Proximity Sensors?
At their essence, proximity sensors are non-contact detection devices. They emit an electromagnetic field or beam and react when a target object enters their sensing range. This reaction triggers an electrical signal, feeding vital information back to a controller (like a PLC). This fundamental capability – detecting objects reliably without touching them – eliminates mechanical wear, allows for high-speed operation, and functions effectively in challenging environments filled with dust, moisture, or vibrations.
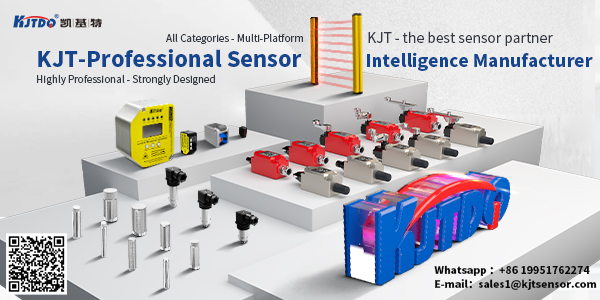
Why Turck Proximity Sensors Command Industry Respect
Turck has built a formidable reputation over decades by specializing in industrial automation connectivity and sensing solutions. Their proximity sensor range embodies this expertise, consistently delivering attributes crucial for demanding applications:
- Exceptional Ruggedness and Longevity: Engineered for industrial life, Turck sensors boast robust housings (often stainless steel or specialized plastics) and impeccable sealing (IP67, IP68, IP69K ratings are common). They shrug off impacts, resist washdown chemicals, and operate reliably in extreme temperatures, significantly reducing maintenance burdens and replacement costs.
- Uncompromising Sensing Performance: Precision is non-negotiable. Turck offers sensors with remarkably consistent and repeatable switching points. Factors like target material composition, size, and approach speed are carefully accounted for in their design, ensuring dependable detection cycle after cycle. This minimizes false triggers and missed detections, the culprits behind costly production errors.
- Innovative Technology Integration: Turck doesn’t just offer standard inductive sensors. Their portfolio includes advanced solutions like:
- Factors 1 Sensors: Featuring IO-Link connectivity, these intelligent sensors provide diagnostic data (temperature, operating hours, switch cycles) and allow remote parameterization. This enables predictive maintenance – addressing potential failures before they cause downtime.
- High-Temperature Sensors: Specifically designed to operate reliably in environments exceeding 100°C, even up to 250°C, crucial for processes like metal casting, plastic molding, or baking.
- Weld-Immune Inductive Sensors: Engineered to withstand intense electromagnetic interference (EMI) generated by welding equipment, ensuring stable operation where standard sensors fail.
- Comprehensive Application Coverage: From tiny inductive sensors detecting miniature parts to larger capacitive sensors sensing non-metallic materials (like liquids or plastics through containers), and specialized magnetic sensors (reed or Hall effect) for cylinder positioning, Turck provides the optimal sensing technology. Ultrasonic options handle demanding distance measurement tasks and object detection regardless of color or material.
- Simplified Installation and Connectivity: Turck leverages its core strength in connectivity. Many sensors feature industry-standard M8, M12, or M18 threaded connectors or pre-wired cables, seamlessly integrating with their renowned fieldbus connectors and junction boxes. This significantly speeds up installation, troubleshooting, and system modifications.
Key Applications Where Turck Prox Sensors Shine
The versatility of Turck’s proximity sensors makes them indispensable across countless industrial sectors:
- Automotive Manufacturing: Detecting parts on assembly lines, confirming robot end-of-arm tooling positions, verifying weld nut presence, and monitoring fluid levels in reservoirs. Reliability here is critical to maintaining high-volume production rates.
- Material Handling & Logistics: Counting packages on conveyors, verifying pallet presence at loading stations, monitoring bin levels, and detecting the position of AGVs (Automated Guided Vehicles). Downtime in logistics cascades rapidly through supply chains.
- Food and Beverage Processing: Confirming cap placement on bottles, detecting fill levels in containers (often using capacitive sensors), and verifying product presence on hygienic stainless steel lines built to withstand rigorous sanitation protocols (IP69K).
- Packaging Machinery: Ensuring cartons are present for labeling, detecting film breaks, confirming case sealing, and verifying product transfer between stations. High cycle rates demand equally fast and reliable sensors.
- Machine Tooling: Monitoring tool changer positions, confirming workpiece clamping, detecting part presence in fixtures, and safeguarding operator access with safety interlocks. Precision and safety are paramount.
- Building Automation: Controlling door positions, monitoring damper status in HVAC systems, and detecting occupancy for lighting control.
The Strategic Advantage: Beyond Basic Detection
Investing in high-quality Turck proximity sensors transcends simple component selection. It translates into tangible operational benefits:
- Maximized Uptime: Rugged construction and high reliability directly reduce unplanned machine stops, keeping production lines moving.
- Reduced Maintenance Costs: Long operational lifespans (often exceeding 200% of standard sensor life in harsh conditions) and diagnostic capabilities (via IO-Link) lower total cost of ownership.
- Enhanced Process Control: Consistent and accurate detection ensures processes run as intended, minimizing scrap and improving final product quality.
- Improved Safety: Reliable position feedback is critical for safe machine operation and effective safety interlock systems.
- Future-Proofing with Smart Capabilities: IO-Link enabled Turck sensors pave the way for Industry 4.0 initiatives, providing valuable data for optimization and predictive maintenance strategies.
In an industrial landscape defined by its demand for unwavering reliability, uncompromising precision, and seamless connectivity, Turck proximity sensors consistently deliver. They operate silently in the background, forming the essential sensory network that allows complex automation systems to function intelligently and efficiently. By choosing Turck, engineers and plant managers aren’t just selecting a sensor; they are fortifying their operations with a cornerstone of industrial resilience built on decades of proven innovation and quality.