safety rated proximity sensors
- time:2025-07-05 02:06:39
- Click:0
Safety Rated Proximity Sensors: The Essential Guardians of Machinery Safety
Imagine a high-speed robotic arm swinging its payload with immense power. Picture a massive press descending to shape metal, or automated guided vehicles (AGVs) navigating busy factory floors alongside workers. These scenarios represent the efficiency of modern industry, but they also inherently carry risk. The difference between a safe operation and a catastrophic incident often hinges on split-second detection and response. This is precisely where Safety Rated Proximity Sensors transition from simple components to critical life-saving devices, forming the bedrock of functional safety systems in industrial automation.
Unlike their standard counterparts designed for basic detection tasks, safety rated proximity sensors are engineered and certified to meet stringent international safety standards. Their core function goes beyond mere presence detection; they are integral components in safety circuits designed to prevent hazardous machine motion before harm can occur. Key standards governing their design, validation, and usage include ISO 13849 (Performance Level - PL) and IEC 62061 (Safety Integrity Level - SIL).
What Truly Defines “Safety Rated”?
The distinction lies in several critical design philosophies and capabilities mandated by safety standards:
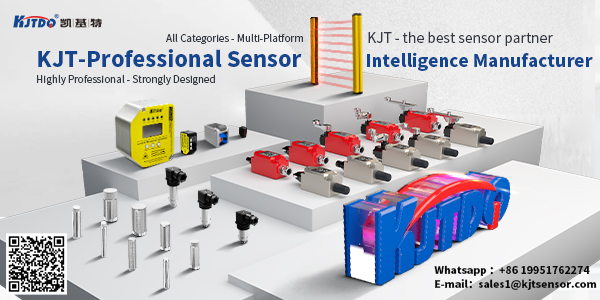
- High Diagnostic Coverage (DC): Standard sensors might fail silently, leaving machinery operating unsafely. Safety sensors incorporate sophisticated internal diagnostics that constantly monitor their own health and functionality. They detect internal faults like coil shorts, open circuits, or degraded performance in real-time.
- Redundancy and Diversity: Many safety rated proximity sensors employ dual-channel architectures. This means two independent sensing elements and circuits operate within a single device. Crucially, these channels often utilize diverse technologies or physical separation. If one channel fails, the other can still function, maintaining the safety function. This redundancy significantly reduces the probability of dangerous undetected failures.
- Fault Tolerance: Safety standards define required levels of fault tolerance. A device meeting Performance Level “d” (PLd) or Safety Integrity Level “2” (SIL 2), for example, is designed to remain safe even in the event of a single fault occurring within itself or its immediate control circuit. Higher levels like PLe or SIL 3 offer even greater fault tolerance.
- Clear Status Indication: Reliable feedback is paramount. Safety sensors provide unambiguous signals, often using specific output configurations like OSSD (Output Signal Switching Device) or dual-channel complementary signals. These signals indicate not just target detection but also the health status of the sensor itself.
- Robust Construction: Operating in harsh industrial environments demands resilience. Sealed housings (IP67, IP69K), resistance to shock, vibration, electromagnetic interference (EMI), and extreme temperatures are standard requirements to ensure reliable operation under demanding conditions.
- Rigorous Certification: Crucially, independent third-party certification bodies (like TÜV, UL) verify that these sensors comply with the relevant standards. Look for the specific SIL or PL rating clearly marked on the device and datasheet, along with the certifying body’s mark. This certification is non-negotiable for true safety integrity.
Why Standard Proximity Sensors Fall Short for Safety Functions
Using a standard proximity sensor in a critical safety application is a significant risk. Here’s why:
- Undetected Failures: A standard sensor can fail in a dangerous state (e.g., frozen output) without any warning to the safety system.
- No Diagnostics: It lacks the internal intelligence to monitor and report its own health, providing false confidence.
- Single Point of Failure: Relying on a single channel device means its failure directly compromises the entire safety function.
- Lack of Certification: They are not validated to meet the stringent requirements for risk reduction defined by SIL or PL.
Pivotal Applications: Where Safety Sensors Shine
Safety rated proximity sensors are mission-critical in countless scenarios:
- Machine Guarding: Monitoring the position of safety doors, gates, interlocks, and light curtains to ensure access is only permitted when machinery is in a safe state. Detecting a guard opening triggers an immediate safe stop.
- Robotic Cells: Establishing safe zones around collaborative and industrial robots. Sensors verify the robot is within its predefined safe operating envelope before allowing high-speed operation or triggering stops if an intrusion is detected.
- Press Brakes & Stamping Machines: Ensuring correct positioning of tooling and guarding, and critically, verifying that the operator’s hands are safely clear (presence sensing) before the downstroke begins.
- Material Handling & AGVs: Detecting objects or personnel in the path of AGVs, triggering slowdowns or stops. Ensuring pallets or loads are correctly positioned before automated handling sequences commence.
- Elevators & Escalators: Monitoring door positions, step gaps, and obstruction detection to prevent entrapment or shearing hazards.
The Tangible Benefits of Investing in Safety Integrity
Choosing genuine safety rated proximity sensors offers powerful advantages:
- Mitigated Risk of Injury: The primary goal: significantly reducing the likelihood of accidents involving machinery, protecting personnel, and fostering a culture of safety.
- Enhanced Machinery Uptime: By preventing accidents and enabling safe interaction points (like limited speed modes when personnel are near), safety sensors can actually contribute to smoother, more efficient operations.
- Regulatory Compliance: Essential for meeting stringent occupational health and safety regulations (like OSHA, EU Machinery Directive) and industry-specific standards. Using uncertified components can result in costly fines, shutdowns, and liability.
- Reduced Liability: Demonstrating due diligence through the use of certified safety components is crucial for protecting the organization from legal and financial repercussions following an incident.
- System Reliability: The inherent robustness, diagnostics, and fault tolerance of safety sensors often lead to higher overall reliability compared to cobbled-together solutions using standard components, reducing nuisance stops caused by undiagnosed failures.
In the intricate dance of modern industrial automation, safety rated proximity sensors are the vigilant partners ensuring that efficiency never comes at the cost of human well-being. Their sophisticated design, rigorous certification, and unwavering reliability make them indispensable components in functional safety architectures. They transform proximity detection from a basic operational signal into a powerful, trustworthy command capable of preventing harm. When lives are on the line, specifying and installing independently certified safety rated proximity sensors is not merely best practice – it is an ethical and operational imperative. They are, quite simply, the silent guardians allowing industry to progress safely.