sick inductive proximity sensor
- time:2025-07-05 02:00:39
- Click:0
SICK Inductive Proximity Sensors: Precision Detection for Industrial Automation
Imagine a robotic arm welding a car frame with millimeter precision. Or a conveyor belt reliably sorting thousands of metal parts per hour. What silent sentinels ensure these complex industrial processes operate flawlessly, preventing collisions, confirming placements, and guaranteeing quality? Often, the unsung heroes are SICK inductive proximity sensors, tirelessly providing crucial, non-contact detection of metallic objects in demanding environments.
Understanding Inductive Proximity Sensing: The Core Principle
At its heart, how does this technology work? Inductive proximity sensors leverage the fundamentals of electromagnetism. Within the sensor head resides an oscillator coil generating a high-frequency electromagnetic field. When a metallic object enters this field, eddy currents are induced within the metal itself. This phenomenon draws energy from the sensor’s oscillator coil, causing a measurable change in its amplitude or frequency. The sensor’s integrated electronics detect this precise change, triggering an electronic switch (solid-state output), signaling the object’s presence – all without any physical contact. This inherent principle makes them exceptionally robust, wear-free, and reliable.
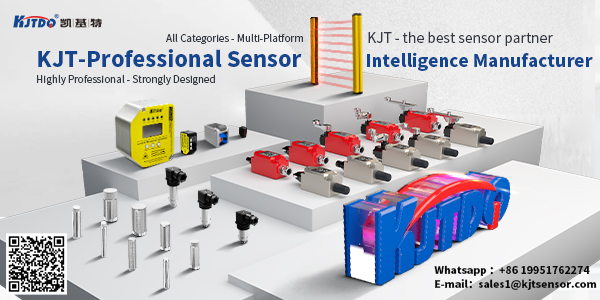
Why SICK Stands Out in Inductive Sensing
SICK AG, a global leader in sensor intelligence and automation solutions, elevates the standard inductive sensor concept through exceptional engineering and relentless innovation. Choosing SICK inductive proximity sensors isn’t just about picking a sensor; it’s about integrating a component known for:
- Unparalleled Precision and Reliability: SICK sensors offer remarkably short switching distances and high repeat accuracy. This pinpoint detection capability is vital for applications like high-speed counting, precise positioning of parts in assembly lines, or controlling machining tool positions, where even minute errors are unacceptable.
- Robustness in Harsh Industrial Environments: Engineered to thrive where others falter, SICK sensors boast superior resistance to shock, vibration, dust, dirt, moisture, oils, and coolants (often meeting IP67, IP68, IP69K ratings). Their rugged construction ensures consistent operation in foundries, welding shops, machining centers, and outdoor applications.
- Versatility Through Extensive Portfolio: SICK doesn’t offer a one-size-fits-all solution. Their range includes:
- Miniature Sensors: For space-constrained installations.
- High-Temperature Models: Operating reliably near furnaces or hot processes.
- Factor 1 Sensors (All-Metal Detectable): Capable of detecting any type of ferrous or non-ferrous metal equally well – a significant advantage over standard sensors which perform differently on different metals.
- Long-Range Sensors: Extending detection capabilities where needed.
- Analog Output Sensors: Providing continuous distance measurement, not just on/off signals.
- Specialty Designs: Including flush-mountable sensors for seamless mounting and sensors with specific resistances like weld field immunity.
- Advanced Features for Smarter Automation: Modern SICK inductive sensors go beyond simple detection. Look for models featuring:
- IO-Link Communication: Enabling digital parameter setting, remote diagnostics, and condition monitoring, paving the way for Industry 4.0 connectivity and predictive maintenance.
- Enhanced Diagnostics: Visual status indicators (like SICK’s innovative LED technology) and signal strength indicators simplify commissioning and troubleshooting.
- Advanced Housing Materials: Utilizing high-performance plastics and stainless steel for extreme chemical or cleaning resistance.
Critical Applications: Where SICK Inductive Sensors Drive Efficiency
The unique blend of SICK’s precision, robustness, and versatility makes these sensors indispensable across countless industrial sectors:
- Factory Automation & Assembly: Detecting parts presence/absence on conveyors, confirming correct part orientation before assembly, verifying cylinder end positions, controlling robotic tooling changes.
- Material Handling & Logistics: Monitoring pallet positions, detecting metal rollers or chains on conveyors, ensuring correct stacking heights, confirming bin filling levels (for metal containers).
- Automotive Manufacturing: Precise positioning of vehicle bodies for welding/assembly, monitoring robotic weld guns, detecting metal components in paint shops (using specialized high-temperature variants), confirming engine block placements.
- Metalworking & Machining: Verifying workpiece clamping/unclamping, monitoring tool positions on CNC machines (e.g., turret indexing), detecting metal slugs or finished parts exiting machinery, confirming protective door closures.
- Packaging Machinery: Detecting metal components within packaging lines, monitoring position of metallic cams or actuators, confirming can or metal lid presence.
Ensuring Peak Performance: Key Considerations
To fully leverage the capabilities of SICK inductive proximity sensors, consider these vital aspects:
- Correct Sensor Selection: Meticulously match the sensor type (standard, factor 1, analog, temperature-resistant, etc.), size, sensing range, electrical output (NPN/PNP, NO/NC), and housing material to your specific application’s demands and environmental conditions.
- Precise Mounting: SICK provides detailed mounting guidelines. Flush vs. non-flush mounting significantly impacts the nominal sensing range. Ensure proper clearance from surrounding metal objects (“mounting flush zone”) as specified in the datasheet.
- Environmental Factors: While highly resistant, consider extreme temperatures, aggressive chemicals, powerful magnetic fields, or heavy metallic swarf. SICK’s diverse portfolio has options tailored for these challenges.
- Power Supply & Wiring: Use a stable power supply within the sensor’s specified voltage range and adhere strictly to correct polarity and wiring practices. Protecting sensor outputs from overloads (e.g., using suppression diodes for inductive loads) is crucial for longevity.
SICK inductive proximity sensors represent the pinnacle of trusted, non-contact metallic object detection for industrial automation. Their fusion of fundamental reliability, engineered robustness, and continuous innovation delivers the precision and durability essential for maximizing efficiency, ensuring safety, and achieving consistent quality in the most demanding manufacturing and processing environments. When the integrity of your automated processes relies on detecting metal, SICK sensors provide the confidence and performance needed to keep operations running smoothly and predictably.