high temperature inductive sensor
- time:2025-07-05 00:54:19
- Click:0
High-Temperature Inductive Sensors: Unlocking Reliable Measurements in Extreme Environments
Imagine molten metal flowing, jet engines roaring, or glass glowing red-hot. These aren’t just scenes of raw industrial power; they represent environments where conventional sensors fail miserably. Temperature, the relentless adversary of electronics and materials, wreaks havoc on standard measurement systems. Enter the unsung hero: the high-temperature inductive sensor. These robust devices are engineered to thrive where others perish, providing vital position, speed, or presence detection in the most punishing heat-intensive applications. Their unique ability to operate accurately at elevated temperatures makes them indispensable for efficiency, safety, and process control across critical industries.
Understanding the Inductive Principle - Resilience by Design
At their core, inductive sensors are non-contact devices that detect metallic objects. They function using electromagnetic induction. A coil within the sensor generates a high-frequency oscillating magnetic field. When a metallic target enters this field, eddy currents are induced on the target’s surface. These eddy currents draw energy from the oscillator coil, causing a measurable change in the oscillation amplitude or frequency – effectively signaling the target’s presence or position. This core principle offers inherent advantages: no moving parts, resistance to dirt, oil, and vibrations, and long operational life.
However, extreme heat poses formidable challenges to this elegant principle:
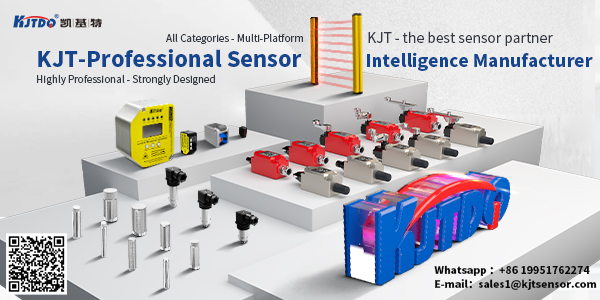
- Demagnetization of Core Materials: The ferrite cores essential for focusing the magnetic field lose their magnetic properties (exceed their Curie temperature), drastically reducing sensor range and sensitivity.
- Insulation Breakdown: Standard wire insulation (like PVC or PTFE) melts or degrades, leading to short circuits.
- Coil Deterioration: High temperatures accelerate oxidation and thermal stress on coil windings, potentially breaking connections or changing electrical properties.
- Electronic Component Failure: The integrated oscillator and evaluation circuitry are highly susceptible to thermal damage. Standard semiconductors have relatively low maximum junction temperatures.
- Thermal Expansion: Differential expansion rates between materials can cause mechanical stress, cracking, or loss of hermetic seals, allowing environmental contaminants inside.
Engineering for the Inferno: How High-Temp Inductive Sensors Overcome the Heat
Converting a standard inductive sensor into a high temperature inductive sensor isn’t a minor tweak; it’s a fundamental re-engineering effort focused on material science and thermal management:
- Specialized High-Temp Coils: Replacing standard copper windings with high-temperature alloys like Kanthal or utilizing advanced ceramic-coated windings significantly boosts thermal resilience. Special mineral-insulated cables (MIC) with ceramic or magnesium oxide insulation offer robustness.
- Advanced Core Materials: Moving beyond standard ferrites to specialty high-temperature ferrites or even ceramic core materials ensures the magnetic circuit remains functional well beyond typical Curie points. Some designs eliminate cores altogether, optimizing coil geometry for high-temp operation.
- Revolutionary Insulation: Ceramic-based insulators, high-temperature polymers like PEEK or Polyimide (Kapton), and fiberglass-reinforced materials replace standard plastics, maintaining dielectric strength under thermal stress.
- Innovative Housing & Sealing: Robust, thermally stable housings made from stainless steel (often grades 316 or 310) or high-nickel alloys protect the internal components. High-temperature glass-metal seals or ceramic-metal seals (often using Alumina) ensure hermeticity, preventing ingress of moisture or corrosive agents even under thermal cycling. Special potting compounds resist cracking.
- Remote Electronics (Crucial Innovation): Perhaps the most significant advancement is the separation of the sensing head and the evaluation electronics. The sensing head – containing just the coil and core within its high-temp housing – is installed directly in the hot zone. It connects via a high-temperature resistant cable (frequently MIC) to the evaluation electronics module, positioned in a cooler, protected environment. This decoupling allows the sensitive processing circuitry to operate safely at ambient or moderate temperatures while the sensing element braves the extreme heat. Inductive sensors configured this way can reliably operate at ambient temperatures exceeding 200°C, with specialized designs stretching beyond 500°C or even reaching over 1000°C for brief periods.
Where High-Temp Inductive Sensors are Mission Critical: Applications
The unique capabilities of these sensors make them vital in sectors where heat is unavoidable:
- Metal Production & Processing: Monitoring casting machines, continuous casting lines, hot rolling mills (detecting billet positions, coil positioning), forging presses, and induction heating systems. They track positions of molds, rollers, and billets surrounded by molten metal or intense radiant heat.
- Glass Manufacturing: Detecting gobs, molds, bottle positions, and lehr conveyor pushers in environments filled with high radiant heat from molten glass furnaces and forming processes.
- Automotive Testing & Powertrain: Monitoring components like turbochargers, exhaust valves, and within engine test cells exposed to extreme underhood or exhaust stream temperatures.
- Aerospace & Turbomachinery: Vital for monitoring blade tip clearance, shaft position, and actuation systems in jet engines and gas turbines during operation where temperatures are extreme.
- Energy & Power Generation: Used in boiler systems, steam turbines, and monitoring components within gasification plants.
- Industrial Ovens & Furnaces: Tracking door positions, conveyor chains, load presence, and actuator positions inside heat treatment furnaces, kilns, and curing ovens.
- Plastics & Rubber Processing: Position detection within extruders and vulcanizing presses operating at high temperatures.
- Geothermal Drilling: Monitoring equipment in deep, high-temperature boreholes.
Selecting the Right High-Temperature Inductive Sensor: Key Considerations
Choosing the optimal sensor requires careful evaluation:
- Maximum Ambient & Target Temperature: This is paramount. Ensure the sensor’s rated temperature exceeds your application’s maximum sustained and peak temperatures with a safety margin.
- Required Sensing Distance (Sn): Inductive sensor range can be slightly reduced at high temperatures compared to their standard counterparts. Verify the sensing distance at the operating temperature.
- Target Material: While designed for ferrous metals, ensure compatibility with the specific alloy being detected. Non-ferrous detection usually requires different sensor types or specific high-temp variants.
- Connection Type & Cable: The durability of the high-temperature cable and its connectors is critical. Mineral-insulated cables (MIC) are often the gold standard for the harshest environments but are less flexible. Define required cable length and jacket material temperature rating.
- Housing Material & Shape: Select corrosion-resistant materials (stainless steel) and the correct form factor (cylindrical, rectangular, ring-shaped) for mounting and the target.
- Protection Rating (IP/Ingress Protection): Ensure adequate sealing against dust, water, and potentially chemical splashes, especially if cleaning processes are involved.
- Output Type & Electronics: Define if you need PNP/NPN, NO/NC, analog output, etc., and ensure the remote electronics module is compatible with your control system.
The Unseen Enabler of Modern Industry