lidar proximity sensor
- time:2025-07-05 01:00:27
- Click:0
Seeing the Unseen: How Lidar Proximity Sensors Revolutionize Distance Detection
In an increasingly automated world, machines need eyes. More precisely, they need reliable, accurate ways to perceive their surroundings, avoid collisions, and navigate complex environments. While human eyes excel in many scenarios, machines require sensing technologies that work flawlessly in darkness, blinding light, fog, or rain – conditions where our vision falters. This is where LiDAR proximity sensors emerge as a game-changer, offering a powerful solution for precise distance measurement and environmental awareness across countless applications.
Understanding the Core: What is a LiDAR Proximity Sensor?
LiDAR stands for Light Detection and Ranging. At its essence, a LiDAR proximity sensor operates on a brilliantly simple principle: it emits pulses of laser light and precisely measures the time it takes for those pulses to reflect off an object and return to the sensor. Using the known speed of light, the sensor calculates the distance to the object with remarkable accuracy.
While the fundamental concept resembles radar (using radio waves) or sonar (using sound waves), LiDAR’s use of light provides distinct advantages:
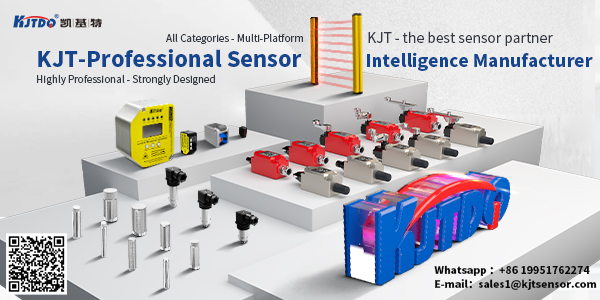
- Unparalleled Precision: Laser light travels in a very tight beam, allowing for extremely accurate distance measurements, often down to millimeters. This high spatial resolution enables the detection of small objects and fine details, crucial for applications like robotics or automated machinery.
- Excellent Range Resolution: LiDAR can distinguish between objects that are very close together along the same line of sight, a capability known as high range resolution.
- Environmental Resilience: Unlike optical cameras, LiDAR is largely unaffected by ambient light conditions. It performs well in total darkness and can often penetrate moderate atmospheric obscurants like fog, dust, or rain better than visible light cameras (though heavy conditions do pose challenges).
- 3D Perception: More advanced LiDAR systems, often using scanning mechanisms or arrays, can build detailed 3D point clouds of the environment. While a basic proximity sensor might provide a single distance point, the underlying technology forms the foundation for these sophisticated spatial maps.
LiDAR vs. the Competition: Why Choose Light?
To appreciate the value proposition of LiDAR proximity sensors, it’s helpful to compare them to common alternatives:
- Ultrasonic Sensors: Use sound waves. Pros: Low cost, good for short-range detection through some materials (like fabric). Cons: Susceptible to temperature variations, wind, and background noise; wider beam angle means lower accuracy; slower response time; cannot detect small objects well.
- Radar Sensors: Use radio waves. Pros: Excellent long-range capability, works well in all weather conditions. Cons: Typically lower spatial resolution than LiDAR, making it harder to distinguish small objects; complex signal processing; can be more expensive for high-resolution needs; potential for interference.
- Vision/Camera Systems: Use visible light. Pros: Rich contextual data (color, texture). Cons: Highly dependent on lighting conditions; performance degrades significantly in low light, glare, fog, or rain; computationally intensive for depth perception. LiDAR provides direct, robust distance measurement where cameras struggle.
Sensor Type |
Principle |
Key Advantages |
Key Limitations |
LiDAR Proximity |
Pulsed Laser Light |
High precision and resolution; works in varied lighting; better fog/dust penetration than cameras |
Performance degrades in heavy precipitation; can be expensive for high-end models |
Ultrasonic |
Sound Waves |
Low cost; penetrates some materials |
Susceptible to noise, temperature; wide beam angle; slower response |
Radar |
Radio Waves |
Long range; all-weather capability |
Lower spatial resolution; complex processing; potential interference |
Vision Systems |
Visible Light |
Rich contextual data |
Highly dependent on lighting; struggles in low visibility; computationally intensive |
LiDAR Proximity Sensors in Action: Powering Innovation
The unique capabilities of LiDAR proximity detection make them indispensable in numerous fields:
- Automotive Safety & ADAS: This is perhaps the most visible application. LiDAR sensors are crucial components in Advanced Driver Assistance Systems (ADAS) and autonomous driving. They provide accurate distance measurements to vehicles, pedestrians, cyclists, and obstacles, enabling features like:
- Automatic Emergency Braking (AEB)
- Adaptive Cruise Control (ACC)
- Lane Keeping Assist (LKA)
- Blind Spot Detection (BSD)
- Crucially, LiDAR offers reliable performance in challenging lighting conditions where cameras might fail.
- Industrial Automation & Robotics:
- Collision Avoidance: Safeguarding robots operating alongside humans (cobots) or navigating dynamic factory floors. LiDAR proximity sensors act as the machine’s “bumpers,” triggering emergency stops.
- AGV/AMR Navigation: Automated Guided Vehicles and Mobile Robots use LiDAR for simultaneous localization and mapping (SLAM), obstacle detection, and safe path planning. Precise proximity sensing ensures smooth and safe operation in complex warehouse environments.
- Object Detection & Positioning: Verifying the presence, position, or absence of objects on conveyor belts, in bins, or during assembly processes.
- High-Bay Warehousing: Monitoring aisles and preventing collisions for cranes and forklifts operating at height.
- Drones (UAVs): Essential for altitude hold, terrain following, and obstacle avoidance, especially during Beyond Visual Line of Sight (BVLOS) operations or autonomous flights. LiDAR helps drones navigate around trees, power lines, and structures.
- Smart Infrastructure: Monitoring clearance distances for bridges, tunnels, and construction sites; detecting vehicles or people in restricted zones; managing traffic flow.
- Consumer Electronics: Emerging applications include gesture recognition for AR/VR devices, robot vacuum cleaners for room mapping and cliff detection, and enhanced security systems.
How Does It Work? A Technical Glimpse
While the core Time-of-Flight (ToF) principle is straightforward, the implementation in a modern LiDAR proximity sensor involves sophisticated components:
- Laser Diode: Typically emits pulsed infrared (IR) light (e.g., 905nm or 1550nm) invisible to the human eye. 1550nm lasers offer better eye safety margins.
- Optics: Lenses collimate (narrow) the emitted laser beam and focus the returning scattered light.
- Photodetector: A highly sensitive semiconductor device (like an Avalanche Photodiode - APD) that converts the faint returning light pulse into an electrical signal. The timing of this signal is critical.
- Timing Circuitry: Ultra-precise electronics measure the time difference between the emission of the laser pulse and the detection of the return signal with picosecond resolution.
- Signal Processing Unit: Filters noise, calculates the distance (
Distance = (Speed of Light × Time of Flight) / 2
), and often handles further tasks like object classification or communication via interfaces (CAN, Ethernet, IO-Link, etc.).
- (Optional) Scanning Mechanism: Some proximity sensors use micro-mirrors or rotating assemblies to scan the laser beam over an area, providing multiple distance points or a field of view.
Key Considerations: Range, Field of View, and Environment
When selecting a LiDAR proximity sensor, several factors are paramount:
- Detection Range: From centimeters to hundreds of meters, depending on laser power, optics, and the target’s reflectivity. Choosing the appropriate range is vital for the application’s safety and functionality.
- Field of View (FoV): The angular area the sensor monitors. Can vary from a narrow spot beam (a few degrees) for precise targeting to wide angles (e.g., 270°) for broad area monitoring like robotics.
*