balluff inductive proximity sensor
- time:2025-07-04 04:07:14
- Click:0
The Unseen Guardians: Why Balluff Inductive Proximity Sensors Power Precision Automation
Imagine the relentless pulse of a high-speed automotive assembly line. Robotic arms swing with rhythmic precision, welding sparks fly, and conveyor belts hum. Hidden within this orchestrated chaos, performing millions of silent, flawless detections every day, are unsung heroes: Balluff inductive proximity sensors. These rugged, dependable devices are fundamental to modern manufacturing, ensuring processes run smoothly, efficiently, and safely by detecting metal objects without physical contact. But what makes Balluff sensors a cornerstone in demanding industrial environments?
Understanding the Core: Inductive Sensing Demystified
At the heart of every Balluff inductive proximity sensor lies a simple yet powerful principle. The sensor generates an oscillating electromagnetic field around its active face. When a metallic object enters this field, it disrupts the field’s flow, inducing tiny circulating electrical currents called “eddy currents” within the target metal. This energy loss dampens the sensor’s internal oscillation. Sophisticated circuitry within the Balluff sensor detects this precise change in oscillation amplitude and triggers a solid-state output switch. This entire process happens near-instantaneously and entirely without physical contact, making these sensors incredibly reliable and wear-free. Their primary function is robust, non-contact detection of metallic targets.
Balluff’s Edge: Engineering Excellence for Industrial Resilience
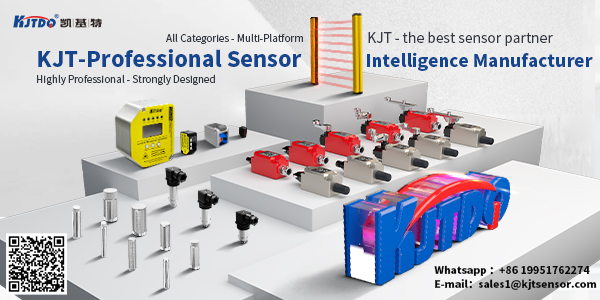
While the basic physics is shared, Balluff elevates inductive sensing to an art form through meticulous engineering, delivering distinct advantages:
- Uncompromising Precision & Reliability: Balluff sensors are renowned for their exceptional repeat accuracy, often down to fractions of a millimeter. This is paramount for positioning tasks in CNC machining, robotics, or high-speed assembly where millimeter precision dictates quality and throughput. They consistently perform millions of operations without drift.
- Unmatched Robustness: Designed to endure the harshest realities of the factory floor. Many feature stainless steel housings, special coatings, and industry-leading IP68, IP69K, and IP67 ratings – shrugging off high-pressure washdowns (crucial in food & beverage or pharma), corrosive coolants, pervasive oils, grinding dust, and relentless vibrations. Durability is non-negotiable.
- Superior Immunity: Industrial environments are electrically noisy battlegrounds. Balluff sensors excel with exceptional immunity to electromagnetic interference (EMI) generated by welding equipment, variable frequency drives (VFDs), and powerful motors. This ensures reliable operation where lesser sensors might falter, reducing costly false signals or dropouts.
- Extended Sensing Ranges: Balluff pushes the boundaries, offering a broad selection of sensors with industry-leading sensing ranges. This provides greater flexibility in machine design, allowing for easier installation, maintenance access, or detecting objects from safer distances, enhancing both efficiency and safety.
- Specialized Solutions for Extreme Conditions: Need detection in a foundry furnace zone? Inside a high-pressure hydraulic cylinder? Balluff has you covered. Their portfolio includes sensors specifically hardened for extreme temperatures (both high and low), capable of withstanding immense pressure (like those rated for hydraulic applications), or designed for flush mounting in tight spaces. Application-specific engineering solves niche challenges.
Where Precision Meets Practice: Key Applications
The versatility and robustness of Balluff inductive proximity sensors make them indispensable across countless sectors:
- Automotive Manufacturing: Position verification of metal components on moving pallets, robot end-of-arm tooling detection, cylinder position feedback in presses, presence sensing in welding cells. Precision position sensing is critical.
- Packaging & Material Handling: Detecting metal cans or foil lids on high-speed conveyors, confirming case presence before sealing, monitoring fill levels in metal containers, controlling sorting gates. Reliable object detection drives efficiency.
- Machine Tool & Metalworking: Tool breakage detection (monitoring spindle tool presence), workpiece clamping confirmation, pallet positioning on CNC machines, safety door monitoring. Protecting machinery and personnel is paramount.
- Food & Beverage Processing: Detecting metal tags on returnable containers (despite washdown chemicals), verifying metal lids are seated correctly before capping, monitoring valve positions in stainless steel processing lines. Hygienic design and washdown resistance are essential.
- Mobile Hydraulics: Precise cylinder position feedback in excavators, loaders, and agricultural machinery operating in dusty, wet, and shock-prone environments. Ruggedness and reliability under harsh conditions are key.
Beyond Detection: Intelligence and Connectivity
Modern Balluff inductive sensors often incorporate smart features:
- IO-Link Integration: Many Balluff sensors feature IO-Link communication, transforming them from simple switches into intelligent data points. This enables remote parameterization (adjusting sensitivity without tools), real-time diagnostic data transmission (health status, temperature, operating hours), and seamless integration into Industrial Internet of Things (IIoT) architectures for predictive maintenance and process optimization. Smart sensors create smarter factories.
- Analog Output Options: Beyond simple on/off switching, some models offer analog outputs (e.g., 4-20mA, 0-10V), providing continuous distance measurement relative to the target, valuable for precise positioning tasks.
Selecting the Right Balluff Inductive Sensor: Key Considerations
Choosing the optimal sensor involves evaluating:
- Target Material: Ferrous steel offers the longest range; non-ferrous metals (aluminum, brass, copper) have shorter ranges. Verify the sensor’s specifications for your target material.
- Required Sensing Distance: Choose a sensor whose nominal sensing range comfortably exceeds your application’s actual gap, considering installation tolerances and potential target variations.
- Mounting Constraints: Cylindrical (threaded barrel), rectangular, block-style? Flush or non-flush mounting? Ensure the form factor fits the available space.
- Environmental Conditions: Temperature extremes? Washdown? Pressure? Chemicals? Vibration? Select the housing material (stainless steel, nickel-plated brass, PBT plastic) and protection rating (IP67, IP68, IP69K) accordingly.
- Electrical Requirements: Output type needed (NPN/PNP, NO/NC)? Voltage range (typically 10-30V DC)? Connection type (cable, M8/M12 connector)?
- Special Features: IO-Link? Analog output? High-temperature rating? High-pressure resistance? Extreme durability?
From the unforgiving heat of a foundry to the sterile chill of a cleanroom, within high-pressure hydraulics or on blisteringly fast packaging lines, Balluff inductive proximity sensors deliver unwavering reliability. Their precision detection, legendary robustness, resilience against electromagnetic interference, and adaptability through specialized variants and smart capabilities make them more than just components – they are fundamental enablers of efficiency, quality, and safety in modern automation. When the margin for error is zero and uptime is critical, specifying a Balluff sensor isn’t just a choice; it’s an investment in seamless, dependable, high-performance industrial automation. Their silent vigilance ensures the machines that