pnp inductive proximity sensor
- time:2025-07-04 04:01:14
- Click:0
Demystifying PNP Inductive Proximity Sensors: The Workhorse of Contactless Detection
Imagine a high-speed packaging line suddenly halting because a critical metal component wasn’t in place. Or a robotic arm colliding because it misjudged the location of a fixture. Costly downtime, potential damage, safety hazards – these are the nightmares PNP inductive proximity sensors are designed to prevent. As fundamental components in countless industrial automation, manufacturing, and machinery applications, these robust devices offer a reliable, contactless way to detect the presence or absence of metallic objects. But what exactly are they, and why is the “PNP” designation so important? This article dives into the core functionality, advantages, and typical uses of PNP inductive proximity sensors.
The Core Principle: Eddy Currents at Work
At the heart of every inductive proximity sensor lies a simple yet elegant principle: electromagnetic induction. The sensor contains an oscillator circuit that generates a high-frequency electromagnetic field emanating from its active face (the sensing surface). When a ferrous metal target (like iron or steel) or a non-ferrous metal target (like aluminum, brass, or copper) enters this field, tiny circulating currents called eddy currents are induced on the surface of the target. These eddy currents absorb energy from the sensor’s oscillating field.
This energy absorption causes a measurable change – typically a damping or reduction – in the amplitude of the sensor’s oscillation. An internal evaluation circuit continuously monitors this amplitude. Once the damping exceeds a pre-defined threshold (indicating the target is within the specified sensing distance), the sensor triggers its output state. Crucially, all this happens without any physical contact between the sensor and the target, making these sensors incredibly durable and immune to wear. They are essentially solid-state switches, offering long service life in harsh conditions.
Unpacking “PNP”: The Output Configuration
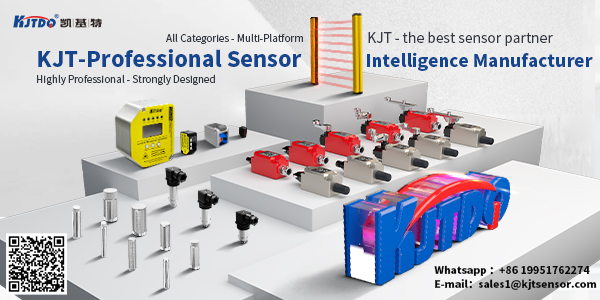
The term “PNP” (Positive-Negative-Positive) refers specifically to the transistor switching configuration used in the sensor’s output stage. This designation is critical for correctly integrating the sensor into a control system’s electrical circuit. Here’s the key distinction:
- PNP Output (Sourcing): When the sensor detects a target (switches “ON”), it connects the output signal line to the positive supply voltage (V+). Think of it as sourcing the positive voltage to the load (like a PLC input, relay coil, or indicator lamp). The load must be connected between the sensor’s output wire and the negative supply (0V).
- NPN Output (Sinking): Conversely, an NPN sensor, when “ON”, connects the output signal line to the negative supply (0V). It sinks the current from the load. The load needs to be connected between the positive supply (V+) and the sensor’s output wire.
PNP sensors are the *predominant standard in many European and North American industrial control systems*. PLC input modules are often designed to expect this sourcing signal. Always consult your control system’s specifications to determine whether PNP or NPN sensors are required, as wiring them incorrectly will prevent operation.
Key Advantages of PNP Inductive Proximity Sensors
The widespread adoption of these sensors is driven by several compelling benefits:
- Contactless Operation: Eliminates mechanical wear and tear, ensuring exceptional longevity and reliability. No moving parts susceptible to fatigue.
- High Switching Frequency: Capable of detecting rapidly moving targets or changes at high speeds, often ranging from hundreds of Hz up to several kHz, making them suitable for high-throughput automation lines.
- Robust Construction: Designed for harsh industrial environments. Typically feature stainless steel or nickel-plated brass housings and offer high IP ratings (e.g., IP67, IP68, IP69K) for excellent resistance to dust, water, oils, and coolants. Many are also resistant to vibration and shock.
- Insensitivity to Surface Conditions: Performance is generally unaffected by target surface conditions like dirt, oil, or paint (as long as it’s not metallic paint thick enough to become a target itself).
- Solid-State Reliability: The absence of mechanical contacts translates to millions of reliable switching cycles.
- Simple Installation & Wiring: Usually feature threaded barrels (M8, M12, M18, M30 are common sizes) for easy mounting and standardized cable or connector options (e.g., M12 connectors).
- Cost-Effective: Offer a very favorable price-to-performance ratio for industrial sensing tasks.
Where PNP Inductive Proximity Sensors Shine: Common Applications
Their ruggedness, speed, and reliability make PNP inductive sensors ubiquitous across industries:
- Position Verification: Confirming the presence, absence, or end-position of machine parts, cylinders (using bumper flags), slides, clamps, or pallets.
- Object Counting: Counting metallic objects on conveyors (bottles via metal caps, cans, machined parts).
- Speed Monitoring: Detecting the teeth of gears or sprockets to measure rotational speed.
- End-of-Travel Detection: Signaling when a moving part has reached its limit.
- Machine Safety: Providing part-in-place confirmation for safe machine operation sequences.
- Material Handling & Packaging: Monitoring fill levels (metal containers), detecting jams, confirming package sealing jaws are closed.
- Automotive Manufacturing: Used extensively in assembly lines for part positioning, robot guidance, and quality control checks on metal components.
- Food & Beverage (Specific Models): Utilizing special food-grade (FDA/USDA compliant) housings for hygiene-critical zones, detecting metal lids, cans, or machinery components.
Choosing the Right PNP Inductive Proximity Sensor: Key Considerations
Selecting the optimal sensor involves evaluating several factors:
- Target Material: Ferrous metals offer the longest sensing ranges. Sensing distance is reduced for non-ferrous metals like aluminum or copper (often specified as a factor, like 50% of the ferrous range). Know your target!
- Required Sensing Distance: Choose a sensor whose nominal sensing distance (Sn) comfortably exceeds the maximum air gap required in your application, typically using 70-80% of Sn for reliability. Consider factors like target size and approach direction (axial vs. lateral).
- Output Configuration: PNP output, clearly. Also decide between Normally Open (NO) or Normally Closed (NC) logic based on your control system requirements. NO is the most common.
- Housing Style & Size: Threaded barrel (M5 to M30), block, or rectangular style? Choose based on mounting constraints and space availability. M8 and M12 are incredibly versatile and popular sizes.
- Environmental Rating: Match the IP rating to the environment (dust, water jets, high-pressure washdown, temperature extremes).
- Electrical Specifications: Ensure compatibility with your system’s supply voltage (e.g., 10-30V DC is standard) and current requirements.
- Special Requirements: High temperature resistance? Extra shielding for weld immunity? Food-grade materials? Short-circuit or reverse polarity protection? Factor these in.
The Backbone of Reliable Automation
PNP inductive proximity sensors represent a mature, yet continually refined, technology. Their inherent simplicity, robustness, and reliability solidify their position as the workhorse sensor for countless metal detection tasks in demanding industrial environments. Understanding their operating principle, particularly the criticality of the