pnp nc proximity sensor
- time:2025-07-03 02:48:51
- Click:0
The Essential Guide to PNP NC Proximity Sensors: How They Work & Where to Use Them
Imagine a critical machine guarding door on a high-speed assembly line. Its safety relies on instantly knowing if that door is truly closed before powerful actuators engage. Or picture a robotic arm precisely picking components from a vibrating feeder bowl; it needs absolute certainty a part is in position before executing a delicate movement. In countless industrial situations where detecting the absence or presence of an object is paramount, PNP NC proximity sensors are the unsung heroes providing that vital, fail-safe signal. Understanding their unique behavior is key to unlocking their potential in your applications.
Decoding the Acronym: PNP NC
Let’s break down what “PNP NC” actually means:
- Proximity Sensor: A non-contact sensing device that detects the presence or absence of a target object (usually metallic) within its sensing range without physical touch. They work based on electromagnetic fields (inductive type, most common for metals), capacitive effects, or ultrasonic waves.
- PNP (Sourcing Output): This refers to the transistor output type within the sensor.
- A PNP sensor acts like a switching source of positive (+) voltage relative to the common ground (0V).
- When active (target detected), the PNP output transistor connects the output signal wire directly to the positive supply voltage (+V).
- Think: “Positive Switched Positive”. It sources current to the load (like a PLC input, relay coil, or indicator lamp). The load is connected between the sensor output and the ground (0V).
- NC (Normally Closed): This defines the default electrical state of the sensor’s output circuit when no target is present in its sensing field.
- NC means the output circuit is closed (like a switch turned ON) when no target is detected. Current can flow from the output to the load.
- When a target enters the sensing field, a Normally Closed sensor’s output circuit opens (like a switch turning OFF), stopping the current flow. This transition from closed to open signifies detection.
Therefore, a PNP NC proximity sensor combines these traits:
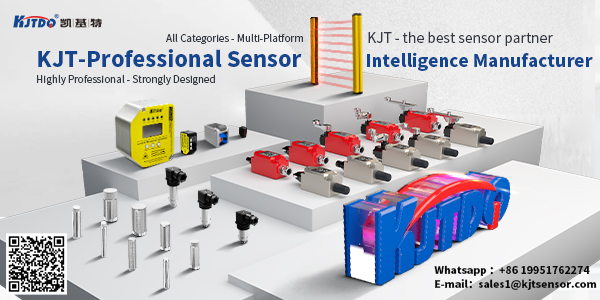
- Outputs +V (Sourcing) when active.
- Its output circuit is CLOSED (conducting) when NO target is near (resting state).
- Its output circuit OPENS (stops conducting) when a target IS detected.
The Critical Logic: Why Choose Normally Closed?
The defining characteristic of an NC configuration is its inherent fail-safe nature for critical detection scenarios. This is its primary advantage and dictates its ideal use cases:
- Detecting Absence is Safer: Often, confirming that something is missing or not in place is more critical for safety or process integrity than confirming its presence. An NC sensor provides a continuous “OK” signal (closed circuit) only when the monitored object is absent. A break in this signal (open circuit) immediately alerts the system to a problem.
- Wire Break Detection: If the signal wire connecting a PNP NC sensor to the control system (like a PLC) gets severed, the circuit opens. This mimics the behavior of the sensor detecting a target. Therefore, a wire break on a PNP NC sensor inherently triggers the “alarm” or “fault” state (output off/open). This is crucial for safety applications where an undetected wire failure could lead to dangerous operation. A Normally Open (NO) sensor would fail “silent” in a wire break scenario, potentially hiding a critical issue.
- Power Loss Behavior: Similar to wire break, if the sensor loses power, the output circuit inherently opens. Again, this defaults to the “detected” or “fault” state, enhancing safety. Contrast this with an NO sensor losing power, which would be unable to signal detection.
Key Applications Capitalizing on PNP NC Strengths
PNP NC proximity sensors shine in situations demanding high reliability and fail-safe operation:
- Machine Guarding & Safety Interlocks: As mentioned in the opening example. Door closed? An NC sensor confirms it by keeping the safety circuit closed. If the door opens (or the wire breaks/power fails), the circuit opens, triggering an immediate machine stop (E-Stop signal). Position verification of physical guards also uses NC logic.
- Presence Verification for Process Start: Must confirm a part is removed from a fixture before clamping or starting a cycle? An NC sensor positioned where the part shouldn’t be provides a “cycle start OK” signal only when the fixture is clear.
- End-of-Travel or Over-Travel Limits: Detecting when a moving part (cylinder, slide) has fully retracted to a safe “home” position is often critical before reversing direction or starting a new action. An NC sensor confirms the home position by being covered (output open = position verified).
- Material Run-Out / Break Detection: Monitoring the presence of a continuous web (metal strip, film, paper – often using capacitive sensors configured as NC). The absence of material (break) causes the NC sensor’s output to open, signaling a fault. A break in the sensor wiring also causes the same fault signal.
- Tray or Pallet Position Confirmation: Ensuring a pallet has been removed from a loading/unloading station before initiating the next sequence.
Advantages Summarized: Why Opt for PNP NC?
- Inherent Fail-Safe Design: Wire breaks or power loss trigger the “fault/alert” state automatically. This is paramount for safety and critical process monitoring.
- Ideal for Vital “Absence” Detection: Functionally designed to signal when something is missing or not in the correct safe position.
- Compatibility: PNP outputs are widely compatible with modern PLCs and control systems designed for sourcing inputs. NC logic is well-understood in safety circuit design.
- Reliability: Provides a continuous “heartbeat” signal under normal conditions, making loss of signal immediately apparent.
Selecting and Implementing Your PNP NC Sensor
When choosing and installing a PNP NC proximity sensor, consider these factors:
- Sensing Type: Inductive (metals only), capacitive (metals, plastics, liquids, powders), ultrasonic (solid objects, level)? Match the technology to your target material.
- Sensing Range: Choose a range appropriate for the application, considering mounting constraints and potential target variations. Remember, NC sensors trigger when a target enters this range.
- Output Current Rating: Ensure the PNP NC sensor can handle the current required by the connected load (PLC input module, relay, etc.). PNP sensors source current.
- Electrical Specifications: Voltage rating (e.g., 10-30V DC), current consumption, switching frequency.
- Environmental Factors: IP rating (dust/water ingress protection), temperature range, resistance to chemicals, shock, and vibration. Flush or non-flush mounting (for inductive sensors) matters near metal surroundings.
- Connection: Ensure correct wiring. For a PNP NC sensor:
- Connect Brown wire (+V Supply) to DC positive.
- Connect Blue wire (0V / Common) to DC negative/ground.
- Connect Black wire (Output Signal) to your PLC input (or load terminal).
- Crucial: Your PLC input (or connected device) must be configured to interpret the *