npn nc proximity sensor
- time:2025-07-03 02:54:52
- Click:0
Demystifying NPN NC Proximity Sensors: The Reliable “Normally Closed” Workhorse
Imagine a crucial machine needing to stop instantly if a safety guard is opened. Or a conveyor belt system that must pause if a part is unexpectedly present. In these critical moments, reliability isn’t just desired; it’s imperative. This is where the NPN NC (Normally Closed) proximity sensor shines. It’s a specific type of non-contact switch designed for dependable operation and enhanced safety in demanding industrial environments. Understanding its function, advantages, and applications is key to selecting the right sensor for robust automation.
Beyond the Touch: The Core Principle
At its heart, a proximity sensor detects the presence or absence of a metallic target object without physical contact. It achieves this using an electromagnetic field generated by a coil inside the sensor head. When a conductive metallic target enters this sensing field, electromagnetic induction (in the case of inductive sensors) causes changes in the sensor’s internal oscillator circuit. This change is detected, triggering the sensor’s switching circuitry.
Decoding “NPN”: The Transistor Output Driver
The “NPN” designation is crucial and refers to the type of transistor used in the sensor’s output stage and how it interfaces with the control system (like a PLC - Programmable Logic Controller). Here’s what NPN means:
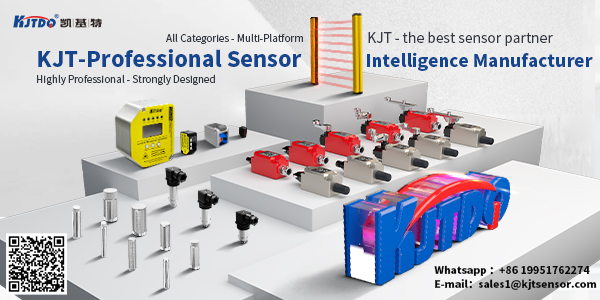
- Open Collector Output: An NPN sensor features an open collector output transistor. Think of it as a switch inside the sensor connected to the negative (0V) side of the power supply.
- Current Sinking Operation: When the sensor is active (target detected), the NPN transistor turns ON. This effectively “closes” the switch, connecting the sensor’s output wire (usually the black or brown wire) directly to the negative supply rail (0V). This allows current to flow out of the connected load (e.g., the PLC input module) into the sensor’s output and down to ground. Hence, NPN sensors are known as current sinking sensors. When inactive (no target), the transistor is OFF, leaving the output disconnected (open circuit).
Understanding “NC”: The Normally Closed State
The “NC” stands for Normally Closed. This describes the default electrical state of the sensor’s output contacts when no target is present within its sensing range.
- No Target Present (Normal State): The output circuit is electrically closed. If you connected a multimeter across the output and the positive supply, you’d see continuity. Current can flow through the sensor’s output circuit back to the power source.
- Target Detected (Active State): The presence of the target causes the sensor to open the output circuit. The internal “switch” breaks the connection. This is the switching action.
Why Choose NPN NC? Key Advantages and Rationale
The combination of NPN output and Normally Closed configuration offers distinct benefits, especially for safety-critical applications:
- Fail-Safe Operation: This is the primary advantage. If the sensor fails completely (e.g., loses power, internal fault, wire break), the output circuit reverts to its “closed” state. In a safety circuit wired to monitor this closed state, the failure itself triggers the safety response (e.g., machine shutdown). This inherently safer design is why NC circuits are often mandated for safety guarding and emergency stop monitoring. An NO sensor failing would simply look like “no target present,” potentially failing dangerously.
- No Power Consumption (Idle State): In its default (no target) NC state, the sensor itself typically draws minimal current through its internal switch. While the connected load might be powered, the sensor’s active circuitry isn’t constantly energized for switching.
- Wiring Compatibility (Often): NPN sensors are traditionally very common in regions like Europe and Asia, making them readily compatible with many PLCs and controllers designed to accept sinking inputs.
- Noise Immunity: Solid-state transistor outputs are generally less susceptible to electrical noise compared to mechanical relays, offering reliable switching in electrically noisy industrial settings.
Putting It Into Practice: Common Applications
NPN NC proximity sensors excel in scenarios demanding safety and reliability:
- Safety Interlocking: Monitoring the closed position of machine guards, safety doors, or enclosures. A guard opening breaks the target presence, opening the sensor output, signaling the PLC to stop the machine.
- End-of-Travel Detection: Verifying that a moving part (like a cylinder) has fully retracted (sensor detects target) before allowing another sequence to start. The NC state ensures a fault stops the cycle.
- Emergency Stop Monitoring: Integrated into E-stop circuits where a wire break or sensor failure must trigger an immediate shutdown.
- Presence Verification for Process Start: Ensuring a part is correctly positioned (and absent from a forbidden zone) before initiating a process. The NC configuration might signal “clear to proceed” only when the zone is empty.
- Jam Detection: Detecting when a part hasn’t moved past a point within an expected timeframe (target remains absent, NC state persists, triggering an alarm/shutdown).
Installation & Considerations
- Wiring: Connect the Brown wire (+) to the positive DC supply voltage (typically 10-30V DC), the Blue wire (-) to the negative (0V) supply. Connect the Black output wire (NPN NC) to the PLC input point designed for sinking signals. The PLC input module usually provides the positive voltage source via its internal circuitry; the sensor connects it to ground when active/switched.
- Sensing Range: Ensure the target material (usually ferrous metal like iron or steel is most detectable) and size are appropriate for the sensor’s specifications. Non-ferrous metals require sensors specifically designed for them or have significantly reduced ranges.
- Environment: Consider factors like temperature, humidity, chemicals, and potential shielding effects from surrounding metal. Choose sensors with appropriate IP (Ingress Protection) ratings.
- Mounting: Secure the sensor firmly to prevent vibration-induced false signals. Ensure the target approaches perpendicularly within the specified sensing distance.
NPN NC vs. Others: A Quick Clarification
- NPN NO: Normally Open. Output is OFF/open circuit when no target, ON/closed to ground when target detected. Not inherently fail-safe for safety circuits.
- PNP NC: PNP sensors source current (connect output to positive when active). PNP NC opens the circuit to positive when target detected. Also offers NC fail-safe but uses sourcing logic. Common in North America.
- PNP NO: PNP Normally Open. Output is OFF/open when no target, connects to positive (sources current) when target detected.
Conclusion
The NPN NC proximity sensor isn’t just a component; it’s a cornerstone of reliable and safe industrial automation. Its defining characteristic – switching open when a target is detected while being closed by default – combined with current sinking (NPN) operation, makes it an indispensable tool, particularly where failsafe operation is paramount. Understanding the nuances of its NPN NC label empowers engineers and technicians to design control systems that prioritize safety, reliability, and efficient machine operation. When your application demands that a fault leads to a safe stop, the NPN NC sensor is often the clear and robust choice.