analog inductive proximity sensor
- time:2025-07-03 01:00:29
- Click:0
The Power of Analog Inductive Proximity Sensors: Unlocking Precision in Industrial Detection
Imagine a high-speed assembly line where metal components whiz by. A traditional on/off switch might miss a slightly misaligned part, causing costly jams or defects. But what if a sensor could not only detect the presence of that metal component but also measure exactly how close or far away it is during its approach? That’s the critical capability provided by analog inductive proximity sensors, transforming simple detection into actionable intelligence for sophisticated automation.
Unlike their simpler digital counterparts that offer a straightforward “target present/target absent” signal, analog inductive proximity sensors provide a continuous output signal directly proportional to the distance between the sensor’s face and the conductive target object. This continuous feedback unlocks a world of possibilities far beyond mere presence detection, enabling precision control and monitoring in demanding industrial environments.
How Analog Inductive Proximity Sensors Achieve This Magic
At their core, all inductive proximity sensors rely on the same fundamental inductive sensing principle:
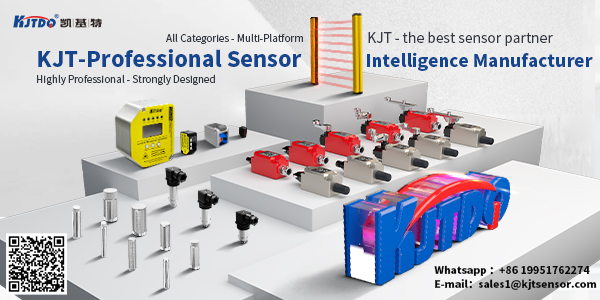
- Oscillating Field Generation: The sensor contains a coil (inductor) energized by an oscillator circuit, creating a high-frequency electromagnetic field emanating from its active face.
- Eddy Currents & Damping: When a conductive target object (typically ferrous or non-ferrous metal) enters this field, it induces tiny circulating electrical currents called eddy currents within the target material.
- Energy Loss Detection: The creation of these eddy currents absorbs energy from the sensor’s oscillating circuit, causing a measurable damping (energy loss) effect.
- Signal Processing: Electronic circuitry within the sensor monitors the magnitude of this damping effect.
Here’s where the “analog” difference becomes clear:
- Digital Sensors: Measure if the damping exceeds a fixed threshold. Output: Simple on/off switch signal.
- Analog Sensors: Precisely measure the degree of damping. Output: A continuous output signal (typically voltage, e.g., 0-10V, or current, e.g., 4-20mA) that changes linearly with the distance between the sensor and the target within its defined sensing range.
Why Choose Analog Over Digital? Key Advantages
The continuous output signal of an analog inductive proximity sensor delivers significant benefits where precise positioning or distance monitoring is paramount:
- Distance Measurement & Monitoring: Directly measure how far away a metal object is. This is invaluable for tasks like monitoring brake pad wear, checking valve positions, controlling robotic arm movement relative to a part, or ensuring precise tool positioning in machining centers. The sensor provides real-time feedback within microns.
- Position Control: Enable proportional or closed-loop position control systems. Instead of just triggering an action at a single point, analog sensors allow systems to react proportionally to position changes – like smoothly controlling actuator speed as a part nears its final position.
- Vibration Damping & Runout Detection: Monitor subtle variations in distance caused by shaft oscillation, bearing wear, or part eccentricity. The analog output reveals trends and magnitudes that a simple digital switch signal would miss entirely. Detecting these nuances early is crucial for predictive maintenance.
- Material Thickness Detection: Under controlled conditions, the analog signal can correlate with the thickness or composition of the conductive material passing by the sensor face, useful in rolling mills or quality checks.
- Smoother Process Control: Replace multiple discrete digital sensors with a single analog sensor for applications requiring measurement across a range, simplifying setup and providing richer data for process optimization.
Where Analog Inductive Proximity Sensors Shine: Applications
The unique capabilities of these sensors make them ideal for numerous demanding industrial scenarios:
- Precision Machinery: Monitoring tool wear, workpiece positioning, spindle runout, and clamp pressure in CNC machines, grinders, and presses. Ensuring micron-level accuracy is critical.
- Automotive Manufacturing: Checking cylinder liner protrusion, controlling robotic welder standoff distance, verifying door panel alignment, detecting brake disc thickness variation, and monitoring suspension component travel. Consistency and precision are non-negotiable on the assembly line.
- Material Handling & Packaging: Verifying stack heights, controlling filling levels (metallic containers), guiding robotic palletizers, and ensuring precise positioning of metal parts on conveyors. Preventing costly errors and optimizing speed.
- Hydraulic & Pneumatic Systems: Continuously monitoring cylinder piston position for accurate movement control and feedback. Essential for smooth, controlled automation.
- Wood & Paper Industry: Monitoring blade position, detecting metal contaminants within non-metallic materials, and controlling roll positioning.
- General Automation: Any application demanding continuous position feedback from metallic objects without physical contact, especially where harsh environments (dust, oil, vibration) rule out optical or mechanical solutions.
Selecting the Right Sensor: Important Considerations
Choosing the optimal analog inductive proximity sensor involves several factors:
- Sensing Range: The distance over which the analog signal is linear and proportional. Ensure the sensor’s range meets your application’s maximum and minimum distance requirements. Target size significantly impacts achievable range.
- Output Signal Type: Common options are voltage (0-10V, often based on PNP switching) or current (typically 4-20mA). Choose based on compatibility with your PLC, controller, or data acquisition system. 4-20mA is often preferred for long cable runs due to its noise immunity.
- Linearity & Repeatability: How accurately and consistently the output signal represents the actual distance? High-precision applications demand sensors with excellent linearity and repeatability specifications.
- Target Material: While all inductive sensors detect conductive metals, the specific material (steel, aluminum, copper, brass) affects sensing range and sensitivity. Confirm the sensor’s specifications for your target material. Non-conductive targets require capacitive sensors.
- Operating Environment: Consider temperature extremes, potential exposure to cutting fluids, coolants, oils, welding spatter, dust, vibration, and shock. Ensure the sensor housing (stainless steel preferred), protection rating (IP67/IP68 common), and temperature range are suitable.
- Mounting & Size: Flush or non-flush mounting capability? What are the space constraints? Flush-mount sensors can be embedded in metal, non-flush types offer longer ranges.
Harnessing Continuous Feedback for Smarter Automation
Analog inductive proximity sensors are far more than just detectors; they are sophisticated measurement tools. Their ability to provide a continuous, proportional output signal reflecting the precise distance to a metallic target unlocks a level of control and insight that simple on/off detection cannot match. From ensuring micron-level accuracy in machining to enabling smooth robotic movement and providing early warnings of mechanical wear through vibration analysis, these robust sensors are indispensable components in modern, data-driven, and precision-focused industrial automation. By converting the subtle changes in an electromagnetic field into actionable analog data, they empower engineers to build smarter, more efficient, and more reliable systems.