pnp proximity sensor
- time:2025-07-01 14:22:31
- Click:0
PNP Proximity Sensors: Your Go-To Guide for Sourcing Output Operation
Imagine a robotic arm smoothly placing components on a circuit board, never missing a beat. Or a production line counting bottles with uncanny accuracy. Behind these seamless operations often lies a critical, unsung hero: the PNP proximity sensor. These remarkable devices detect the presence or absence of objects without physical contact, silently ensuring processes run smoothly and safely. But with different output types available, understanding the PNP configuration is crucial for successful automation system design. This guide dives deep into the world of PNP proximity sensors, explaining their operation, advantages, and where they shine.
Understanding the Core: What is a Proximity Sensor?
At its heart, a proximity sensor is an electronic device designed to detect the presence or absence of an object within a set distance – its sensing range – without needing physical touch or direct exposure. They achieve this through various principles, the most common being inductive sensing for metallic targets and capacitive sensing for both metal and non-metal objects. These sensors generate an electromagnetic field (inductive) or electrostatic field (capacitive), and a change in this field caused by a target object entering the detection zone triggers the sensor’s output state. The key takeaway? Contactless detection, leading to reliability, longevity, and freedom from mechanical wear.
The “PNP” Distinction: Sourcing the Signal
The acronym “PNP” specifically refers to the type of transistor output used within the sensor’s electronics. It stands for “Positive-Negative-Positive,” describing the semiconductor structure. In practical terms for wiring and system integration, this translates to a sourcing output.
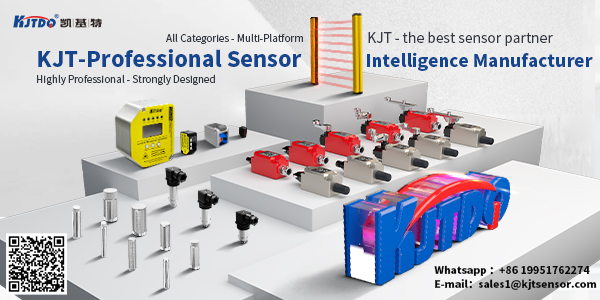
- Sourcing Output Explained: When an object is detected (the sensor is “on”), a PNP sensor sources or provides positive voltage (+V) on its output signal wire. Think of it as the sensor connecting the output wire to the positive supply rail when active.
- The Load Connection: To complete the circuit, the load (like a PLC input module, relay coil, or indicator lamp) must be connected between the sensor’s output wire and the negative supply terminal (usually 0V or Ground). When the sensor switches on, current flows from the sensor’s output (source) through the load to ground. This is sometimes called an active-high logic output.
Why does this matter? It defines how the sensor integrates into your control system and dictates the wiring configuration. Choosing between PNP and its counterpart, NPN, is fundamental.
PNP vs. NPN: Choosing the Right Output Type
The main alternative is the NPN proximity sensor, which features a sinking output. Understanding the difference is critical:
- PNP (Sourcing):
- Output provides +V when active.
- Load connects between OUTPUT and GND (0V).
- Common in Europe and many industrial PLCs.
- Often preferred for directly driving indicator lamps or relays with simple power supplies.
- NPN (Sinking):
- Output connects to GND (0V) when active (sinks current).
- Load connects between +V and OUTPUT.
- Common in Asia and with some PLC types.
- Can be advantageous in specific safety circuits or when interfacing with certain legacy controls.
Key Advantage of PNP: A significant benefit of the PNP configuration is related to fault behavior. If the wire connecting the sensor’s output to the load becomes severed or disconnected, a PNP sensor typically causes the load to turn off. In contrast, NPN sensors can sometimes cause a faulty “on” state under wire-break conditions. This inherent behavior often makes PNP the preferred choice in many safety-related or critical applications where a fail-safe off state is desirable. However, always consult safety standards and perform risk assessments, as definitive safety requires certified safety devices and proper design.
Where Do PNP Proximity Sensors Excel? Applications Galore
The robustness and contactless nature of proximity sensors, combined with the sourcing output of PNP types, make them indispensable across countless industries. Here’s where you’ll find them hard at work:
- Industrial Automation: The undisputed champion application area.
- Object Detection:
- Position Verification: Confirming cylinders are retracted/extended, detecting part presence in fixtures or guides.
- Counting: Accurately tallying products on conveyors (e.g., bottles, boxes).
- Speed Monitoring: Detecting teeth on gears or markers on rotating shafts to calculate RPM.
- Level Detection: Sensing the fill level of liquids or bulk materials in tanks (using capacitive sensors).
- End-of-Travel Detection: Signaling when a moving part (like a slide or door) has reached its limit.
- Packaging Machinery: Ensuring cartons are correctly positioned before sealing, detecting film breaks, verifying cap presence.
- Automotive Manufacturing: Monitoring robotic arm positions, confirming part insertion (e.g., pistons into blocks), checking door/window alignment.
- Material Handling: Detecting pallets on conveyors, verifying box flaps are closed, controlling gate positions.
- Machine Tools: Monitoring tool changers, confirming workpiece clamping, checking coolant levels.
- Building Automation: Detecting door positions for security systems, monitorin* level detection applications like paper in copiers or water in dispensers.
Their ability to operate reliably in harsh environments – tolerant of dust, oil, vibration, and temperature variations (within specified limits) – makes them ideal for dirty, demanding industrial settings where mechanical switches would quickly fail.
Selecting and Implementing Your PNP Proximity Sensor
Choosing the right PNP sensor involves several critical factors beyond just the output type:
- Sensing Principle: Inductive for metals only, Capacitive for metals/non-metals/liquids, Ultrasonic for longer-range detection, Photoelectric for beam interruption or reflection.
- Sensing Range: Ensure the rated nominal sensing distance (Sn) comfortably exceeds your application’s required gap. Factor in temperature effects and target material (for inductive).
- Target Material and Size: Inductive sensors are particularly sensitive to the type and size of the metal target. Capacitive sensors respond differently to various materials. Consult datasheets.
- Output Configuration: PNP is our focus, but confirm the number of wires (typically 3-wire: +V, Output, 0V) and if it has Normally Open (NO), Normally Closed (NC), or switching capability.
- Housing and Form Factor: Cylindrical (threaded barrel) and rectangular (block) are common. Consider mounting constraints, space limitations, and required IP (Ingress Protection) rating for dust/water resistance.
- Electrical Specifications: Operating voltage range (e.g., 10-30V DC), current consumption, output current capacity (how much load it can drive), voltage drop (important for long cables/PLC compatibility).
- Environmental Factors: Ambient temperature range, resistance to chemicals, shock