cylinder proximity sensor
- time:2025-07-01 14:28:33
- Click:0
Unlocking Precision & Reliability: The Essential Guide to Cylinder Proximity Sensors
Imagine a critical assembly line grinding to a sudden halt. Bottles shatter, components jam, and costly downtime ticks away. The culprit? A simple failure to detect the precise position of a hydraulic cylinder piston. This frustrating, avoidable scenario underscores why cylinder proximity sensors are the unsung heroes of modern automation, ensuring smooth, efficient, and reliable motion control. These ingenious devices silently monitor cylinder rod position, providing vital feedback that keeps machinery synchronized, safe, and productive.
At its core, a cylinder proximity sensor is a specialized type of non-contact sensing device designed explicitly for detecting the position of a pneumatic or hydraulic cylinder’s piston rod or internal piston. Unlike mechanical limit switches prone to wear and physical failure, proximity sensors operate using electromagnetic principles, creating a robust and maintenance-free solution essential for demanding industrial environments. The most common technology employed is inductive sensing, where an oscillating electromagnetic field generated by the sensor reacts to the presence of a conductive metal target – typically the cylinder’s piston rod or a designated target flag mounted on it.
Here’s how it typically works:
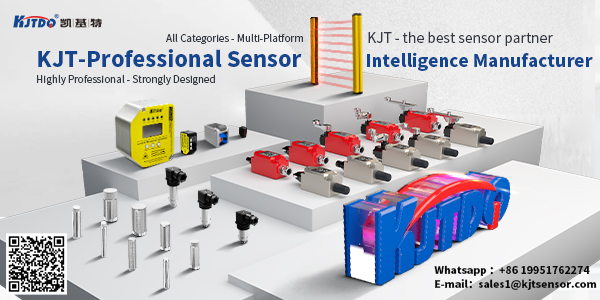
- Field Generation: An internal coil within the sensor head is energized with an alternating current, creating an oscillating electromagnetic field extending slightly beyond the sensor face.
- Target Interaction: When a metal target (the piston rod or target flag) enters this active field zone, eddy currents are induced within the target material.
- Field Dampening & Detection: These eddy currents draw energy from the sensor’s oscillating field, causing a measurable dampening of the field amplitude and often a shift in frequency.
- Signal Switch: The sensor’s integrated electronic circuitry detects this change and triggers a solid-state switching action (e.g., NPN/PNP transistor output). This clean electrical signal reliably indicates the target’s presence or absence.
For cylinder sensing, two main configurations dominate:
- Rod Sensing: The sensor is mounted externally on the cylinder body, detecting the movement of the cylinder rod itself as it extends or retracts past the sensor face. This requires the rod to be made of a ferrous metal (like steel).
- Piston Sensing (Magnetic): A sensor is mounted within a groove on the cylinder barrel. Instead of detecting the rod, it senses the magnetic field generated by a permanent magnet embedded within the piston. This method, often using reed switches or specialized cylinder sensors with integrated magnets, allows position detection even with non-ferrous rods (stainless steel, chrome-plated) and provides detection right at the piston’s location.
The critical role of cylinder proximity sensors manifests in numerous vital applications:
- End-of-Stroke Verification: Confirming a cylinder has fully extended or retracted before initiating the next machine sequence is fundamental to process integrity and preventing collisions or jams. Sensors at both ends provide this crucial confirmation.
- Mid-Stroke Position Feedback: For cylinders requiring intermediate stops or position verification, strategically placed sensors deliver precise feedback on piston location.
- Sequencing Control: Accurate position signals from multiple cylinders enable complex, synchronized machine movements essential in assembly, packaging, and material handling.
- Safety Interlocks: Sensors can verify cylinders are in a safe “home” or “parked” position before granting access to machine guards or initiating potentially hazardous operations.
- Preventing Over-Travel: Detecting a cylinder at its fully extended point helps prevent mechanical stress and potential damage caused by over-pressurization or misalignment.
Choosing the right cylinder proximity sensor involves several key considerations:
- Sensing Principle: Rod sensing vs. Magnetic Piston sensing, based on cylinder construction and required detection point.
- Mounting: Cylinder proximity sensors often feature specialized bracketless mounting options like clamp bands, slide-in grooves, or threaded barrels designed to integrate seamlessly with standard ISO cylinder profiles.
- Environmental Factors: Sensors must withstand industrial challenges like vibration, temperature extremes, washdown conditions (IP67/IP68/IP69K ratings), and exposure to cutting fluids or hydraulic oils. Selecting sensors with robust housings (stainless steel PBT plastic) and appropriate ingress protection is essential.
- Electrical Specifications: Output type (NPN/PNP, NO/NC), operating voltage range (commonly 10-30V DC), and cable/connector type must match the control system requirements. DC 3-wire sensors are the industry standard.
- Sensing Distance: The nominal sensing range must be suitable for the target material and mounting position. Shielded sensors offer flush mounting capabilities but shorter ranges, while unshielded provide longer ranges but require more clearance.
The advantages of using dedicated cylinder proximity sensors over mechanical alternatives are compelling:
- Zero Contact, Zero Wear: Non-contact operation eliminates mechanical wear and tear, dramatically increasing lifespan and reducing maintenance.
- High-Speed Switching: Capable of detecting targets moving at very high speeds, ideal for fast-cycling machinery.
- Environmental Resilience: Sealed units resist dirt, dust, moisture, and vibration far better than mechanical switches.
- Repeatability & Precision: Delivers highly consistent and precise switching points, critical for automation accuracy.
- Simple Installation & Setup: Modern designs with standardized mounting often allow for tool-free adjustment and secure fastening directly onto the cylinder.
Integrating a cylinder proximity sensor involves mounting it securely, aligning it correctly with the target path, and connecting its output to the machine’s Programmable Logic Controller (PLC) or other control device. Careful attention to alignment and ensuring the sensor operates within its specified sensing range guarantee reliable performance. Their outputs provide the discrete signals that form the backbone of reliable sequence control and safety logic in countless automated systems.
From factory robots performing delicate assembly tasks to heavy-duty presses shaping metal, cylinder position feedback provided by these sensors is indispensable. They transform simple linear actuators into intelligent, feedback-driven components. Whether ensuring a gripper is fully retracted before a conveyor starts or verifying a stamping die is safely open, the humble cylinder proximity sensor is a fundamental building block of efficient, safe, and profitable automation. Selecting, installing, and maintaining these sensors correctly is not just a technical detail; it’s an investment in operational continuity and peak machine performance. Their silent vigilance is a key ingredient in the smooth, uninterrupted rhythm of modern manufacturing and processing.