photoelectric sensor working
- time:2025-07-25 03:29:20
- Click:0
Seeing the Light: Demystifying How Photoelectric Sensors Work
Within the intricate dance of modern automation, countless tasks rely on unseen sentinels – devices that detect presence, absence, position, or color without physical contact. Among the most versatile and widely used are photoelectric sensors. But how exactly does this ubiquitous piece of industrial technology translate light into actionable data? Understanding the photoelectric sensor working principle is key to appreciating its role and selecting the right tool for the job.
At its most fundamental level, a photoelectric sensor operates on a surprisingly simple concept: it emits a beam of light and detects changes in that light’s properties when an object interrupts or alters it. Yet, beneath this simplicity lies sophisticated engineering that enables reliable operation in diverse and often challenging environments. Every photoelectric sensor comprises two core components: an emitter (light source) and a receiver (light detector). The intricate interplay between these elements defines its functionality.
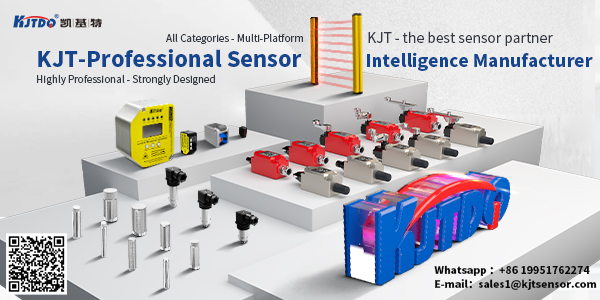
The Core Mechanism: Light Emission and Reception
- Light Emission: The emitter, typically a Light Emitting Diode (LED), generates the sensing beam. While visible red light is common for ease of alignment, infrared light (IR) is extremely prevalent due to its invisibility and resistance to ambient light interference. Specialized sensors might use laser diodes for precise targeting or colored LEDs (red, green, blue) for color discrimination tasks. Crucially, the emitted light is often modulated – pulsed at a specific high frequency. This modulation allows the sensor’s receiver circuitry to distinguish the sensor’s own light signal from constant background or ambient light sources (like sunlight or room lighting), significantly boosting reliability.
- Light Reception: The receiver, usually a phototransistor or photodiode, is designed to be highly sensitive to the specific wavelength of light emitted by its paired emitter. Its primary role is to convert incoming light energy into an electrical current. The strength of this electrical signal is directly proportional to the intensity of the light striking the receiver.
- Signal Processing & Output: An integrated electronic circuit continuously monitors the electrical signal generated by the receiver. This circuit is the “brain” that interprets what the light level means. Based on predefined thresholds configured during setup (often involving potentiometers or teach-in functions), the circuit determines the sensor’s state. When the received light meets the “sufficient light” condition (or the opposite, depending on the sensing mode), the sensor triggers its output circuit. This output is typically a solid-state switch (like a transistor - PNP or NPN) that changes state (ON/OFF), providing a discrete signal usable by controllers like PLCs, robots, or counters.
The Three Pillars of Photoelectric Sensing Modes
The photoelectric sensor working principle manifests in three primary configurations, each suited to different application challenges:
- Through-Beam (Opposed Mode):
- Working Principle: The emitter and receiver are housed in separate units, positioned directly opposite each other. The emitter sends a continuous (modulated) beam straight to the receiver. The sensor’s output is triggered when an object physically interrupts this beam, blocking the light from reaching the receiver.
- Key Features: Offers the longest sensing distances (often many meters) and is generally the most reliable mode, as it depends on a simple beam break. It is less affected by the object’s surface color, reflectivity, or texture. Alignment is critical.
- Common Applications: Detecting large objects on conveyors, checking for broken parts in feeding systems, box counting, level detection in large bins, safety light curtains (a specialized form).
- Retroreflective (Reflex Mode):
- Working Principle: Both the emitter and receiver reside in the same housing. The sensor emits a light beam towards a specially designed retroreflector (a prism or tape covered in tiny corner cubes). This reflector efficiently bounces the light beam directly back to the receiver within the sensor head. The output triggers when an object interrupts the beam’s path between the sensor and the reflector.
- Key Features: Simplifies installation compared to through-beam (only one device to wire and mount, plus the reflector). Sensing distances are typically shorter than through-beam but longer than diffuse modes. Relies on the integrity of the reflector.
- Common Applications: Detecting objects on conveyors where mounting opposite sides is impractical, pallet detection, door open/close monitoring, bottle detection on filling lines.
- Diffuse (Proximity Mode):
- Working Principle: The emitter and receiver are mounted together in the same housing, angled towards the target area. Unlike retroreflective, there is no separate reflector. The sensor relies on the target object itself to diffusely reflect the emitted light beam back towards the receiver. The output triggers when sufficient reflected light is detected, indicating the presence of the target.
- Key Features: Simplest installation – only one device needs mounting. Sensing distance is the shortest of the three modes and is highly dependent on the target object’s size, color, and surface texture (light-colored, matte surfaces reflect best; dark, shiny, or absorbent surfaces are challenging). Background suppression (BGS) and foreground suppression (FGS) are advanced diffuse technologies using triangulation or time-of-flight principles to detect objects only within a specific, defined distance zone, minimizing interference from objects beyond the desired range or the background.
- Common Applications: Detecting objects at close range where mounting reflectors or opposing sensors is impossible (e.g., inside machinery, small packages), presence detection on assembly lines, label detection, fill level detection in transparent containers, object counting on vibratory feeders.
Beyond the Basics: Enhancing Reliability and Capability
Modern photoelectric sensors incorporate several features built directly into their core working principle to handle real-world complexities:
- Modulation & Synchronization: As mentioned, pulsing the emitted light at a specific frequency and tuning the receiver to only recognize that frequency filters out nearly all constant ambient light interference, allowing reliable operation even in bright sunlight.
- Polarized Light (for Retroreflective): Used with special polarized retroreflectors. The emitter sends out polarized light. The reflector twists the polarization before sending it back. The receiver has a polarized filter. This setup ensures the sensor only recognizes light bounced off the genuine reflector, ignoring reflections from ordinary shiny surfaces (like metal or plastic) that would otherwise cause false triggers. Essential for detecting shiny objects.
- Analog Outputs: While discrete ON/OFF is common, many sensors offer analog outputs (0-10V, 4-20mA) proportional to the amount of reflected light received. This enables tasks like edge guiding, precise positioning, or detecting subtle changes in transparency or fill level.
- Specialized Emitters: Laser diodes offer small, intense spots for detecting very small objects or precise positioning. Fiber optic versions (using separate amplifiers) allow sensing in extremely tight spaces, high temperatures, or hazardous areas.
Why the Photoelectric Sensor Principle Reigns Supreme
The fundamental photoelectric sensor working principle – detecting changes in light – provides significant advantages over other sensing technologies like inductive or capacitive proximity sensors. Photoelectric sensors excel at detecting objects at greater distances, can sense virtually any material (opaque or transparent), and offer unparalleled versatility through their different operational modes. Their non-contact nature ensures no wear on the sensor or target, leading to long service life and low maintenance. Continuous innovation in light sources, receiver sensitivity, and signal processing ensures they remain a cornerstone of industrial automation.
From verifying a tiny component is present on a high-speed assembly line to ensuring a massive container is correctly positioned on a loading dock, photoelectric sensors translate the invisible interaction of light and object into the reliable, discrete signals that keep modern automation systems running smoothly and efficiently. Understanding *