diffuse reflective optical sensor
- time:2025-07-25 00:56:03
- Click:0
Diffuse Reflective Optical Sensors: The Workhorse of Non-Contact Object Detection
Ever wondered how machines “see” objects without touching them? How does a conveyor belt know a package has arrived, or a robot arm sense the presence of a component? Often, the invisible hero enabling this automation magic is the diffuse reflective optical sensor. This robust and versatile technology forms the backbone of countless sensing applications across diverse industries, providing reliable and cost-effective non-contact detection solutions. Understanding its principles, strengths, and limitations is key to leveraging its power effectively.
Understanding the Core Principle: Light Reflection Reimagined
Unlike its counterparts – retroreflective sensors (which rely on a reflector) or through-beam sensors (using separate transmitter and receiver units) – the diffuse reflective optical sensor integrates both the light emitter (usually an LED, infrared or visible light) and the photodetector (receiver) into a single housing unit. Its operation hinges entirely on detecting light diffusely reflected off the surface of a target object.
Here’s the step-by-step process:
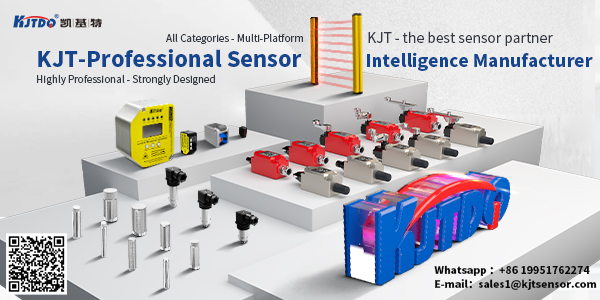
- Emission: The sensor’s integrated LED emitter sends out a beam of light, typically infrared (IR) for insensitivity to ambient visible light or red light for visible indication.
- Target Interaction: This emitted light beam strikes the surface of the target object within the sensor’s detection range.
- Diffuse Reflection: Crucially, the target surface scatters the incident light rays in many directions – this is the diffuse reflection. Unlike a mirror (specular reflection), most real-world objects (cardboard, plastic, metal with texture, liquids, biological tissue) diffusely reflect light.
- Detection: Some portion of this diffusely scattered light travels back towards the sensor’s housing.
- Reception and Processing: The integrated photodetector (like a phototransistor or photodiode) captures the returned light energy. The sensor’s internal circuitry then evaluates the intensity of this received light. If the received intensity exceeds a predefined threshold (indicating sufficient reflection from a nearby object), the sensor switches its output state (e.g., from OFF to ON, or vice versa).
- Output Signal: This state change generates a signal used by the control system – triggering an action like stopping a motor, counting an item, or changing a display.
Key Characteristics and Advantages
This fundamental operating principle grants diffuse reflective sensors several distinct advantages:
- Single-Unit Simplicity: The integrated emitter/receiver design makes installation significantly easier and less costly than through-beam sensors, which require precise alignment of two separate units. There’s no need for a separate reflector like with retroreflective sensors.
- Cost-Effectiveness: Their simple design makes them generally the most economical optical sensing solution.
- Compact Size: The single housing allows for very compact sensor designs, ideal for space-constrained applications.
- Non-Contact Operation: Like all optical sensors, they detect objects without physical touch, eliminating wear and tear on both the sensor and the object.
- Versatility: Capable of detecting a wide variety of materials, especially those with non-shiny, matte surfaces that provide good diffuse reflection (cardboard, paper, wood, most plastics, textured metals).
- Suitability for Close-Range Detection: Excelling at detecting objects positioned relatively close to the sensor face.
This versatility makes them the go-to choice for numerous applications.
Where Diffuse Reflective Sensors Shine: Common Applications
You’ll find these sensors operating reliably in countless scenarios:
- Object Presence/Absence Detection: Detecting bottles on a filling line, packages on a conveyor belt, sheets of paper in a printer, or components in assembly jigs. Is the part in place? Has the product passed the checkpoint?
- Counting: Tallying products on a line (e.g., bottles, boxes, pills in blister packs).
- Level Detection: Sensing the presence (or absence) of material within a bin or container (e.g., detecting low paper in a copier tray, monitoring fill levels in non-transparent containers).
- End-of-Travel/Position Verification: Confirming doors are closed, robotic arms have reached a home position, or slides have extended fully.
- Label Detection: Sensing the presence of a label on a product (relying on the difference in reflectivity between the label and the background or the gap between labels).
- Robotics & Automation: Proximity sensing for end effectors, part positioning feedback, and obstacle detection in collaborative environments (though often with shorter ranges).
- Vending Machines: Detecting dispensed products or coin presence.
- Security Systems: Tamper detection (e.g., breaking a light beam onto a diffusely reflective surface).
Navigating Limitations and Best Practices
Despite their widespread utility, diffuse reflective sensors have inherent limitations defined by their operating principle:
- Sensitivity to Surface Properties: This is the most critical factor. Performance heavily depends on the target’s color, texture, and material. Highly reflective or specular surfaces (like mirrors or polished chrome) tend to reflect light away from the sensor’s receiver, potentially causing false negatives or unreliable detection. Conversely, very dark or light-absorbing surfaces (black velvet, certain plastics) reflect very little light back, also making detection difficult.
- Limited Sensing Range: Compared to through-beam sensors, their effective range is significantly shorter, typically ranging from a few millimeters up to perhaps a meter or two, depending heavily on emitter power and target reflectivity. Detecting low-reflectivity targets drastically reduces the usable range.
- Ambient Light Sensitivity: While many modern sensors incorporate background suppression technology or modulated light to combat this, bright ambient light shining directly onto the receiver can potentially saturate it or cause false triggering.
- Environmental Factors: Contamination like dust, dirt, or oil on the sensor’s lens or the target surface can severely attenuate the light signal, reducing detection reliability. Harsh chemicals, extreme temperatures, or steam can also affect performance if the sensor isn’t rated for these conditions.
To achieve optimal and reliable performance:
- Prioritize Target Characterization: Carefully evaluate the target material’s color and surface finish. Test the specific sensor model with the actual target under real conditions if possible.
- Consider Background Suppression (BGS) Technology: Opt for sensors featuring Background Suppression. These advanced models use triangulation principles to focus detection only within a specific, short distance range in front of the lens, largely ignoring objects or surfaces beyond that point. This is invaluable when the target needs to be detected reliably against a potentially reflective background at a different distance. It greatly reduces false triggers.
- Factor in Range Requirements: Ensure the sensor’s specified operating range is sufficient for the application, considering the likely reflectivity of the target. Don’t rely on maximum range specs achieved with perfect targets.
- Mind the Environment: Choose sensors with appropriate Ingress Protection (IP) ratings for dusty or wet environments. Ensure they can withstand any chemical exposure or temperature extremes present.
- Keep Lenses Clean: Implement maintenance routines to keep the sensor’s window clean for consistent light transmission.
- Utilize Adjustability: Leverage potentiometers or teach-in functions to fine-tune the sensitivity threshold for reliable operation on the specific target surface.
Diffuse reflective optical sensors are a testament to elegant engineering simplicity solving complex problems. Their robust design, cost-effectiveness, and fundamental non-contact detection principle make them an indispensable tool for industrial automation and beyond. By thoroughly understanding their reliance on diffuse reflection, carefully evaluating target properties, and applying best practices like selecting sensors with background suppression, engineers and designers can harness this reliable technology to create smarter, more efficient systems. They may operate unseen, but their impact on automated processes is fundamental and undeniable.