reflective beam sensor
- time:2025-07-25 00:30:36
- Click:0
Reflective Beam Sensors: The Invisible Guardians of Object Detection
Have you ever wondered how a vending machine knows a can is present, or how an industrial robot avoids collisions, or even how some automatic soap dispensers sense your hand? Often, the silent hero behind these seemingly simple actions is the reflective beam sensor. These compact yet powerful devices are fundamental components in countless applications, offering a simple, reliable, and cost-effective solution for detecting objects and distance. Let’s delve into how they work, where they shine, and why they are so widely adopted.
Understanding the Core Principle: Light, Reflection, and Detection
At its heart, a reflective beam sensor operates on a remarkably straightforward principle, reminiscent of echolocation but using light instead of sound. It consists of just two core components housed together in a single unit:
- Emitter: This component, usually an infrared (IR) LED, laser diode, or sometimes a visible light LED, projects a beam of light outward.
- Receiver (Detector): Positioned right beside the emitter, this component (commonly a phototransistor or photodiode) is specifically tuned to be sensitive to the wavelength of light emitted.
The magic happens when an object enters the sensor’s detection zone:
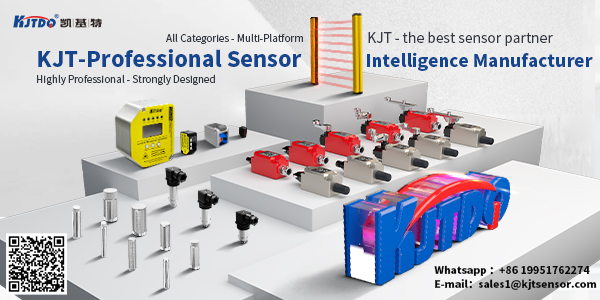
- The emitter constantly sends out its light beam.
- If no object is present within the sensor’s designed range and angle, the light beam travels away, and only a minimal amount of ambient light or stray reflection reaches the receiver. The receiver’s output signal remains low.
- When an object enters the detection zone, the emitted light beam strikes its surface.
- A portion of this light is reflected back towards the sensor unit.
- The receiver detects this increase in reflected light intensity.
- This change in detected light triggers a significant shift in the receiver’s output signal (e.g., switching from a low state to a high state, or vice versa, depending on the sensor’s logic). This signal change is the sensor’s way of saying, “Object detected!”.
Variations on a Theme: Key Types of Reflective Sensors
While the basic principle remains constant, several types cater to different needs:
- Standard Diffuse Reflective Sensors: These are the most common type. They use an IR LED and phototransistor. Detection relies on the diffuse reflection from the object’s surface. They are simple and cost-effective but have a relatively short range and performance can be influenced by the object’s color, texture, and reflectivity. Light-colored, matte objects reflect well; dark, shiny, or absorbent objects can be harder to detect consistently.
- Background Suppression (BGS) / Fixed Focus Sensors: These sensors use optical elements to focus the emitted beam at a specific, fixed distance. The receiver is only sensitive to reflections coming back from this precise focal point. This allows them to reliably detect objects within a very narrow window at the set distance, largely ignoring objects closer or farther, as well as highly reflective or dark backgrounds beyond the focal point. This makes them excellent for precise positioning tasks.
- Retro-reflective Sensors (Requires Reflector): While “reflective beam sensor” typically means diffuse reflective (bouncing light off the object itself), it’s worth noting the contrast with retro-reflective types. Retro-reflective sensors also have an emitter and receiver together, but they require a special reflector placed opposite the sensor. The beam travels to the reflector and back. The sensor detects an object when it interrupts this beam path. They offer much longer detection ranges than diffuse types but require mounting the reflector.
Where Reflective Beam Sensors Make a Difference: Ubiquitous Applications
The simplicity, compact size, and affordability of reflective beam sensors make them incredibly versatile. You’ll find them in:
- Industrial Automation: Object presence detection on conveyor belts or assembly lines, counting products, position verification of parts in machinery, end-of-travel detection for robotic arms (preventing collisions), fill level detection in bins or hoppers (using specific mounting angles).
- Consumer Electronics & Appliances: Paper jam detection in printers and copiers, detecting cassette tapes or CDs, position sensing in disk drives, automatic soap or sanitizer dispensers, automatic faucets, proximity sensing for touchless controls.
- Medical Equipment: Detecting slides/reagents in analyzers, patient or equipment positioning alerts, cover closure detection, fluid level sensing.
- Automotive: Detecting seat occupancy (for airbag control), sunroof or window pinch detection (safety feature), gear position sensing, parking assist sensors (often ultrasonic, but optical variants exist).
- Vending Machines & Kiosks: Identifying product presence in delivery chutes, detecting coins or bills passing through mechanisms.
- Security: Simple intrusion detection (breaking a beam), automatic door openers (sensing approach).
Why Choose a Reflective Beam Sensor? The Compelling Advantages
Several key benefits drive their widespread adoption:
- Non-Contact Operation: The sensor detects objects without physically touching them. This eliminates wear and tear on both the sensor and the object, making them ideal for delicate items or high-speed applications. The lack of physical contact translates directly to longevity and reliability.
- Compact Size & Simple Installation: Combining emitter and receiver into a single, small unit drastically simplifies mounting. There’s no need to precisely align separate components on opposite sides of a detection path (unlike through-beam sensors). This saves space and reduces installation complexity and time.
- Cost-Effectiveness: The integrated design and common components make diffuse reflective sensors one of the most economical sensing solutions available for object detection tasks.
- High-Speed Response: These sensors react extremely quickly to changes in light reflection, enabling detection in fast-moving production lines or machinery. Response times are typically measured in milliseconds, making them suitable for demanding industrial processes.
- Reliability (When Applied Correctly): With no moving parts, they are inherently robust. By choosing the right type (e.g., BGS for challenging backgrounds) and ensuring the target object provides sufficient reflection, they deliver highly dependable operation.
- Digital Output: Most modern reflective sensors provide a clean, easy-to-interface digital output (e.g., PNP/NPN transistor switch, push-pull), simplifying integration with PLCs, microcontrollers, and other control systems. This provides immediate, actionable real-time feedback.
Implementing Effectively: Key Considerations
To maximize the performance and reliability of a reflective beam sensor, consider these factors:
- Target Characteristics: Will