photoelectric liquid level sensor
- time:2025-07-25 00:25:29
- Click:0
Photoelectric Liquid Level Sensors: Precision Non-Contact Detection for Demanding Applications
Keeping track of liquid levels is fundamental across countless industries, from manufacturing chemicals and pharmaceuticals to managing water resources and processing food. Accuracy, reliability, and minimal maintenance are paramount. Enter the photoelectric liquid level sensor – a sophisticated solution leveraging the fundamental properties of light to deliver exceptional performance where traditional methods fall short. This technology offers a distinct advantage: detecting liquid presence without ever touching it.
How Does a Photoelectric Liquid Level Sensor Work? The Core Principle
At its heart, a photoelectric liquid level sensor operates on a beautifully simple yet powerful principle: the difference in how light behaves when passing through air versus liquid, specifically the phenomenon of refraction.
Imagine a sensor housing containing two key components:
- An Infrared (IR) Light Emitting Diode (LED): This emits an invisible beam of infrared light.
- A Phototransistor or Photodiode Receiver: Positioned to detect that IR beam.
The critical element is the design of the sensor’s tip, typically made from a highly transparent, chemically resistant material like sapphire or specialized glass. This prism-shaped tip is strategically positioned where liquid detection is needed.
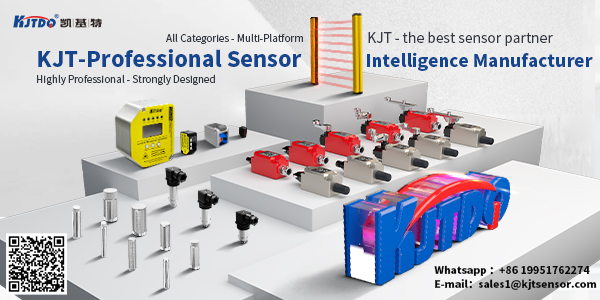
Here’s the magic:
- In Air: When the sensor tip is surrounded by air, the infrared light emitted from the LED undergoes total internal reflection within the prism. Because the critical angle for the air-glass interface is relatively small, the light beam bounces internally and is efficiently directed towards the phototransistor, which registers a “high” or “ON” signal.
- In Liquid: When the liquid level rises and submerges the sensor tip, everything changes. Liquids generally have a higher refractive index than air. This changes the critical angle at the prism/liquid interface. Instead of reflecting internally, a significant portion of the infrared light refracts out into the liquid. Consequently, much less light reaches the phototransistor. This significant drop in received light intensity triggers a “low” or “OFF” signal.
This clear, binary state change (light detected = no liquid / light not detected = liquid present) provides an unambiguous indication of the liquid level at the precise point of the sensor tip. The beauty lies in its non-contact nature; only the tip interacts with the medium.
Where Photoelectric Liquid Level Sensors Excel: Key Applications
The unique characteristics of photoelectric sensors make them the ideal choice for numerous challenging environments:
- Chemically Aggressive Liquids: Thanks to chemically inert sensing tips (sapphire, PTFE-clad glass), these sensors excel with acids, alkalis, solvents, fuels, and other corrosive substances that would quickly degrade mechanical floats or conductive probes. Material compatibility is a critical advantage.
- High-Purity Applications: In pharmaceutical manufacturing, semiconductor production, or food & beverage processing, contamination is unacceptable. The non-contact principle ensures the liquid remains untouched by sensing components, preserving purity.
- Viscous Media and Slurries: Sticky liquids, oils, syrups, or slurries can gum up moving parts or coat conductive sensors, causing failure. Photoelectric sensors, with no moving parts and a smooth sensing tip, resist fouling and maintain reliable operation.
- High-Pressure or Vacuum Systems: Rugged designs allow these sensors to function reliably under significant pressure or within vacuum chambers where mechanical seals might fail.
- Point Level Detection Tasks: Ideal for critical functions requiring precise on/off control:
- Overfill Prevention: Triggering an alarm or pump shut-off when a tank reaches maximum capacity.
- Dry Run Protection: Detecting low levels to prevent pumps from operating without liquid, avoiding catastrophic damage.
- Leak Detection: Identifying unexpected liquid presence in containment areas or sumps.
- Tank Empty/Full Confirmation: Providing definitive signals for process control sequences.
- Applications Demanding Fast Response: With no inertia from moving parts, the state change (liquid/no liquid) is virtually instantaneous, enabling rapid control actions.
Compelling Advantages Over Traditional Methods
Why choose a photoelectric sensor over float switches or conductive probes? The benefits are substantial:
- No Moving Parts: This is arguably the biggest advantage. Eliminating floats, arms, or reed switches translates to dramatically reduced mechanical wear and tear, significantly enhancing long-term reliability and sensor lifespan. Failure points are minimized.
- Non-Contact Sensing: The sensing element doesn’t immerse in the liquid (only the inert prism tip contacts it). This prevents contamination of the liquid and avoids issues like coating, scaling, or clogging that plague immersed sensors. Hygiene and purity are preserved.
- Exceptional Chemical Resistance: Utilizing materials like sapphire or specialized glass/plastics for the tip ensures compatibility with an extremely wide range of aggressive fluids, far exceeding the capabilities of most elastomers or metals used in other sensors.
- High Accuracy & Repeatability: Detection occurs precisely at the tip, offering consistent and reliable point-level switching without hysteresis issues common in floats.
- Low Maintenance: The combination of no moving parts and resistance to fouling/chemicals means these sensors require minimal attention after installation, lowering the total cost of ownership.
- Insensitivity to Liquid Properties: Unlike capacitive or conductive sensors, photoelectric sensors generally aren’t affected by the liquid’s conductivity, dielectric constant, or bubbles (as long as the tip itself is fully covered). They detect the interface based purely on refractive index change. Performance remains consistent across diverse liquids.
- Simple Installation & Integration: Typically installed via a threaded process connection (NPT, BSP, etc.) or flange, they offer straightforward mounting. Output is usually a clean digital signal (PNP/NPN transistor, relay) easily interfaced with PLCs, controllers, or alarms.
Important Considerations for Optimal Use
While powerful, ensuring success requires attention to a few factors:
- Tip Contamination: While resistant, heavy coating or opaque deposits can potentially block or scatter the light beam, interfering with detection. Selecting a sensor with a smooth tip suitable for the liquid and periodic inspection (or cleaning if feasible) mitigates this. Preventative maintenance matters.
- Turbulence & Bubbles: Excessive splashing, heavy foam, or persistent bubbles directly around the tip could cause intermittent switching. Mounting the sensor in a relatively calm area of the tank (e.g., using a stilling well) often solves this.
- Material Compatibility: While the tip is highly resistant, ensure the sensor housing material (stainless steel, plastic) and seals (e.g., FKM/Viton, EPDM, FFKM) are compatible with the process environment (liquid, vapor, temperature, pressure).
- Mounting Orientation: Some designs may have optimal mounting angles. Consulting the manufacturer’s datasheet is essential.
- Transparent Containers: When sensing through a container wall, ensure the container material is transparent to the sensor’s specific IR wavelength and that external light interference is minimized (often addressed by sensor design).
Conclusion: A Smart Choice for Reliable Level Control
The photoelectric liquid level sensor stands as a testament to elegant engineering solving real-world problems. By harnessing the reliable principle of light refraction and utilizing robust, non-contact construction, it delivers unparalleled performance in environments where other technologies struggle. Its strengths – exceptional reliability, chemical resistance, non-contaminating operation, and minimal maintenance needs – make it an indispensable tool for ensuring process safety, efficiency, and product quality across a vast spectrum of demanding industrial and commercial applications. When precision point-level detection of even the most challenging liquids is critical, the photoelectric sensor offers a fundamentally superior solution.