proximity speed sensor
- time:2025-07-12 01:24:31
- Click:0
Proximity Speed Sensors: The Non-Contact Powerhouse Driving Modern Automation
Imagine a critical conveyor belt in a bustling factory suddenly grinding to a halt. Production stops, costs mount. The culprit? Often, it’s unseen wear or failure in a component monitoring its speed. Traditional contact-based methods, like mechanical tachometers dragging against a shaft, are prone to slippage, wear, and inaccuracy, especially in harsh environments. This is where the proximity speed sensor emerges as the unsung hero – a sophisticated, non-contact solution transforming how we measure rotational and linear velocity with remarkable precision and unparalleled reliability.
Fundamentally, a proximity speed sensor detects the presence, absence, or passage of a target object without physical contact, and crucially, translates the frequency of these detections into a speed measurement. It’s a marriage of proximity sensing principles and frequency-to-speed conversion. Unlike traditional encoders that require direct coupling to a shaft, proximity sensors operate at a distance, making them ideal for applications where mounting space is tight, contamination is high, or physical wear is unacceptable.
How Do They Work Their Magic?
The core technology hinges on detecting changes in a physical field. The two predominant types are:
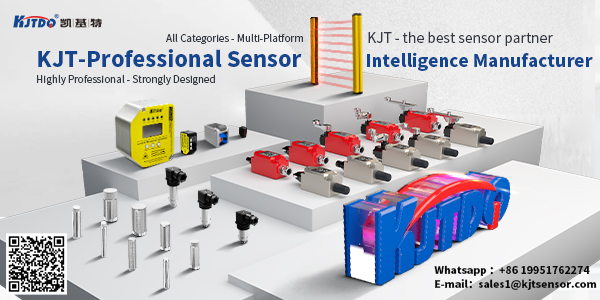
- Inductive Proximity Speed Sensors: These generate a high-frequency oscillating electromagnetic field emanating from the sensing face. When a metallic target (like a gear tooth, keyway, bolt head, or specially designed trigger wheel) enters this field, it induces small circulating electrical currents called eddy currents within the metal. These eddy currents draw energy from the sensor’s oscillator circuit. This energy loss translates into a measurable change in the oscillation amplitude or frequency. By counting the number of times this detection event happens per second as the target features rotate or move past the sensor, the sensor (or associated controller) can precisely calculate the target’s speed.
- Hall Effect Proximity Speed Sensors: These utilize the Hall effect principle. They contain a semiconductor element that generates a voltage (the Hall voltage) perpendicular to the direction of an applied electric current when exposed to a magnetic field. A magnet is either embedded within the sensor or mounted on the moving target (like a ferrous gear tooth passing near the magnet). As the magnetic field strength fluctuates due to the target movement (e.g., a tooth passing close creates a peak, a gap creates a trough), the Hall voltage changes proportionally. The frequency of these voltage pulses directly corresponds to the rotational speed of the target.
Key Advantages: Why Choose Proximity Speed Sensors?
The shift towards proximity-based speed sensing is driven by compelling benefits:
- Non-Contact Operation: This is the cornerstone advantage. Eliminating physical wear extends sensor life dramatically and prevents damage to the target shaft or component, leading to significant reduced maintenance costs and downtime.
- High Reliability & Durability: Sealed designs protect the sensitive electronics from dust, dirt, moisture, oil, and even chemical splashes (commonly rated IP67 or higher). They thrive in environments where optical sensors would fog or mechanical sensors would jam and wear.
- Immunity to Surface Conditions: Proximity sensors are largely unaffected by surface oil, grease, or minor debris (unlike optical sensors). Inductive types detect the metal itself through these contaminants, and Hall effect sensors respond to magnetic fields, which penetrate most non-ferrous grime.
- Wide Operating Speed Range: Modern proximity speed sensors offer impressive dynamic range, capable of accurately measuring speeds from very slow creeping movements (inches per minute) to extremely high RPMs encountered in turbines or high-speed motors.
- Robustness in Harsh Environments: Engineered to withstand extreme temperatures, high vibration, and shock, they are ideal for demanding sectors like heavy industry, automotive testing, and offshore applications.
- Simple Installation & Retrofit: Mounting typically involves securing the sensor at the correct gap distance (air gap) from the target. No complex mechanical coupling, lubrication, or alignment of drive shafts is required, simplifying installation and making them perfect for retrofitting onto existing machinery.
Where Are They Making a Difference?
Proximity speed sensors are ubiquitous across industries, silently ensuring efficiency and safety:
- Industrial Automation & Manufacturing: Monitoring conveyor belt speeds, motor and pump shaft RPMs, gearbox output speeds, spindle speeds in CNC machines, and detecting overspeed/underspeed conditions on production lines.
- Automotive: Measuring wheel speed for Anti-lock Braking Systems (ABS), monitoring crankshaft and camshaft position/speed (engine timing), transmission shaft speeds, and testing engine RPM during development and manufacturing.
- Aerospace: Tracking turbine engine speeds (N1, N2), monitoring APU (Auxiliary Power Unit) performance, and measuring landing gear wheel speeds.
- Material Handling: Controlling the speed of rollers in printing presses, paper machines, and packaging equipment; monitoring bucket elevator chain speeds.
- Energy: Measuring wind turbine rotor speeds, monitoring pump speeds in power plants and water/wastewater treatment facilities, and tracking generator output shaft RPM.
- Rail & Transportation: Monitoring axle speeds for traction control and safety systems, measuring ground speed.
Essential Considerations for Optimal Performance
While powerful, achieving reliable speed measurement requires attention to detail:
- Target Material & Size: Inductive sensors require ferrous (iron-based) metal targets. Non-ferrous metals like aluminum or copper require specific sensor designs or Hall effect sensors (which usually need a magnetic target or a ferrous target with a separate magnet). The target feature size and shape must be suitable to reliably trigger the sensor.
- Air Gap: Maintaining the correct distance between the sensor face and the target is critical for consistent signal strength and detection. This is specified by the manufacturer.
- Target Geometry: The pattern and spacing of target features (teeth, gaps, holes, lugs) directly define the resolution and accuracy of the speed calculation. Consistent feature spacing is key.
- Sensor Output & Signal Conditioning: Sensors typically provide a digital pulse (PNP/NPN), analog voltage (0-10V), or analog current (4-20mA) signal proportional to speed. Choosing the right output type compatible with the receiving controller (PLC, drive, display unit) is essential. Signal conditioning circuitry may sometimes be needed to clean noisy signals.
- Environmental Factors: While robust, extreme temperatures exceeding the sensor’s rating, or exceptionally strong external magnetic/electrical fields, can interfere with performance.
The Silent Workhorse of Precision Motion Control
Proximity speed sensors represent a leap forward in motion sensing technology. Their ability to deliver accurate, reliable speed sensing without physical contact, coupled with exceptional durability in challenging conditions, makes them indispensable across countless modern applications. From ensuring the smooth flow of assembly lines to guaranteeing the safe operation of vehicles and critical machinery, these sophisticated devices operate silently in the background. Understanding their operational principles – the interplay of electromagnetic fields or the Hall effect – and their inherent advantages over contact methods empowers engineers and maintenance professionals to select and deploy them effectively. As automation demands ever-greater precision and uptime, the role of the versatile and robust proximity speed sensor continues to expand, solidifying its position as a cornerstone of efficient and safe industrial operations.