ir distance sensors
- time:2025-07-12 01:17:29
- Click:0
Unlocking Precision: How IR Distance Sensors Revolutionize Modern Technology
Imagine a technology that works like a bat’s echolocation, but with invisible light, capable of measuring distances without physical contact, operating silently in the background of countless devices. This is the essence of Infrared (IR) Distance Sensors. These compact yet powerful components are fundamental to enabling machines to perceive their surroundings, driving innovation across a vast spectrum of applications. This article dives deep into the world of IR sensing technology, exploring its principles, diverse uses, advantages, and key selection considerations.
Seeing with Invisible Light: The Core Principle
At its heart, an IR distance sensor operates by leveraging the properties of infrared light – electromagnetic radiation with wavelengths longer than visible light but shorter than microwaves. The fundamental operation involves:
- Emission: An integrated infrared LED (Light Emitting Diode) emits a beam of IR light, typically modulated (pulsed) at a specific frequency to improve noise immunity and range detection.
- Reflection: This IR beam travels outward and strikes an object within its field of view.
- Detection: A portion of the emitted light reflects off the object and travels back towards the sensor.
- Measurement: A sensitive photodetector (like a photodiode, phototransistor, or a specialized Position Sensitive Device - PSD) captures the reflected light. The sensor’s internal electronics then calculate the distance based on how the returning light is received. The two primary measurement techniques are:
- Triangulation Method: Commonly used in shorter-range sensors (< 30cm). The emitted IR light hits the target and reflects at an angle. The reflected beam hits the PSD at a position proportional to the distance. Measuring this position shift allows precise distance calculation. Known for high accuracy at close range.
- Time-of-Flight (ToF): Suitable for longer ranges (up to several meters). The sensor precisely measures the small time difference (Δt) between the emission of the IR pulse and the detection of its reflection. Since the speed of light (c) is constant, distance (d) is calculated directly: *d = (c * Δt) / 2*. Offers faster response times and is less affected by object color and surface characteristics.
Beyond Simple Distance: Photoelectric Sensors vs. IR Distance Sensors
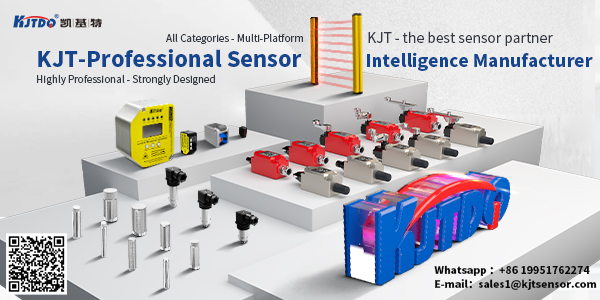
It’s important to distinguish IR distance sensors from simpler IR photoelectric sensors (like break-beam or reflective sensors). While both use IR light:
- Photoelectric Sensors: Primarily provide a binary output (object present/not present) or sometimes a rough analog signal indicating intensity. They detect presence but typically cannot provide an exact distance measurement. Examples include garage door safety beams or conveyor belt object detectors.
- IR Distance Sensors: Explicitly designed to provide a continuous output signal (analog voltage, PWM, digital I2C/UART) proportional to the measured distance. They offer precise quantitative data about how far away an object is.
Where the Invisible Works: Ubiquitous Applications
The ability to provide non-contact distance measurement reliably and affordably makes IR distance sensors indispensable in numerous fields:
- Robotics & Automation: Obstacle detection and avoidance is crucial for mobile robots (AGVs, drones, vacuum cleaners). They enable precise positioning of robotic arms near workpieces and bin picking. Proximity sensing ensures safety around machinery.
- Consumer Electronics: Smartphone screens use them for proximity detection during calls. Gesture recognition features in TVs and game consoles often rely on IR sensing. Automatic soap dispensers and faucets utilize them for touchless activation.
- Automotive Industry: Found in parking assist systems to detect curbs and obstacles. Enable blind-spot monitoring and automatic braking systems’ initial short-range detection layers. Used inside cabins for driver alertness monitoring or gesture controls.
- Industrial Control & Manufacturing: Level sensing in tanks (non-hazardous materials), object counting on conveyors, web sag detection, and position feedback on moving parts rely on these sensors.
- Appliance & HVAC: Used in dishwashers and washing machines for water level control. Smart thermostats may employ them for occupancy detection to optimize heating/cooling.
- Interactive Displays: Enable touchless interaction with kiosks and museum exhibits.
Why Choose IR? Key Advantages
- Non-Contact Measurement: Eliminates mechanical wear and tear and allows measurement of fragile or moving objects.
- Compact Size & Low Cost: Small form factors and relatively inexpensive compared to technologies like ultrasonic or laser rangefinders (for shorter ranges).
- Fast Response Time: Particularly ToF variants offer rapid measurement updates, crucial for dynamic applications like robotics.
- Low Power Consumption: Ideal for battery-operated devices like smartphones and portable gadgets.
- Modest Range Adequacy: Well-suited for applications requiring detection within centimeters to several meters.
Navigating the Choices: Key Selection Factors
Choosing the right IR distance sensor requires careful consideration of your specific application needs:
- Measurement Range & Accuracy: What is the minimum and maximum distance you need to measure? What level of precision is required (e.g., ±1mm vs ±10mm)? Triangulation excels at close-range accuracy; ToF offers better longer-range performance.
- Target Characteristics: How does the object’s surface affect performance? Highly reflective surfaces (mirrors, metal) can cause inaccurate readings due to specular reflection. Dark, matte, or absorbent surfaces significantly weaken the return signal, potentially reducing range. Transparent objects (glass, plastic) might be difficult or impossible for standard IR sensors to detect reliably.
- Environmental Factors: Ambient IR light (sunlight, incandescent bulbs) is a major challenge. Look for modulated IR sensors with filters and robust signal processing. Dust, fog, or steam can scatter IR light, impacting range and accuracy. Temperature extremes can affect LED output and detector sensitivity.
- Output Interface & Signal Processing: Do you need a simple analog output voltage proportional to distance? A PWM signal? Or a digital output (I2C, UART) offering calibrated distance values and potentially additional features? Consider the ease of interfacing with your microcontroller or PLC.
- Field of View (FoV): The beam angle determines the width of the area the sensor can detect. A narrow FoV provides precise point measurement, while a wide FoV is better for presence detection over an area. Alignment is easier with a narrower FoV.
- Response Time & Update Rate: How quickly does the application require updated distance readings? Critical for high-speed robotics or automation.
The Future is Sensing
IR distance sensors are a cornerstone of modern sensing technology, offering a compelling blend of simplicity, affordability, and capability. Their role in enabling machines to interact intelligently with the physical world is undeniable. From the smartphone in your pocket to the automated factory floor and the autonomous vehicles of tomorrow, the invisible beams of IR light are constantly at work, measuring distances and driving innovation. Understanding their principles, strengths, limitations, and selection criteria is key to unlocking their potential in your next project. As sensing technologies continue to evolve, infrared proximity detection remains a vital tool in the engineer’s toolkit, quietly shaping a more responsive and automated future.