dc proximity sensor
- time:2025-07-12 00:14:10
- Click:0
DC Proximity Sensors: Powering Industrial Automation Effortlessly
Imagine a robotic arm glides toward a component on an assembly line. It doesn’t crash; instead, it halts precisely millimeters away, picks up the part with perfect dexterity, and moves on. This silent ballet of machinery, critical for efficiency and safety, hinges on an unseen hero: the DC proximity sensor. Far more than just a switch, these compact electronic sentinels silently monitor their surroundings, detecting objects without physical contact. Their ability to thrive on direct current (DC) power makes them indispensable workhorses in the demanding world of industrial automation and countless other applications. Understanding what they are and why their DC nature is crucial reveals the foundation of reliable, contactless sensing.
What Exactly Are DC Proximity Sensors?
At their core, proximity sensors are electronic devices designed to detect the presence or absence of an object within a specific range – their sensing distance – without needing to touch it. They achieve this feat through various physical principles. The most common types are:
- Inductive Proximity Sensors: These detect metallic objects (primarily ferrous metals like iron and steel, but also non-ferrous like aluminum or copper at reduced range). They generate an oscillating electromagnetic field. When a metal target enters this field, it induces eddy currents within the metal. This disturbance causes a measurable change in the sensor’s internal oscillation or coil inductance, triggering its output switch.
- Capacitive Proximity Sensors: These detect a much wider range of materials, including metals, plastics, liquids, powders, and wood. They function similarly to a capacitor. The sensor face acts as one plate, and the target object (or sometimes ground) acts as the other plate. As the target approaches, the capacitance between them changes. The sensor circuitry detects this change and activates the output.
- Optical Proximity Sensors: These use light (usually infrared LED) and a receiver (phototransistor or photodiode). They detect objects by either the interruption of a light beam (through-beam) or the reflection of light off the target (retro-reflective or diffuse reflective). While also powered by DC, their operating principle is distinctly different.
The Critical Advantages of DC Power
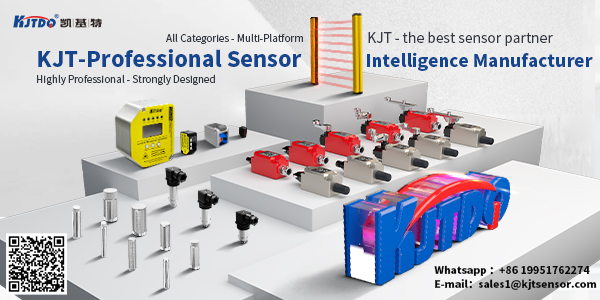
While proximity sensors exist in AC versions, DC proximity sensors hold distinct advantages that make them the preferred choice in modern electronics and automation:
- Simplified Wiring & Integration: DC sensors typically require only two wires for power and signal output. This dramatically simplifies installation, reducing wiring complexity, potential points of failure, and installation time compared to 3-wire AC sensors. Their output is usually a simple DC voltage signal (like PNP or NPN open-collector transistor outputs), making them inherently compatible with the DC-powered logic levels of PLCs (Programmable Logic Controllers), microcontrollers, and modern control systems.
- Superior Switching Speed: DC sensors boast significantly faster response times compared to their AC counterparts. They can detect objects and switch their output state much quicker (often in microseconds or milliseconds). This high-speed capability is essential for applications involving rapidly moving objects on high-speed production lines or in precise positioning tasks.
- Lower Power Consumption: DC proximity sensors are generally more energy-efficient. This is particularly beneficial in battery-operated systems, large installations with many sensors, or applications where minimizing heat generation is crucial.
- Freedom from AC Hum: AC-powered sensors can sometimes introduce electrical noise (“hum”) into sensitive control circuits. DC sensors operate silently, eliminating this source of potential interference and ensuring cleaner signal transmission to control units.
- Output Flexibility: DC sensors offer versatile output configurations (PNP sourcing, NPN sinking, normally open, normally closed) to easily interface with different types of control inputs.
- Wider Operating Voltage Range: Many DC proximity sensors operate over a broad DC voltage range (e.g., 10-30V DC), providing tolerance against voltage fluctuations commonly found in industrial environments.
Unveiling the Core Mechanism: How They Detect
While the specific physics differ between inductive, capacitive, and optical types, the fundamental operating principle of a DC proximity sensor remains constant:
- Field Generation: Internally, the sensor generates a specific field based on its type (electromagnetic field for inductive, electrostatic field for capacitive, light beam for optical). This field extends outward from the sensor face to its rated sensing distance.
- Target Interaction: When a suitable target enters the effective range of this field, an interaction occurs:
- Inductive: Eddy currents form in the metal target, altering the sensor’s electromagnetic field.
- Capacitive: The effective capacitance between the sensor face and the target changes.
- Optical: Light is interrupted (blocked) or reflected back to the receiver.
- Internal Detection Circuit: Sophisticated internal electronics constantly monitor the state of the generated field or light reception. The microprocessor detects the change caused by the target presence.
- Output Signal Change: Upon detecting the qualifying change, the sensor’s solid-state output switch (e.g., transistor) changes state. This could mean switching on (connecting the output to supply voltage) or switching off (disconnecting the output), depending on its configuration (NO/NC). This state change is the clear, debounced DC signal sent to the control system.
The Pervasive Impact: Where DC Proximity Sensors Excel
Their reliability, speed, and versatility make DC proximity sensors ubiquitous across industries:
- Industrial Automation: The undisputed king of applications. Used for position sensing (end-of-stroke on cylinders, part presence on conveyors), object counting, machine guarding (detecting unsafe entry), level detection for liquids/powders in tanks (capacitive), and rotational speed monitoring.
- Automotive Manufacturing: Critical for assembly line robotics (positioning, welding, painting), part verification, conveyor control, and ensuring precise component placement.
- Packaging Machinery: Detecting product presence for filling, labeling, capping, and carton sealing. Verifying bottle caps or tamper seals are present.
- Material Handling: Monitoring pallet position, controlling conveyor belt starts/stops based on object presence, detecting jams.
- Building Automation: Automatic door operation (detecting approaching people), elevator position sensing, lighting control (presence detection), fluid level control in HVAC systems.
- Robotics: Providing essential feedback for navigation (obstacle avoidance), end-effector positioning, and object detection for picking/placing tasks.
- Consumer Electronics: Found in smartphones (screen on/off during calls), tablets, appliances (detecting door closure, water levels), and security systems.
Choosing the Right Sentinel: Key Selection Factors
Selecting the optimal DC proximity sensor requires careful consideration:
- Detection Principle: What material is the target? Metal? Choose Inductive. Plastic, liquid, wood? Capacitive is better. Any solid object via light interruption/reflection? Optical.
- Sensing Distance: How far away does the target need to be detected? Choose a sensor with a rated operating distance slightly larger than your required gap to account for tolerances and installation variations. Respect the specified mounting conditions (flush or non-flush for inductive) which affect range.
- Output Configuration: Does your control system require P