limit switch proximity sensor
- time:2025-07-11 03:31:08
- Click:0
Limit Switch Proximity Sensor: Mastering Position Detection in Automation
That unexpected clunk. The shuddering halt of a production line. A valuable component damaged because a machine traveled too far. In the high-stakes world of industrial automation, precise position detection isn’t just convenient; it’s essential for safety, efficiency, and product quality. This is where understanding the distinct roles and powerful synergy of limit switches and proximity sensors becomes critical. While the term “limit switch proximity sensor” often reflects a common search combining these two technologies, they are distinct solutions serving overlapping, yet different purposes in detecting the presence or position of objects. Mastering their application is key to robust system design.
What’s the Core Difference? Physical Contact vs. Invisible Fields
The fundamental distinction lies in how these sensors interact with the target object:
- The Classic Workhorse: Mechanical Limit Switches
- Operational Principle: These are electromechanical devices. They feature a physical actuator (lever, roller, plunger). When an object makes physical contact with this actuator, it mechanically triggers an internal set of electrical contacts (NO/NC) to change state.
- Key Characteristics:
- Requires Direct Contact: The target must touch the actuator.
- Robust & Simple: Generally durable, able to handle harsh environments (dust, moisture with proper ratings), and relatively inexpensive. Their operation is easily visualized.
- Tactile Feedback: Provides a definite physical confirmation of contact.
- Potential for Wear: Moving parts (actuator, internal springs/contacts) can wear out over time, especially under high-frequency cycling or excessive force.
- Mounting Flexibility: Often designed with adjustable mounting options or different actuator styles (e.g., roller levers for cams, whisker types for light touch).
- The Silent Sentinel: Proximity Sensors (Inductive/Capacitive)
- Operational Principle: These are solid-state electronic devices. They generate an electromagnetic field (inductive for metals) or an electrostatic field (capacitive for various materials, including non-metals and liquids). When a target object enters this field, it causes a detectable change (eddy currents for inductive, change in capacitance for capacitive), triggering the sensor’s electronic switch without any physical contact.
- Key Characteristics:
- Zero-Contact Operation: The defining feature. Detection happens through an invisible field.
- High Speed & Long Life: With no moving parts to wear out, proximity sensors boast exceptionally long operational lifespans and very fast response times, ideal for high-speed automation.
- Suitable for Challenging Objects: Can detect fragile, awkwardly shaped, or vibrating objects without disturbing them.
- Environmental Resilience: Sealed housings (IP67, IP69K common) make them excellent for dirty, wet, or washdown environments where physical switches might jam.
- Sensing Range: Defined by the sensor’s specifications; consistent detection occurs within this nominal range but fails outside it.
Why Combine Their Strengths? The “Limit Switch Proximity Sensor” Synergy
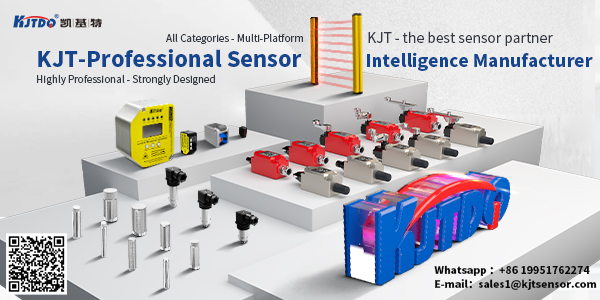
While distinct, limit switches and proximity sensors are often deployed together within automated systems, complementing each other perfectly:
- Safety Critical Limits: Robust mechanical limit switches are frequently chosen as final, fail-safe position stops. Their physical nature provides a highly reliable last line of defense to prevent catastrophic over-travel of machinery, even if the primary control system fails. A proximity sensor might serve as the primary “home” or “end-of-stroke” signal, but a limit switch acts as the ultimate backup.
- Primary Positioning with Endurance: Proximity sensors excel as the primary workhorse for routine position verification – detecting the end of a cylinder stroke, confirming a part is in place for machining, or signaling pallet presence. Their non-contact nature and long lifespan make them ideal for high-cycle applications where a mechanical switch would wear prematurely.
- Versatility in Object Detection: Need to detect a non-metallic bottle cap on a conveyor? A capacitive proximity sensor handles it easily where an inductive type or a standard limit switch would fail. Need absolute certainty a heavy metal gate is closed? A heavy-duty limit switch provides unambiguous physical confirmation.
- Speed Demands: For extremely high-speed processes (e.g., packaging lines), the near-instantaneous response of a proximity sensor is often essential, far exceeding the mechanical movement time of a limit switch actuator.
Key Applications Where They Shine
The choice between, or combination of, limit switches and proximity sensors depends heavily on the application:
- Machine Tooling: Limit switches for hard over-travel limits on axes; proximity sensors for tool changer position, spindle orientation, or chuck clamping confirmation.
- Material Handling: Proximity sensors for pallet detection at stations; limit switches as physical stops for lift gates or conveyor diverter arms.
- Packaging Machinery: Capacitive proximity sensors detecting plastic bottles or cardboard boxes; limit switches confirming case sealer gates are closed.
- Robotics: Proximity sensors used extensively for end-of-arm tooling presence detection and path sensing; limit switches often define critical joint rotation limits.
- Automotive Assembly: Inductive proximity sensors detecting metal components on fixtures; heavy-duty limit switches confirming door or hood closure force in test stations.
- Food & Beverage: Stainless steel capacitive sensors detecting liquid levels or plastic containers; washdown-rated limit switches on valves or hatches.
Choosing the Right Sensor for the Job: Key Considerations
Selecting between a limit switch or proximity sensor (or both) requires evaluating several factors:
- Target Object: Material (metal, plastic, liquid?), size, shape, required sensing distance? Can it withstand contact?
- Environment: Dust, moisture, temperature extremes, chemicals, vibration, washdown requirements? Proximity sensors often have an edge in harsh environments.
- Required Function: Simple presence/absence? Exact position? Over-travel protection? Speed of detection? Force verification (requires contact)?
- Cycle Life & Maintenance: High-frequency operation heavily favors non-contact proximity sensors for longevity. Lower speed or critical safety points may suit robust limit switches.
- Mounting Constraints: Available space? Physical access for actuator movement? Proximity sensors often offer more compact, flexible mounting options.
- Cost: While basic limit switches can be cheaper upfront, consider the total cost of ownership. Proximity sensors may offer lower lifetime costs in high-cycle applications due to zero maintenance.
Conclusion: Precision Through Understanding
The phrase “limit switch proximity sensor” underscores a fundamental truth in automation: effective position and object detection rarely relies on a single solution. Mechanical limit switches deliver unmatched physical reliability and tactile certainty, serving as vital safeties and confirmations where failure is not an option. Proximity sensors, leveraging non-contact technology, offer unparalleled speed, endurance, and versatility for the relentless demands of high-speed, high-cycle manufacturing. By understanding their distinct principles, strengths, limitations, and synergistic potential, engineers and technicians can design and maintain systems that operate with the precision, efficiency, and safety essential in today’s competitive industrial landscape. The right sensor in the right place makes all the difference between smooth operation and costly downtime.