induction sensor price
- time:2025-07-11 02:27:45
- Click:0
Demystifying Induction Sensor Pricing: What Really Drives the Cost?
Induction sensors, the silent workhorses of modern automation, detect the presence of metallic objects without physical contact. From ensuring precise positioning on assembly lines to safeguarding machinery, their reliability is paramount. Yet, when it comes time to procure them, the induction sensor price range can be surprisingly wide, leaving many buyers perplexed. Understanding the key factors that influence this cost is crucial for making informed purchasing decisions that balance budget and performance requirements.
Beyond the Basic Unit: Unpacking the Cost Variables
The sticker price of an induction sensor isn’t arbitrary. It’s a reflection of the engineering, materials, and capabilities packed into that compact housing. Here’s a breakdown of the primary drivers:
Sensing Range & Size: This is fundamental. Generally, sensors with longer sensing ranges require more sophisticated coil designs and electronics to generate and detect the necessary electromagnetic field reliably at a distance. Larger physical size often correlates with increased range and also uses more material. Unsurprisingly, a sensor with a 20mm range will typically cost more than one with a 4mm range.
Material & Build Quality: Durability is king in industrial settings. Sensors constructed from stainless steel (especially V4A/316L) offer superior corrosion resistance, chemical resilience, and mechanical strength compared to nickel-plated brass or plastic bodies. This robustness comes at a premium. The choice of housing material directly impacts longevity in harsh environments and thus influences the price significantly.
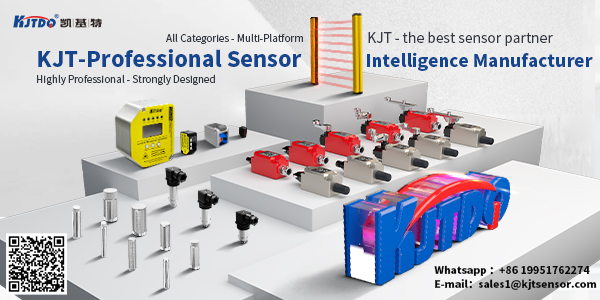
Output Configuration: How does the sensor communicate its detection state?
- Standard 2-Wire DC (NPN or PNP): The most common and generally the most economical option.
- 3-Wire DC (NPN or PNP): Often preferred for better switch-off characteristics and simpler wiring, may carry a slight premium over 2-wire.
- Analog Output (e.g., 0-10V, 4-20mA): Used for distance or position measurement, requiring more complex internal circuitry, thus increasing the cost substantially compared to simple on/off switches.
- NO/NC Configurability: Sensors that allow users to switch between Normally Open and Normally Closed operation without physical modification add flexibility but also cost.
- Special Outputs: IO-Link, AS-Interface, or other industrial communication protocols integrated into the sensor add significant functionality (diagnostics, parameter setting) and complexity, resulting in a higher price point but offering long-term value through smart connectivity.
Environmental Protection (IP Rating): Induction sensors often face dust, moisture, oils, and coolants. Higher IP ratings (e.g., IP67, IP68, IP69K) guarantee superior sealing and protection. Achieving these ratings requires meticulous design, high-quality seals, and rigorous testing, which translates into a higher induction sensor price. For washdown environments or extreme conditions, this is non-negotiable.
Performance Specifications: Precision matters.
- Switching Frequency: Sensors capable of detecting objects at very high speeds (e.g., >1kHz vs. standard 25Hz) demand faster response electronics.
- Hysteresis: A smaller hysteresis band provides more precise switching points but requires tighter manufacturing tolerances.
- Temperature Range: Sensors rated for extreme temperatures (e.g., -40°C to +100°C+) need specialized components and materials.
- EMC Immunity/Robustness: Superior resistance to electromagnetic interference prevents false switching in electrically noisy environments, requiring better shielding and filtering, adding to cost.
- Special Features & Certifications:
- Extended Temperature Ranges: As mentioned, operation far beyond standard industrial temps adds cost.
- Enhanced EMC Performance: Meeting stringent standards (like those for automotive or heavy machinery) increases R&D and component costs.
- Extended Operating Voltage Ranges: Flexibility across wide voltage inputs requires more robust power regulation.
- Flush Mount Capability (Non-Flush): While flush-mount sensors are common, non-flush variants allow embedding into metal and detecting recessed targets but require specific coil designs.
- Housing Styles: Unique form factors (e.g., cubical, miniature cylinders, block styles) for specific mounting needs may be priced differently.
- Certifications: ATEX/IECEx for hazardous areas, food-grade approvals (e.g., FDA, EC1935/2004), or specific automotive certifications necessitate rigorous testing and documentation, significantly impacting the final induction sensor price.
Brand Reputation & Support: Established global brands often command higher prices due to extensive R&D investment, proven reliability, comprehensive global warranties, and readily available technical support. While quality generic or regional brands offer cost-effective alternatives, the value proposition of premium brands includes reduced downtime risk and supply chain security.
Quantity & Supplier: Like most industrial components, volume purchasing usually unlocks significant discounts. Furthermore, buying directly from manufacturers or reputable distributors specializing in automation often yields better pricing and support than general electronics retailers. The specific sales channel and your negotiated terms are key factors.
Smart Spending: Navigating the Induction Sensor Marketplace
Understanding these drivers empowers smarter purchasing:
- Don’t Over-Specify: Carefully define your exact requirements. Do you truly need the longest range, the highest IP rating, or analog output? Purchasing a sensor with capabilities far beyond your application’s needs is an unnecessary expense. Choosing the right specification for the job is the first step towards cost efficiency.
- Consider Total Cost of Ownership (TCO): While the upfront induction sensor price is important, factor in longevity and reliability. A slightly cheaper sensor that fails prematurely or causes machine downtime can be far more expensive in the long run than a robust, reliable unit. The cost of downtime in industrial settings can dwarf the sensor’s price tag.
- Evaluate Generic vs. Premium Brands: For standard applications in non-critical environments, a quality generic sensor can offer excellent value. For critical processes, harsh conditions, or where long-term reliability is paramount, the investment in a premium brand may be justified. Research reliability data and reviews if available.
- Leverage Volume and Relationships: Consolidate requirements and negotiate based on volume or frame agreements with distributors/manufacturers. Building strong relationships with suppliers can lead to better pricing and priority support.
- Future-Proofing (Minimally): If anticipating future needs (e.g., potential IO-Link integration), buying sensors that are “IO-Link ready” (even if using standard outputs initially) might be more economical than a complete future replacement. However, only do this if the upgrade path is highly probable.
The Future of Price & Value in Induction Sensing
Advancements continue. Smart sensors with integrated IO-Link and diagnostics are becoming more common, offering enhanced value through predictive maintenance capabilities and easier parameterization. While often carrying a higher initial induction sensor price, the operational savings they enable through reduced downtime and simplified maintenance can deliver a compelling return on investment (ROI). Manufacturing efficiency and component miniaturization may also gradually push costs down for standard models, but the demand for higher performance, robustness, and intelligence will simultaneously fuel innovation at the