infrared ir proximity sensor
- time:2025-07-11 00:14:08
- Click:0
Seeing the Unseen: How Infrared Proximity Sensors Transform Detection
Ever walked up to automatic sliding doors at a supermarket and marvelled as they silently glide open? Wondered how your phone screen dims when held to your ear during a call? Or perhaps you’ve interacted with touchless soap dispensers in public restrooms. These seemingly simple conveniences, and countless critical industrial processes, rely on a fascinating piece of technology: the Infrared (IR) proximity sensor. These unassuming devices are masters of detecting nearby objects without physical contact, operating silently and efficiently in the background. This article demystifies IR proximity sensors, exploring their working principles, core components, diverse applications, and compelling advantages.
The Foundation: Understanding Infrared Light
Before delving into the sensor itself, it’s crucial to grasp the medium it uses: infrared light. Occupying a portion of the electromagnetic spectrum just beyond visible red light (wavelengths roughly between 700 nm to 1 mm), infrared radiation is invisible to the human eye. All objects with a temperature above absolute zero emit some level of infrared radiation, though the specific wavelengths and intensity depend on their temperature. This inherent property makes infrared an ideal candidate for proximity sensing and other detection tasks.
How Does an IR Proximity Sensor Work? Unveiling the Core Principle
The fundamental operation of an infrared proximity sensor hinges on the concept of reflective sensing. Here’s a step-by-step breakdown:
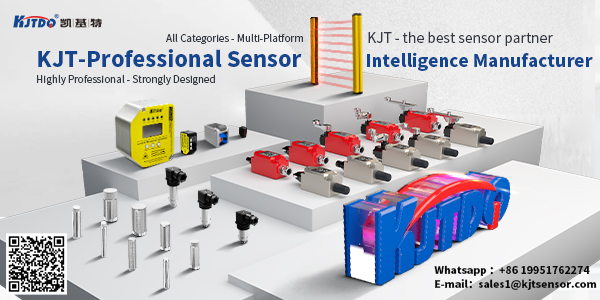
- IR Emission: The sensor houses an infrared LED (Light Emitting Diode). When activated, this LED emits a beam of focused infrared light outward into the surrounding environment.
- Target Interaction: If an object is present within the sensor’s detection range, this emitted IR beam strikes its surface.
- Reflection: A portion of the incident IR light is reflected back towards the sensor. The amount reflected depends on the object’s material, colour, texture, and distance from the sensor. Light-coloured, matte surfaces typically reflect better than dark, shiny ones.
- IR Reception: The sensor incorporates a dedicated photodiode or phototransistor specifically tuned to detect infrared wavelengths. This component acts as the receiver.
- Signal Conversion: The photodiode/phototransistor converts the received reflected IR light into a corresponding small electrical current. The strength of this current is directly proportional to the intensity of the reflected IR light hitting it.
- Signal Processing & Output: Internal circuitry within the sensor processes this electrical signal. It amplifies it, filters out ambient IR noise (like sunlight or indoor lighting), and compares the received signal strength against a predefined threshold. If the reflected signal exceeds this threshold (indicating an object is sufficiently close), the sensor triggers its output. This output is typically a simple digital signal (e.g., logic HIGH/LOW) signifying “object present” or “object absent.” Some advanced models offer analog outputs proportional to distance or intensity.
In essence, these sensors detect the presence of an object by measuring the reflection of its own emitted infrared light off that object. Key components like the infrared LED and photodiode work in tandem to achieve reliable object detection.
Where Do They Shine? Diverse Applications of IR Proximity Sensors
The simplicity, reliability, and non-contact nature of infrared proximity sensors make them incredibly versatile across numerous fields:
- Consumer Electronics: Ubiquitous in smartphones and tablets (screen dimming during calls, preventing accidental touches), gesture recognition systems, TVs (presence detection), laptops, and gaming consoles.
- Home & Building Automation: Enabling automatic faucets, soap/toilet paper dispensers, sliding doors/gates, touchless light switches, and occupancy detection for smart lighting/climate control.
- Robotics & Automation: Critical for object detection, collision avoidance/navigation in mobile robots and AGVs, line following, and detecting end-of-arm-tooling positions or workpieces on assembly lines.
- Industrial Controls: Used for object detection on conveyors, counting items on production lines, detecting paper jams in printers/copiers, liquid level sensing (in transparent containers), and verifying assembly positions.
- Security Systems: Employed in intrusion detection systems (detecting proximity to protected surfaces), vandal-proof interfaces, and intercom activation.
- Automotive: Found in rain sensors (detecting raindrops on the windshield), reversing/obstacle detection systems (lower-speed applications), and gesture controls inside the cabin.
Why Choose IR Proximity Sensors? Key Advantages
Several factors contribute to the widespread adoption of IR proximity sensors for object detection and distance measurement tasks:
- Non-Contact Sensing: Eliminates physical wear and tear on both the sensor and the target object.
- Compact Size & Low Cost: The core components (LED, photodiode) are small and inexpensive to manufacture, enabling integration into space-constrained devices.
- Low Power Consumption: Particularly important for battery-operated devices like smartphones and portable gadgets.
- Fast Response Time: Can detect objects rapidly, making them suitable for high-speed applications like production line counting.
- Simple Interface: Typically provide easy-to-use digital outputs that integrate seamlessly with microcontrollers and logic circuits.
- Solid-State Reliability: Lack moving parts, leading to higher durability and longer operational life compared to mechanical switches.
Important Considerations and Limitations
While highly effective, infrared proximity sensors are not a universal solution. Key points to remember:
- Material Dependency: Performance can be significantly affected by the target object’s surface properties. Highly reflective surfaces (like mirrors) or very dark/absorbent materials may reduce detection range or reliability.
- Ambient IR Interference: Strong sources of ambient infrared light (direct sunlight, incandescent/halogen bulbs) can saturate the receiver and cause false triggers or reduce accuracy. Careful design (modulated signals, optical filtering) helps mitigate this.
- Limited Range: Primarily designed for short-range detection, typically from a few millimetres up to several centimeters. For longer distances, other technologies like ultrasonic sensors or LiDAR might be more suitable.
- Distance Accuracy: While indicative of proximity, standard reflective sensors are generally not precision distance-measuring devices (though specific “IR distance sensors” using triangulation or time-of-flight exist).
- Requires Reflection: Needs a surface capable of reflecting IR light back to the receiver. Detecting transparent objects or objects in a vacuum can be problematic.
Understanding Key Specifications
Selecting the right infrared proximity sensor involves understanding key parameters:
- Sensing Range: The minimum and maximum distance within which the sensor can reliably detect objects.
- Output Type: Digital (ON/OFF), Analog (voltage proportional to reflection/distance), or special protocols (I2C).
- Supply Voltage: Operating voltage range (e.g., 3.3V, 5V).
- Response Time: How quickly the sensor reacts to an object entering or leaving its detection zone.
- Beam Pattern: The shape and spread of the emitted IR beam (narrow vs. wide).
From the seamless convenience of a touchless faucet to the precision required on a high-speed assembly line, infrared proximity sensors are fundamental workhorses in modern technology. Utilizing the properties of invisible infrared light, they provide a simple, cost-effective, and reliable method for object detection in a vast array of applications. Understanding their operating principle – the interplay of an infrared LED emitter and a dedicated photodiode receiver measuring reflected light – demystifies their pervasive presence. While mindful of their limitations regarding material dependency and ambient IR interference, their advantages of non-contact operation, low cost, compact size, and efficiency ensure they will continue to be a vital solution for countless proximity sensing tasks, quietly enabling smarter interactions and automation across our world.