cost of proximity sensor
- time:2025-07-10 00:28:07
- Click:0
What Influences the Cost of Proximity Sensors? Key Factors Explained
Imagine your smartphone screen automatically turning off when held to your ear, preventing accidental taps. Or picture a complex assembly line where robotic arms move with precision, safely halting before colliding with objects. That unseen magic, the silent guardian enabling these interactions, is often a proximity sensor. These ubiquitous components detect the presence or absence of nearby objects without physical contact. But when it comes to sourcing them, the cost of proximity sensors isn’t a single number. Prices can range from mere cents for simple units to hundreds of dollars for highly specialized ones. Understanding why this cost varies so dramatically is crucial for engineers, purchasers, and anyone integrating this essential technology.
At its heart, the proximity sensor cost is dictated by its fundamental sensing technology and the capabilities required. Think of this as the engine determining its core functionality:
- Sensing Principle: The underlying physics significantly impacts manufacturing complexity and materials.
- Inductive Sensors: Detect metallic objects. Generally the most cost-effective option for metal detection, widely used in industrial automation. Prices rise with detection range and housing robustness.
- Capacitive Sensors: Detect both metallic and non-metallic objects (liquids, plastics, wood). Typically slightly more expensive than inductive due to more complex electronics needed to sense subtle dielectric changes.
- Ultrasonic Sensors: Use sound waves, excellent for longer ranges and detecting various materials regardless of color or transparency. Cost more than inductive or capacitive due to the transducer components and sophisticated timing circuitry.
- Optical Sensors (IR Photoelectric): Use infrared light beams (diffuse, retro-reflective, through-beam). Versatile but cost varies greatly: simple diffuse sensors are inexpensive, while long-range, high-precision, or laser-based versions command a premium. Ambient light immunity features add cost.
- Magnetic Sensors (Reed Switches/Hall Effect): Detect magnets. Reed switches are very low cost but mechanical and slow. Solid-state Hall effect sensors offer better performance and durability at a moderate price increase.
Detection Range and Accuracy: You pay for performance. A sensor needing to detect an object precisely at 50mm will inherently cost more than one designed for a simple 5mm presence check. High accuracy, fine resolution, and long sensing distances demand more sophisticated components and calibration. The greater the required performance envelope, the higher the investment.
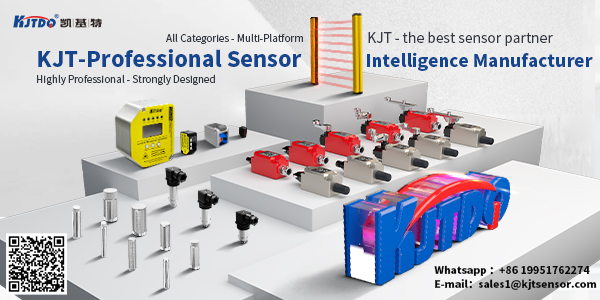
Ruggedness and Environmental Protection: Where will the sensor live?
- Ingress Protection (IP Rating): Sensors exposed to dust, water sprays, or harsh washdowns (common in food processing or outdoor applications) need high IP ratings (e.g., IP67, IP69K). Achieving this requires specialized sealing materials and designs, increasing the cost significantly over basic IP65 or unsealed units.
- Temperature Resilience: Operating reliably in extreme cold (-25°C) or heat (+70°C and beyond) necessitates components rated for those temperatures and potentially specialized housing materials, adding to the price.
- Resistance to Chemicals/Oils: Contact with aggressive substances demands chemically resistant housing materials (like specific stainless steels or specialized plastics), raising manufacturing costs. Stainless steel housings are almost always pricier than nickel-plated brass or plastic equivalents.
- Output Configuration and Complexity: How does the sensor communicate its detection state?
- Basic Digital Outputs (NPN/PNP transistors) are standard and most economical.
- Analog Outputs (e.g., 0-10V, 4-20mA) providing distance information are more complex and costly.
- IO-Link compatibility, enabling advanced diagnostics, parameterization, and process data integration, adds significant cost due to the required communication hardware and software integration.
- Materials and Build Quality: Beyond just environmental protection:
- High-quality, durable sensing faces resist wear and abrasion.
- Premium connectors offer better reliability than simple flying leads.
- Internal component quality (resistors, ICs, capacitors) affects longevity and stability, impacting long-term cost of ownership, even if the initial sensor cost is lower.
- Robust construction suitable for high-vibration environments requires design and material choices that boost the price.
Brand Reputation and Support: Established manufacturers with a track record of reliability, extensive global support networks, and comprehensive documentation often command a price premium. You’re paying for peace of mind, guaranteed supply chains, and readily available technical expertise. The cost of proximity sensors from niche or lesser-known brands might seem attractive initially, but hidden expenses like shorter lifespan, difficulty sourcing replacements, or lack of support can erase those savings.
Order Volume: Like most electronic components, proximity sensor prices follow economies of scale. Ordering thousands of units unlocks substantial discounts compared to buying a single piece. High-volume OEM applications see vastly different unit costs compared to maintenance replacements or prototyping needs.
Special Features: Requirements like:
- Extended Temperature Ranges (e.g., -40°C to +100°C+)
- High Switching Frequency capabilities.
- Enhanced EMI/RFI Immunity for electrically noisy environments.
- Safety-Rated versions (e.g., SIL, PL) for critical applications.
- Specialized Form Factors or custom modifications. Each of these adds layers of engineering and specialized components, driving the cost upwards.
Navigating the Proximity Sensor Cost Landscape: Smart Selection
Understanding these factors isn’t just academic; it’s critical for making informed procurement decisions and optimizing project budgets:
- Define the Exact Requirement: What material needs detection? At what range? What’s the operating environment (temp, moisture, chemicals)? What output is required? Resist feature creep – don’t pay for capabilities you don’t genuinely need. Precision in specification prevents overspending.
- Consider Total Cost of Ownership (TCO): Look beyond the initial purchase price. A slightly more expensive proximity sensor with a stainless steel housing and high IP rating in a harsh environment will likely last far longer and cause less downtime than a cheaper, less protected unit that fails prematurely. Factor in potential maintenance costs and production interruptions.
- Balance Brand and Budget: While premium brands offer advantages, thoroughly evaluate reputable mid-tier manufacturers. They often provide excellent value for performance in standard applications. Read reviews and seek independent testing data if available.
- Explore Volume Discounts: For production runs, engage suppliers early to negotiate pricing based on projected annual volumes. Consolidating sensor types across machines can also increase bargaining power.
- Consult Experts: Distributors and manufacturer representatives possess deep knowledge. Present your specific application details and environmental challenges; they can often recommend the most cost-optimized proximity sensor solution that meets your technical needs, potentially saving you from selecting an over-engineered (and overpriced) option.
The cost of proximity sensors reflects their sophistication and the demanding roles they fulfill. From the humble inductive sensor ensuring machine safety to complex optical units guiding intricate assembly, the price tag is shaped by physics, performance demands, environmental challenges, and manufacturing realities. By dissecting the key cost drivers – **sensing technology, range, ruggedness, output type, materials,