proximity sensor 10mm
- time:2025-07-09 03:10:16
- Click:0
The Power of Precise Detection: Unlocking Efficiency with 10mm Proximity Sensors
Imagine an automated assembly line where components must be positioned with pinpoint accuracy. A robot arm swings towards its target, needing to know exactly when to stop or activate a tool. Mere millimeters make the difference between flawless operation and costly collisions. This is where the 10mm proximity sensor emerges as a silent, indispensable hero. Far from arbitrary, this specific sensing range represents a crucial sweet spot in industrial automation, packaging machinery, robotics, and countless other applications demanding reliable, close-range detection without physical contact.
What exactly defines a proximity sensor? Simply put, it’s a device that detects the presence or absence of an object within its detection field without needing to touch it. Operating primarily on electromagnetic principles (most commonly inductive sensing for metallic objects), these sensors offer significant advantages over mechanical limit switches: reliability, long operational life (no moving parts to wear out), high switching speeds, and resistance to harsh environments like dust, oil, and vibration. The “10mm” specification refers to the nominal sensing distance – the guaranteed distance from the sensor’s face at which it will reliably detect a standard target.
But why is 10mm such a prevalent and critical specification? It occupies the “Goldilocks zone” for many demanding applications:
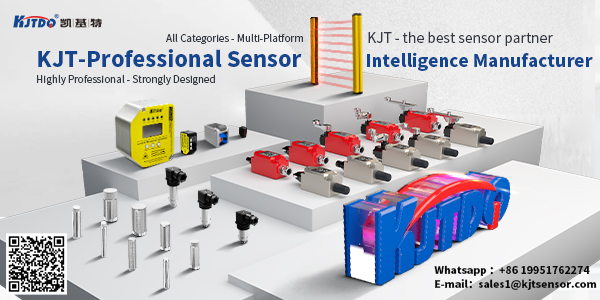
- Optimal Safety & Accuracy: In tight spaces common on machinery, a sensor needs sufficient range to detect an object before potential impact but cannot protrude excessively or risk being struck itself. 10mm provides that vital buffer zone, allowing machinery to react swiftly and precisely to component positioning, door closures, or end-of-travel detection.
- Versatility & Standardization: This range covers a vast array of common tasks. Detecting small components on conveyors, verifying the presence of pallets or tooling, confirming cylinder piston position, or sensing the closed position of guards – these scenarios frequently fall comfortably within a 10mm detection envelope. Furthermore, 10mm is a standardized offering from virtually every major sensor manufacturer, ensuring wide availability and compatibility.
- Robustness & Size: Sensors designed for a 10mm range, especially the ubiquitous M8 (thread size) and M12 (thread size) cylindrical models, strike an excellent balance between compact size and robust construction. They are small enough to fit into densely packed control panels or on moving machine elements without adding significant bulk, yet large enough to house durable electronics and sensing coils capable of reliable operation in demanding factory settings. Their standardized form factors also simplify mounting and replacement.
The core technology behind the most common 10mm inductive proximity sensor relies on eddy currents. The sensor generates a high-frequency electromagnetic field from its face. When a metallic object enters this field (within the nominal 10mm range), eddy currents are induced in the target object. These currents absorb energy from the sensor’s oscillator circuit. The sensor electronics detect this energy loss, triggering a solid-state switch (typically PNP or NPN transistor output) to signal the object’s presence. This purely electronic operation is key to their longevity and speed, capable of millions of switching cycles.
Selecting the right proximity sensor 10mm model involves considering several critical factors beyond just the range:
- Target Material: Standard inductive sensors detect ferrous metals (like iron and steel) most effectively, often at their full 10mm rating. Detection distance decreases for non-ferrous metals (like aluminum, brass, copper). Some specialized sensors offer optimized detection for stainless steel or non-ferrous targets. Capacitive sensors (also available in 10mm ranges) can detect non-metallic materials like plastic, wood, or liquids.
- Output Configuration: Do you need a Normally Open (NO) or Normally Closed (NC) signal? What is the required output type: PNP (sourcing), NPN (sinking), or Analog (e.g., 4-20mA)? Choosing the correct output configuration is essential for compatibility with your control system (PLC, microcontroller).
- Environmental Ratings: Look for high IP (Ingress Protection) ratings (e.g., IP67, IP68, IP69K) indicating resistance to dust and water. Resistance to oils, coolants, welding spatter, and extreme temperatures might also be crucial depending on the installation location. Housing material (often nickel-plated brass or stainless steel) significantly impacts durability.
- Electrical Specifications: Ensure the sensor’s operating voltage (commonly 10-30V DC) and current rating match your power supply and load requirements. Consider factors like short-circuit protection, reverse polarity protection, and surge immunity for enhanced reliability.
- Form Factor: Cylindrical sensors (M8 x 1, M12 x 1 threaded) are most common. Consider barrel length (how far it protrudes) and required mounting (brackets, flush/non-flush mounting capability) for your specific space constraints. Flush-mountable sensors are ideal when the sensor face needs to be protected from physical damage.
The applications for proximity sensor 10mm units are vast and impactful:
- Industrial Automation: Position sensing in pneumatic/hydraulic cylinders, end-of-travel detection on linear actuators, verifying part presence/absence on conveyors or in fixtures, robotic tooling confirmation, rotary position indexing. Their reliability keeps production lines moving.
- Packaging Machinery: Detecting cartons, bottles, or lids; monitoring fill levels (using capacitive variants); confirming case sealer flap positions; guarding access points. Precision detection ensures packaging integrity.
- Material Handling: Verifying pallet placement, detecting objects on roller conveyors, gate/divert arm position confirmation, safety door monitoring. They enhance flow and safety in logistics.
- Automotive Assembly: Confirming component seating (e.g., engines onto mounts), weld gun positioning, detecting tool presence in robotic arms, fixture clamping verification. Accuracy is paramount in vehicle construction.
- Machine Tools: Tool changer position detection, workholding fixture confirmation, coolant level monitoring (capacitive), guarding applications. They protect valuable equipment and ensure correct operation.
When integrating a 10mm proximity sensor, remember these best practices: ensure the target size and material are appropriate for the chosen sensor type; mount the sensor securely; maintain the specified nominal sensing distance, accounting for temperature variations and installation factors which might slightly reduce the effective range; protect wiring from damage and interference; and regularly clean the sensor face in dirty environments to maintain optimal performance. The 10mm sensing distance is specified under ideal conditions; real-world installation may require slight adjustment.
The 10mm proximity sensor exemplifies the power of targeted engineering. It’s not simply a component; it’s a critical enabler of efficiency, safety, and precision across vast sectors of modern industry. Its standardized size, reliable operation, and perfect suitability for countless close-range detection tasks make it a fundamental building block in the automated world. By understanding its capabilities, specifications, and ideal applications, engineers and technicians can leverage this powerful tool to build smarter, more responsive, and more dependable systems. Choosing the correct proximity sensor 10mm variant – whether inductive, capacitive, shielded