festo inductive proximity sensor
- time:2025-07-09 00:56:28
- Click:0
Festo Inductive Sensors: Unlocking Reliable Proximity Detection in Automation
Precision, reliability, non-contact sensing. In the fast-paced world of industrial automation, where milliseconds count and unexpected downtime costs dearly, these attributes aren’t just desirable – they are essential. At the forefront of providing solutions that embody these principles stands Festo, a global leader in automation technology, renowned for its high-quality pneumatic and electrical components. Among its extensive portfolio, Festo inductive proximity sensors represent a cornerstone technology, enabling countless machines to “see” metal targets and react with unwavering consistency. Understanding their function, strengths, and strategic applications is key to optimizing automated processes for peak performance and robustness.
Inductive proximity sensors operate on a fundamental electromagnetic principle. Inside the sensor head, an oscillator generates a high-frequency electromagnetic field. When a ferrous (iron-based) or non-ferrous (like aluminum, brass, copper) metal target enters this active field, Eddy currents are induced within the target material. This phenomenon absorbs energy from the oscillator circuit. The sensor’s sophisticated electronics detect this energy loss, triggering a clean, reliable output signal – typically switching a load ON or OFF – indicating the target’s presence without any physical contact. This non-contact operation is arguably the sensor’s most significant advantage, eliminating mechanical wear and tear and enabling incredibly long service lives. Furthermore, their inherent construction makes them exceptionally immune to dirt, dust, moisture, oil, and vibration, factors that often plague other sensing technologies. They also operate independently of ambient light conditions, making them ideal for enclosed spaces or variable lighting environments. While their core function is detecting metal objects, the specific material (ferrous vs. non-ferrous) does influence the sensor’s nominal sensing distance (Sn), a critical parameter specified by Festo for each model.
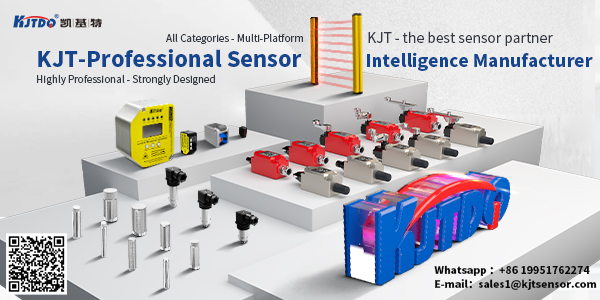
Festo leverages this proven inductive sensing technology and elevates it through superior engineering, rigorous quality control, and a deep understanding of industrial needs. Choosing Festo inductive proximity sensors means investing in solutions designed to excel in demanding automation landscapes:
- Robust Construction & Longevity: Built to withstand harsh industrial realities – shocks, vibrations, cutting fluids, coolants, and wide temperature ranges – Festo sensors deliver exceptional operational life, minimizing costly replacements and maintenance interventions.
- Enhanced Process Reliability: Consistent switching behavior, high repeat accuracy, and immunity to environmental contaminants ensure dependable detection cycle after cycle, shift after shift, directly contributing to overall equipment effectiveness (OEE).
- Versatility in Design: Festo offers an extensive range to suit diverse mounting and application constraints. This includes diverse housing shapes (tubular in various diameters like M5, M8, M12, M18, M30; rectangular/square blocks), mounting styles (flush, non-flush), connection types (cable, M8/M12 connector), and output configurations (NPN/PNP, normally open/normally closed, NO+NC). Popular lines include the SIE/SIEN series for diverse applications and the SMT/SMT-8M series featuring particularly compact M8 designs.
- Advanced Features: Beyond basic detection, many Festo inductive sensors incorporate IO-Link communication. This powerful digital interface enables remote configuration, real-time diagnostics, process data monitoring (e.g., switching distance variations, temperature), and simplified device replacement, paving the way for Industry 4.0 readiness and predictive maintenance strategies. Key parameters like switching hysteresis and temperature behavior are precisely defined and guaranteed.
- Engineering Excellence: Features like short-circuit protection, reverse polarity protection, and high electromagnetic compatibility (EMC) resilience ensure safe and trouble-free operation even in electrically noisy environments. Their modular design philosophy also simplifies integration and system design.
- Global Support & Documentation: Backed by Festo’s worldwide technical support network and comprehensive, easily accessible datasheets and CAD models, integrating and troubleshooting these sensors is streamlined.
The applications for Festo inductive proximity sensors span virtually every sector of automation:
- Position Verification: Confirming the presence of cylinders in end positions (cylinder position sensing), verifying parts are correctly seated in fixtures or pallets.
- End-of-Stroke Detection: Reliably signaling when a pneumatic or hydraulic cylinder has fully extended or retracted.
- Object Detection & Counting: Detecting metal parts on conveyors, within machinery, or during packaging processes. Highly reliable for counting metallic components.
- Speed Monitoring: Detecting rotating targets (e.g., gear teeth, encoder flags) for rotational speed measurement or overspeed detection.
- Machine Safety: Used in non-safety related applications for part presence checking before initiating a cycle (e.g., guarding interlocks often require certified safety sensors).
- Material Handling & Robotics: Guiding robotic arms, confirming gripper closure on metal parts, detecting pallet presence.
Selecting the optimal Festo inductive sensor requires careful consideration:
- Target Material: Identify whether the target is primarily ferrous or non-ferrous.
- Required Sensing Distance (Sn): Choose a sensor with a specified Sn suitable for the application gap. Remember actual sensing distance can be less for non-ferrous targets. Consider mounting (flush vs. non-flush).
- Environmental Conditions: Assess exposure to temperature extremes, chemicals, washdowns, or significant mechanical stress to select the appropriate housing material (typically nickel-plated brass or stainless steel variants available) and ingress protection (IP) rating (commonly IP67 or higher).
- Mounting & Space Constraints: Determine the available space and preferred mounting method (e.g., threaded barrel, slot mount block).
- Electrical Requirements: Define the needed supply voltage (e.g., 10-30V DC) and output type (NPN sinking, PNP sourcing, analog, IO-Link). Ensure compatibility with the controller’s input card.
- Special Features: Determine if enhanced diagnostics via IO-Link or specific approvals (e.g., for food industry) are necessary. Festo’s selection tools and expert technical support are invaluable assets during this process.
In the intricate dance of modern industrial automation, reliable sensing forms the bedrock of efficiency and uptime. Festo inductive proximity sensors, leveraging decades of engineering expertise and a commitment to robust, high-performance solutions, provide an indispensable tool for engineers seeking contactless, wear-free, and highly resilient metal object detection. Their versatility, durability, and integration into smart factory concepts via IO-Link make them a strategic choice for optimizing countless applications, from simple position feedback to complex process monitoring. Integrating Festo sensors means integrating predictable performance and long-term reliability into the very heart of the production line.