electromagnetic induction sensor
- time:2025-07-09 00:49:25
- Click:0
The Invisible Touch: How Electromagnetic Induction Sensors Shape Modern Technology
Imagine unlocking your car door without pressing a button, a factory robot detecting metal parts without touching them, or intricate medical instruments guided with sub-millimeter precision. These feats aren’t magic; they’re powered by the sophisticated capabilities of *electromagnetic induction sensors*. Acting as the unseen perception layer in countless devices, these sensors translate subtle interactions with magnetic fields into vital data, driving efficiency, safety, and innovation across a staggering range of applications.
At its core, electromagnetic induction relies on a fundamental principle discovered by Michael Faraday: a changing magnetic field induces a voltage (electromotive force or EMF) in a nearby conductor. Modern electromagnetic induction sensors leverage this phenomenon as their primary sensing mechanism. They don’t rely on physical contact; instead, they interact with their environment through carefully engineered magnetic fields.
How Does an Electromagnetic Induction Sensor Operate?
The typical architecture involves several key components:
- Excitation Coil: This coil, driven by an alternating electrical current, generates a primary, oscillating magnetic field around the sensor head.
- Target Object: This is the object being sensed. Crucially, it must be electrically conductive (e.g., metals like aluminum, steel, copper). Non-conductive materials like plastic, wood, or ceramics generally do not trigger the effect.
- Eddy Currents: When the primary magnetic field intersects the conductive target, it induces circulating electrical currents within the target material itself. These are called eddy currents.
- Secondary Magnetic Field: The eddy currents, flowing through the target’s resistance, generate their own opposing magnetic field. This is the induced secondary field.
- Detection Coil/Circuit: The sensor contains circuitry designed to detect the changes caused by the secondary field. This might be:
- A separate detection coil whose impedance (resistance and inductance) changes due to the interaction of the primary and secondary fields.
- The same excitation coil whose characteristics (like inductance or impedance) change due to the “loading” effect from the target’s eddy currents.
- Signal Processing: The subtle changes in voltage, current, impedance, or resonant frequency caused by the target’s presence and proximity are amplified and processed by sophisticated electronics. This raw signal is converted into a stable, usable output signal (analog voltage/current or digital) proportional to the measured parameter, most often distance or position.
Why Choose Electromagnetic Induction Sensing? The Key Advantages
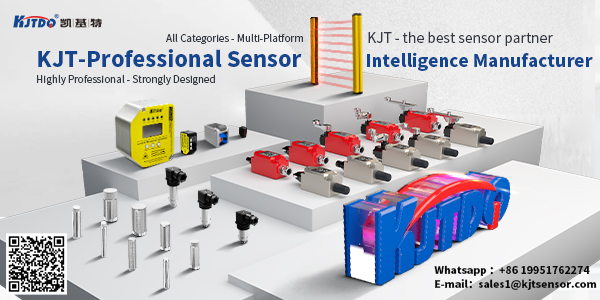
This unique operating principle unlocks a powerful suite of benefits:
- Non-Contact Operation: The sensor never physically touches the target. This eliminates friction, wear, and potential damage to both the sensor and the target, significantly enhancing longevity and reliability, especially in harsh environments.
- High Precision and Resolution: Modern designs offer exceptional resolution, often down to the micron level, and high repeatability for critical positioning tasks.
- Robustness: Many sensors feature rugged housings and can withstand challenging industrial conditions – dirt, dust, oil, water splashes, and even high temperatures are no match for well-designed units. Their sealed construction protects internal electronics.
- High-Speed Response: Capable of detecting rapid changes in target position or vibration with frequencies often into the tens of kilohertz range, ideal for dynamic monitoring and control applications.
- Material Specific: While a limitation in some contexts, the exclusive sensitivity to conductive materials is a major advantage where differentiating between metal and non-metal is crucial (e.g., detecting metal shavings, sensing specific metallic components).
Where the “Invisible Touch” Makes a Tangible Difference
The versatility of electromagnetic induction sensors makes them indispensable across numerous sectors:
- Industrial Automation & Manufacturing: Displacement sensors monitor runout, vibration, bearing wear, and thermal expansion on rotating shafts. Position sensors provide feedback for hydraulic/pneumatic cylinders (cylinder position sensors). Proximity switches sense the presence or absence of metal parts along conveyor lines, triggering actions reliably.
- Automotive: Used in transmission and engine systems (e.g., crankshaft/camshaft position sensing for timing), suspension monitoring, throttle position, and anti-lock braking systems (ABS) wheel speed detection. Power steering torque sensors also often employ this technology. Keyless entry systems detect the key fob’s presence.
- Aerospace: Monitoring critical parameters like blade tip clearance in jet engines (vital for efficiency and safety), structural health monitoring, and control surface positioning due to their robust nature.
- Medical & Scientific Instruments: Providing precise position feedback in surgical robots, imaging equipment (MRI component positioning), and laboratory automation systems requiring contamination-free sensing.
- Energy: Vibration and position monitoring on turbines (steam, gas, hydro), generators, and large pumps within power plants.
- Consumer Electronics: Found in devices requiring non-contact position detection in compact spaces, though often overshadowed by other technologies in mainstream consumer products.
Beyond Basic Presence: The Power of Measurement
While simple proximity detection is common, the true strength lies in precision displacement and position sensing. By precisely calibrating the relationship between the distance to the conductive target and the sensor’s output signal, engineers gain a powerful tool for:
- Monitoring bearing clearances and predicting failures.
- Measuring vibration spectra for machinery health diagnostics.
- Controlling the flatness of rolled metal sheets.
- Ensuring precise alignment in assembly processes.
- Gauging material thickness (using specialized configurations).
Optimizing Performance: Factors to Consider
Achieving optimal results requires attention to several factors:
- Target Material: Different metals (ferrous/non-ferrous, conductivity, permeability) influence the strength of induced eddy currents and the sensor’s sensing range.
- Target Size and Shape: The target must generally be large enough to adequately interact with the sensor’s magnetic field. Shape also affects eddy current distribution.
- Operating Distance: The sensor requires calibration for its intended sensing range. Performance decreases significantly outside this optimal range.
- Environmental Influences: While robust, extreme temperatures, strong external magnetic fields, or conductive materials near the target can affect readings and may require shielding or specific mounting considerations.
- Frequency Selection: The excitation frequency influences penetration depth (skin effect) and sensitivity to different target material properties, allowing some tuning for specific applications.
From Faraday’s Discovery to Future Innovation
Electromagnetic induction sensors are a brilliant application of fundamental physics, transforming an invisible interaction into actionable intelligence. Their unique blend of non-contact operation, high precision, robustness, and speed ensures they remain a cornerstone technology in demanding industrial, automotive, aerospace, and scientific fields. As electronics continue to miniaturize and processing power grows, we can expect even more sophisticated and application-specific designs, further expanding the reach of this remarkable non-contact sensing technology. Their ability to “touch without touching” continues to be an engine for innovation, quietly shaping the performance and reliability of the modern world.