6mm proximity sensor
- time:2025-07-08 04:27:43
- Click:0
6mm Proximity Sensor: The Compact Powerhouse for Precision Detection
Imagine a world where machines operate with uncanny awareness, where robotic arms move with millimeter accuracy, and production lines hum with flawless efficiency. At the heart of this precision often lies an unassuming yet vital component: the 6mm proximity sensor. This compact marvel is far more than just a small electronic device; it’s a fundamental enabler of automation and control in countless applications where space is tight, but accuracy is paramount. Let’s delve into what makes these tiny titans essential.
Understanding the 6mm Proximity Sensor
Put simply, a proximity sensor detects the presence or absence of an object without physical contact. The “6mm” specifically refers to its nominal sensing distance. This means the sensor is designed to reliably detect a standard target (usually a piece of ferrous metal like mild steel) positioned up to 6 millimeters away from its sensing face. This range represents a sweet spot in industrial automation – offering sufficient detection distance for many tasks while allowing for incredibly compact sensor designs to fit into confined spaces where larger sensors simply cannot go. The most common type for this range is the inductive proximity sensor.
How Does a 6mm Proximity Sensor Work? (The Inductive Principle)
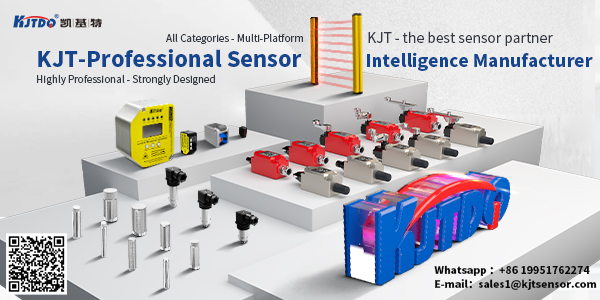
Most 6mm proximity sensors operate on the inductive principle. Here’s the science simplified:
- Internal Oscillator: The sensor contains an oscillator circuit that generates a high-frequency electromagnetic field emanating from the sensing face.
- Field Interaction: When a metallic object (typically ferrous metals like iron or steel, but also detectable non-ferrous like aluminum or copper at reduced ranges) enters this electromagnetic field within the 6mm nominal range.
- Eddy Currents: This metallic target induces small swirling electrical currents called “eddy currents” within itself.
- Damping Effect: The creation of these eddy currents absorbs energy from the sensor’s oscillating field, causing it to dampen or weaken.
- Detection Circuit: An internal circuit within the sensor constantly monitors the amplitude of the oscillator’s field.
- Output Signal Switch: When the damping effect exceeds a certain threshold (indicating the target is within the specified 6mm sensing range), the sensor’s output state changes. This switch can be either Normally Open (NO) or Normally Closed (NC), sending a signal to a controller like a PLC indicating “target present.”
Key takeaway: It’s a non-contact, wear-free detection method ideal for harsh environments.
Why Choose a 6mm Sensing Range?
This specific range isn’t arbitrary; it offers distinct advantages:
- Compact Size: The sensor body itself can be extremely small (e.g., M5, M8, or M12 threaded barrels). This compact size is crucial for integration into machinery with tight tolerances, robotic grippers, small assemblies, and miniature automation equipment.
- High Precision & Repeatability: The relatively short range allows for very precise positioning control. Sensors can detect minute positional changes of a target within fractions of a millimeter, ensuring high repeatability in automated processes.
- Immunity to Contaminants: Being non-contact, they are unaffected by dirt, dust, oil, or moisture (assuming appropriate IP rating – look for IP67 or higher for industrial ruggedness) that could foul mechanical switches. This translates to superior reliability and lower maintenance.
- Fast Response Time: With no moving parts, inductive sensors switch states incredibly quickly (often in microseconds), enabling high-speed counting and detection on fast-moving production lines. This speed is critical for modern automation.
- Robust Construction: Housed in durable materials like nickel-plated brass or stainless steel, they withstand vibration, shock, and harsh industrial environments far better than mechanical limit switches.
- Versatility: While ideal for metal detection, variations can handle specific non-ferrous metals or even incorporate factors like hysteresis (the difference between switch-on and switch-off points) to prevent output chattering on vibrating targets.
Where are 6mm Proximity Sensors Used? (Real-World Applications)
The applications are vast and span numerous industries:
- Factory Automation: Detecting piston position in compact pneumatic cylinders, verifying part presence in pallets or fixtures, confirming end-of-stroke on small actuators, monitoring gear teeth rotation on small mechanisms. Essential for assembly line control.
- Robotics: Providing precise feedback on gripper jaw position, detecting tool changes, verifying workpiece pickup/drop-off within the robot’s tight work envelope. Crucial for robotic accuracy.
- Packaging Machinery: Counting small items on conveyors, detecting foil seals, verifying cap placement, confirming carton flap closure in confined machine sections.
- Machine Tools: Monitoring tool position (especially in tool changers), detecting chuck jaws closed, ensuring workpiece clamping, providing spindle indexing signals.
- Material Handling: Detecting presence of small metal parts in chutes, verifying slider or shuttle positions in compact transfer systems.
- Security & Access Control: Hidden detection points in safes or access panels (detecting metal components).
- Consumer Electronics Manufacturing: Precision positioning in micro-assembly processes for phones, computers, and wearable devices.
Choosing the Right 6mm Proximity Sensor
Selecting the optimal sensor involves considering several factors beyond just the 6mm range:
- Sensor Type: Inductive is standard for metals. Need to detect plastic, wood, or liquids? Consider capacitive sensors (though their range might differ slightly for equivalent size). Photoelectric sensors offer longer ranges but can be larger.
- Housing Size & Shape: Threaded barrel (M5, M8, M12), block, or rectangular? Determined by mounting constraints.
- Output Type: PNP (sourcing) or NPN (sinking) transistor outputs are most common for PLCs. Relay outputs also exist. Voltage level (10-30V DC typical)? Solid-state vs mechanical relay?
- Connection Style: Pre-wired cable, quick-disconnect (M8, M12 connectors), or terminal block?
- Environmental Rating (IP Code): Essential for dust and water resistance (IP67 is standard for washdown environments, IP69K for high-pressure cleaning). Temperature range?
- Target Material: Confirm the sensor is suitable for the specific metal you need to detect (ferrous, non-ferrous, stainless steel). Detection range can vary slightly based on material. Always consult the datasheet.
- Flush or Non-Flush Mounting: Flush-mountable sensors can be embedded in metal, saving space. Non-flush offer slightly longer sensing ranges but require clearance around them.
Installation Tips for Peak Performance
- Mount Securely: Prevent vibration from causing false triggers or damage.
- Respect Sensing Range: Factor in hysteresis and ensure the target consistently enters within the actual operating range (typically 0-6mm). Don’t mount it expecting reliable detection right at the nominal 6mm edge under all conditions.
- Mind the Surroundings: Avoid mounting large metal masses adjacent to the sensor’s sides, which can interfere with the sensing field. Provide the recommended lateral clearance.
- Correct Wiring: Double-check PNP/NPN wiring compatibility with your controller. Reverse polarity protection is common but not universal. Connect the brown wire (+V), blue wire (0V/GND), and black wire (signal output) correctly.
- Check Load Compatibility: Ensure the sensor’s output can handle the current/voltage requirements of the device it’s controlling (PLC input, relay coil, etc.). Avoid overloading.
- Test Thoroughly: Verify detection under all expected operating conditions (target present/absent, speed, environment).
The 6mm proximity sensor might be small in stature, but its impact on modern automation is immense. By offering **reliable