delta proximity sensor
- time:2025-07-08 04:20:41
- Click:0
Delta Proximity Sensors: Mastering Precision in Micro-Measurement
Title: Delta Proximity Sensors: The Key to Ultra-Precise Position Detection
Imagine assembling a smartphone where a component needs placement accuracy finer than the width of a human hair. Or monitoring the microscopic vibrations of a high-speed turbine blade. Precision isn’t just desirable in these scenarios; it’s absolutely critical. Enter the Delta Proximity Sensor, a specialized category designed specifically for detecting vanishingly small changes in distance or position – the “delta” (Δ), or change, being paramount. This article delves into how these sensors achieve remarkable accuracy and where they deliver indispensable value.
Unlike standard proximity sensors designed primarily for presence/absence detection or larger distance ranges, Delta Proximity Sensors are engineered for high-resolution differential measurement. Their primary function isn’t just to sense if an object is nearby, but to provide an extremely precise analog output signal proportional to minute variations in the distance to a target. Think of them as the micrometer gauges of the sensor world.
The Core Principle: Sensitivity to Minute Change
At their heart, most delta proximity sensors operate similarly to standard inductive or capacitive proximity sensors:
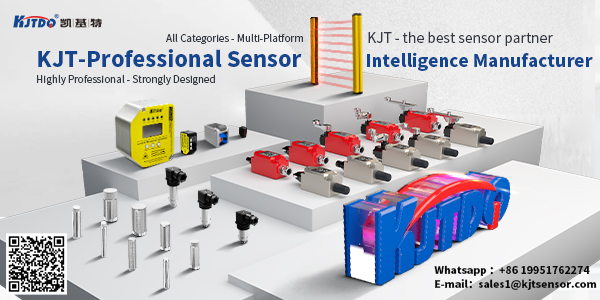
- Inductive Delta Sensors: Generate an electromagnetic field. When a conductive target enters this field, eddy currents are induced, causing a measurable change in the sensor’s internal oscillator circuit. The key difference lies in the sensitivity and signal conditioning. Delta inductive sensors employ high-frequency oscillators and sophisticated electronics to detect incremental changes in this oscillation caused by minuscule target movements, often down to the sub-micrometer level.
- Capacitive Delta Sensors: Detect changes in capacitance between the sensor’s active surface and a target (conductive or non-conductive). Again, delta versions are optimized to focus on tiny fluctuations in this capacitance, translating them into precise analog voltage or current output changes corresponding to distance deltas. They excel with non-metallic targets where inductive sensors falter.
What Truly Defines a “Delta” Sensor?
Several characteristics set these sensors apart:
- Micrometer-Level Resolution: Their ability to discern changes far smaller than standard proximity sensors. Resolution can often reach fractions of a micrometer (µm).
- High Linearity: The output signal is exceptionally proportional to the actual distance change over a defined, albeit typically small, measuring range (e.g., hundreds of micrometers to a few millimeters). This ensures accurate representation of position shifts.
- Stability & Low Drift: Maintaining accuracy over time and varying environmental conditions (like temperature fluctuations) is crucial. Delta sensors feature robust designs and temperature compensation circuits to minimize output drift.
- Differential Focus: While they have an absolute zero point, their primary output information is the deviation from a nominal position or a relative change detected between readings.
- High-Frequency Response: Capable of detecting rapid vibrations or very fast positional changes, essential for dynamic applications.
Where High-Precision Delta Matters Most
Delta proximity sensors find their niche in applications demanding extreme precision and stability:
- Precision Machining & Metrology: Monitoring tool wear in real-time by detecting minute changes in tool position, verifying part dimensions during grinding or turning operations with micron-level tolerances.
- Semiconductor Manufacturing: Critical for wafer steppers, lithography equipment, and inspection systems where alignment and stage positioning require nanometric precision. Vibration monitoring of sensitive equipment is another key use.
- Electronics Assembly: Precisely placing surface-mount components (SMDs), controlling solder paste application thickness, and verifying connector insertion depth.
- Optics & Photonics: Aligning optical components like lenses, lasers, and fibers where angular or positional shifts of microns cause significant performance degradation.
- Micro-Positioning Stages: Providing feedback for closed-loop control of piezo stages or other actuators used in microscopy, biotechnology, and nanofabrication.
- Vibration Analysis: Detecting ultra-small amplitude vibrations in bearings, spindles, or delicate machinery for predictive maintenance purposes.
- Quality Control & Inspection: Measuring tiny variations in surface flatness, coating thickness, or runout on rotating shafts.
Integrating Delta Proximity Sensors: Key Considerations
Successfully leveraging these high-precision tools requires attention to detail:
- Target Material & Size: For inductive types, the target must be conductive (usually ferrous metals offer best performance). Capacitive types work with a wider range but require stable dielectric properties. Target size must be adequate for the sensor’s field.
- Mounting Rigidity: Any flex or vibration in the sensor mount itself will introduce false signals. Secure, stable mounting is non-negotiable.
- Environmental Factors: Temperature changes are the primary concern for drift. Choosing sensors with integrated temperature compensation and minimizing ambient temperature swings are essential. Contaminants like oil or metal chips can also affect performance (especially capacitive sensors).
- Signal Conditioning & Calibration: High-quality signal conditioners or controllers are needed to interpret the sensitive analog output accurately. Regular calibration against known standards may be necessary for the most demanding applications.
- Measuring Range Selection: Delta sensors have very limited absolute ranges. Choosing a sensor with a range that matches the expected positional variations is crucial for optimal resolution and linearity.
Beyond Standard Proximity: The Delta Advantage
While standard inductive or capacitive proximity sensors excel at presence detection and larger gap monitoring, they lack the finesse required for true micro-measurement. The defining advantage of the delta proximity sensor lies in its unparalleled sensitivity to infinitesimal changes. This capability enables engineers to achieve levels of control, quality, and insight that were previously impossible or required vastly more expensive measurement systems. Their differential measurement approach inherently minimizes errors related to absolute distance variations, focusing instead on the critical positional shift or vibration.
In industries pushing the boundaries of miniaturization, speed, and precision, delta proximity sensors are indispensable tools. They transform minute physical changes into highly reliable electronic signals, providing the critical feedback needed for ultra-precise control, stringent quality assurance, and advanced diagnostic capabilities in the most demanding micro-engineering environments. Their ability to resolve the “delta” reliably makes them fundamental components in the relentless pursuit of manufacturing and measurement perfection.