namur inductive sensor
- time:2025-07-08 03:45:28
- Click:0
NAMUR Inductive Sensors: The Essential Guardian in Hazardous Industrial Zones
Imagine a spark in a chemical processing plant or a grain silo filled with combustible dust. The potential for catastrophe is immense. In environments laden with flammable gases, vapors, or dust, standard electrical equipment becomes a significant risk. This is where NAMUR inductive sensors step in – not merely as proximity detectors, but as critical safety components engineered to operate reliably where the slightest spark could ignite disaster. Understanding their unique design and purpose is fundamental for safety and efficiency in high-risk industries.
What Exactly is a NAMUR Inductive Sensor?
At its core, an inductive proximity sensor detects the presence or absence of metallic objects without physical contact, using an electromagnetic field. A NAMUR inductive sensor is a specific intrinsically safe variant of this technology. The term “NAMUR” originates from Normenarbeitsgemeinschaft für Mess- und Regeltechnik in der chemischen Industrie (Standardization Association for Measurement and Control in the Chemical Industry). This German group developed the NAMUR standard (NE 21, now covered by EN 60947-5-6) specifically to define the operating characteristics and electrical interface for sensors used in hazardous areas (HazLoc).
The defining feature of a NAMUR sensor isn’t its physical detection principle (which is standard inductive operation), but its intrinsically safe output circuit designed to prevent any spark or thermal energy capable of igniting an explosive atmosphere.
How Do NAMUR Sensors Function Safely?
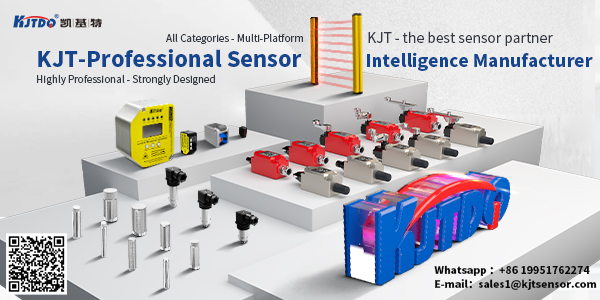
Here’s what sets them apart:
- Low Energy Signaling: Unlike standard PNP or NPN sensors that switch significant current (e.g., 100-200mA), a NAMUR sensor operates with a very low current signal, typically controlled by an external intrinsically safe barrier or isolator. The sensor itself doesn’t directly power the load.
- The Role of the Intrinsic Safety Barrier: This safety device is crucially installed in the safe area. It limits both the current supplied to the sensor and the voltage/current returning from it. This ensures that under both normal operation and fault conditions (like a short circuit), the energy present in the hazardous area circuit remains below levels that could cause ignition. The sensor is intrinsically safe only when used with an approved barrier or isolator.
- Specific Signal Ranges: A NAMUR sensor outputs a specific current range instead of a simple “on/off” voltage:
- Target Absent (Open Circuit): Approx. < 1.2 mA (typically interpreted as a “0” or “Off” state).
- Target Present (Closed Circuit): Approx. > 2.1 mA (typically interpreted as a “1” or “On” state).
- Fault Detection: A significant benefit of the NAMUR standard is its ability to indicate sensor or wiring faults. A current reading close to 0 mA might indicate a broken wire or sensor failure, while a current reading around the nominal supply current (often 8mA) suggests a short circuit. This inherent diagnostics capability significantly enhances system reliability and safety.
- Fail-Safe Design Philosophy: Many NAMUR sensors are designed with fail-safe principles. For instance, a sensor monitoring a clamp position might be designed to generate a “safe-state” signal (like “clamp closed”) even if its power fails, triggering an alarm or shutdown.
Key Advantages Driving Adoption
The NAMUR inductive sensor offers compelling benefits in challenging environments:
- Intrinsic Safety: This is the paramount benefit, enabling safe operation in Zone 0/1 (gas/vapor) or Zone 20⁄21 (dust) hazardous areas classified under ATEX (EU) and IECEx (International) directives. They are fundamental for compliance.
- Enhanced Diagnostic Capability: The defined current ranges allow monitoring systems to easily distinguish between normal operation (target present/absent), damaged wiring (open/short circuits), and sensor failure, leading to proactive maintenance.
- Simplified System Diagnostics: Faults are easily detected by measuring loop current, simplifying troubleshooting compared to voltage-switching sensors.
- Reduced Wiring Costs: Often, multiple NAMUR sensors can share a single multi-channel barrier/isolation amplifier located in the safe area, reducing cabling costs.
- Robustness: They inherit the inherent durability of standard inductive proximity sensors – resistance to vibration, shock, dust, dirt, and moisture (often rated IP67/IP68/IP69K).
Where Are NAMUR Inductive Sensors Crucial?
You’ll find these sensors as indispensable components in industries where flammable substances are handled:
- Oil & Gas: Refineries, offshore platforms, pipelines, tank farms monitoring valves, hatches, pump states, and level limits.
- Chemical & Pharmaceutical: Reactors, mixers, filling lines, spray dryers monitoring position, movement, and end-of-stroke.
- Paints & Coatings: Monitoring mixer blades, agitators, and conveyor positions in areas with solvent vapors.
- Mining: Monitoring equipment positions and conveyor systems where combustible dust is prevalent.
- Grain & Food Processing: Silos, mills, elevators, and packaging lines where fine combustible dust (like flour or sugar) poses an explosion risk.
- Wastewater Treatment: Monitoring equipment like rakes and aerators in potentially methane-rich environments.
Choosing and Implementing NAMUR Sensors
Consider these factors:
- Application: Define exactly what you need to detect (metal type, target size) and the required sensing range.
- Hazardous Area Classification: Precisely identify the Zone (0,1,2 for gas; 20,21,22 for dust) and the required ATEX/IECEx Certification (e.g., Ex ia IIC T6 Ga).
- Compatible Barrier/Isolator: Always select an approved, certified barrier or isolator matched to the sensor’s requirements and the hazardous area classification. Ensure correct configuration.
- Sensor Specifications: Choose the correct housing material (stainless steel is common), size, connection type (M12, M8, M18, Cable), temperature rating, and IP rating for the environment.
- Fail-Safe Requirement: Determine if the application necessitates a fail-safe design.
Conclusion: The Non-Negotiable Safety Sentinel
More than just a metal detector, the NAMUR inductive sensor is an engineered safety solution. Its intrinsically safe design, mandated by the NAMUR standard, provides a fundamental layer of protection in industries where explosive atmospheres are a constant threat. By enabling reliable equipment monitoring while eliminating ignition sources, offering critical diagnostics, and simplifying compliance with ATEX and IECEx regulations, these sensors are indispensable guardians. Understanding their