wireless inductive sensor
- time:2025-07-07 15:24:17
- Click:0
Wireless Inductive Sensors: The Silent Guardians of Industrial Automation
Imagine a high-speed manufacturing line. Robotic arms weld with millimetre precision, conveyor belts zip components into place, and massive presses stamp out parts. Beneath this orchestrated chaos, unseen sentinels work tirelessly. These are wireless inductive sensors, fundamental yet often overlooked components ensuring everything runs smoothly, safely, and efficiently. They are the invisible backbone of modern industrial automation, enabling seamless operation without the constraints of physical wiring.
Demystifying the Wireless Inductive Sensor
At its core, this technology merges two powerful concepts:
- The Inductive Principle: Rooted in Faraday’s Law of Electromagnetic Induction, an inductive sensor generates a high-frequency electromagnetic field from its sensing face. When a conductive metal target (like steel, iron, aluminum, copper, brass) enters this field, it induces tiny circulating electrical currents called eddy currents within the target. These eddy currents draw energy from the sensor’s field, causing a measurable change in the sensor’s internal oscillator. This change triggers the sensor’s output switch (e.g., switching “ON” or “OFF”).
- Wireless Communication: Instead of sending this switched signal through a traditional physical cable back to a controller (like a PLC - Programmable Logic Controller), the sensor incorporates a radio transceiver. It transmits the state change wirelessly – typically using robust, industrial-grade protocols like IO-Link Wireless, Bluetooth Low Energy (BLE), or proprietary ISM band (like 2.4 GHz) radios – to a nearby gateway or receiver module connected to the control system. This gateway acts as the bridge between the wireless sensor network and the wired control backbone.
The result is a device capable of contactless, wear-free proximity detection of metallic objects without the need for physical wiring connections for data transmission and, crucially, often without needing wires for power either.
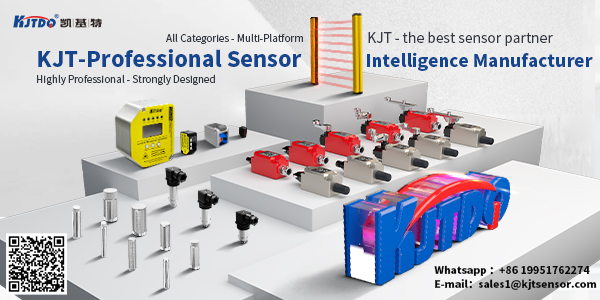
Why Wireless & Inductive? The Compelling Advantages
Combining inductive sensing with wireless communication unlocks significant benefits that address common challenges in industrial settings:
- Elimination of Wiring Costs & Complexity: This is the most immediate and impactful advantage. Running cables, especially in large facilities or over long distances, is expensive (material, conduit, labor) and time-consuming. Installation becomes dramatically faster and cheaper. Retrofitting sensors onto existing machinery also becomes vastly simpler.
- Enhanced Flexibility & Scalability: Need to add a sensor to monitor a new bottleneck? Adjust the position of a sensor for a product changeover? With wireless sensors, repositioning or adding new units is straightforward. The network scales easily without massive rewiring projects.
- Simplified Maintenance: Damaged sensor cables are a common failure point, often requiring costly downtime to trace and repair. Wireless sensors remove this vulnerability. Additionally, diagnostics data (like signal strength, battery level, temperature) can often be transmitted alongside the switch signal, enabling predictive maintenance.
- Operation in Challenging Environments: Inductive sensors are inherently robust. Their non-contact principle means no mechanical wear. They are resistant to dirt, dust, oil, moisture, vibrations, and extreme temperatures. Wireless connectivity further enhances this by removing the cable entry point, a common ingress point for contaminants. This makes them ideal for:
- Machine Tools: Detecting tool position, tool breakage, part presence in coolant-filled environments.
- Material Handling & Logistics: Monitoring pallet presence, cylinder position on automated guided vehicles (AGVs), package counting on conveyors.
- Automotive Assembly: Verifying part seating, robot end-of-arm tooling position, safety interlocking.
- Heavy Machinery: Position feedback on hydraulic/pneumatic cylinders, monitoring moving parts on construction/mining equipment.
- Mobility Enabled: Wireless inductive sensors are perfect for monitoring moving parts where dragging cables is impractical or prone to failure – think rotary tables, robotic end effectors, automated doors, and crane controls.
- Battery-Free Operation (Often): A key innovation in many modern wireless inductive sensors is energy harvesting. The same electromagnetic field used for sensing can often be used to power the sensor’s electronics and wireless transmitter. Alternatively, some sensors might utilize long-life batteries or even small solar cells. This self-powered capability is a major advantage, removing the hassle of battery replacement or wired power supplies.
Real-World Applications: Where the Magic Happens
The combination of robust non-contact detection and wireless freedom opens doors across numerous sectors:
- Machine Tool Monitoring: Detecting broken drills or end mills instantly by sensing the absence of the tool tip upon retraction, preventing costly damage and scrap. Confirming workpiece clamping before machining starts. Zero physical contact is crucial in this harsh environment.
- Automated Guided Vehicle (AGV) Systems: Ensuring lift mechanisms are fully raised/lowered before movement. Detecting load presence on forks. Monitoring safety sensor status without complex cabling that restricts movement.
- Packaging Machinery: Detecting foil seals on containers, verifying lid closure, counting metallic components. Wireless allows easy reconfiguration for different packaging formats.
- Rotary Equipment: Monitoring gear teeth, detecting position of rotating cams or shafts on indexing tables – locations where slip rings or cables would be unreliable.
- Mobile Machinery (Construction, Agriculture): Position feedback on hydraulic cylinders (boom, bucket, implement position) on excavators, tractors, and harvesters. Wireless eliminates cable damage from constant flexing and harsh terrain.
- Process Control Valves: Verifying open/closed states on metallic valves in remote or hard-to-reach locations (e.g., pipelines, tank farms). Wireless simplifies installation drastically.
The Future is Wireless and Smart
The evolution of wireless inductive sensors is ongoing. We are seeing trends towards:
- Integration with IIoT (Industrial IoT): Sensors becoming data points within larger IIoT ecosystems. Transmitting not just binary state, but detailed diagnostics and process parameters.
- Enhanced Communication Protocols: Wider adoption of standardized wireless protocols like IO-Link Wireless ensures interoperability between vendors and future-proofs investments.
- Advanced Energy Harvesting: More efficient harvesting techniques enabling smaller sensors and operation in lower-energy detection scenarios.
- Smarter Sensors: Incorporation of edge computing capabilities for local processing (e.g., simple counting, filtering) before transmission, optimizing network bandwidth.
- AI & Predictive Analytics Integration: Sensor data feeding AI algorithms to predict equipment failures or optimize process parameters based on detection patterns.
From sensing metal parts on a high-speed conveyor to ensuring the precise position of a massive hydraulic arm deep in a mine, wireless inductive sensors provide the essential link between the physical world and the digital control systems driving modern industry. Their unique blend of robust contactless sensing, wireless freedom, and potential for battery-free operation makes them not just a convenient alternative to wired sensors, but often the enabling technology for smarter, more flexible, and cost-effective automation solutions. They truly are the silent guardians, working unseen to keep the wheels of industry turning.