cnc proximity sensor
- time:2025-07-07 11:38:58
- Click:0
The Unsung Heroes of Precision Machining: How CNC Proximity Sensors Keep Your Shop Running Smoothly
Imagine a high-speed CNC machining center, whirring with almost invisible precision, carving intricate components from solid metal. Now, picture the catastrophic results if a misaligned tool crashes into the workpiece, or a critical component isn’t detected in its correct position. Preventing such expensive and dangerous scenarios relies heavily on one often-overlooked component: the CNC proximity sensor. These silent sentinels, working tirelessly behind the scenes, are fundamental to modern manufacturing’s accuracy, safety, and efficiency. They are the eyes and touchless fingers of the automated world, ensuring everything is precisely where it needs to be.
What Exactly is a CNC Proximity Sensor?
At its core, a CNC proximity sensor is a non-contact electronic device designed to detect the presence or absence of a metallic (and sometimes non-metallic) target within a specific range without physical contact. Installed at critical points on CNC machines – like tool changers, axis limits, part presence stations, pallet changers, or coolant guards – they send signals back to the CNC controller. This feedback is vital for the machine’s logic, dictating the next step in the machining process, triggering safety halts, confirming tool engagement, or verifying workpiece positioning. Unlike mechanical limit switches, they have no moving parts to wear out, offering superior longevity and reliability in the demanding environment of a machine shop.
The Magic Behind the Detection: Eddy Currents and Fields
The most common type used for metal detection in CNC environments is the inductive proximity sensor. Here’s a simplified look at how they work:
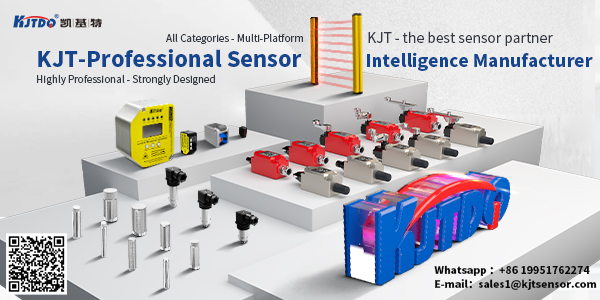
- Generating the Field: An internal oscillator generates a high-frequency electromagnetic field that radiates from the sensor’s face.
- Target Interaction: When a conductive metallic target (like a tool holder, pallet, or machine slide) enters this field, it induces small swirling electrical currents within the target itself, known as eddy currents.
- Field Dampening: These eddy currents draw energy from the sensor’s oscillator field, effectively dampening or reducing the amplitude of the oscillations.
- Signal Change Detection: An internal circuit continuously monitors the strength of the oscillator. As the target approaches and the oscillation amplitude drops below a certain threshold…
- Output Switching: …the sensor’s output state changes. This typically means switching a solid-state transistor output from “OFF” to “ON” (or vice-versa), sending a clear electrical signal to the CNC controller that a target is present within its sensing range.
For detecting non-metallic materials like plastics, wood, or liquids, capacitive proximity sensors are employed. These work by detecting changes in capacitance caused by the target material entering the sensor’s electrostatic field, altering the oscillator’s state.
Why CNC Proximity Sensors Are Indispensable
The advantages they bring to CNC operations are compelling:
- Non-Contact Operation: This is paramount. No physical wear means dramatically reduced maintenance, no mechanical failure from repeated impacts, and no damage to delicate targets or the sensor itself. This translates directly to reduced downtime and lower operating costs.
- High Reliability & Long Life: With no moving parts susceptible to wear and tear from contact or vibration, and robust housings often rated to high IP standards (like IP67) for dust and coolant resistance, they offer exceptional long-term reliability.
- High-Speed Operation: Capable of detecting targets at extremely high frequencies (thousands of times per second), they are perfectly suited for the rapid movements and decision-making cycles of modern CNC machines. This enables fast cycle times and high throughput.
- Environmental Resilience: Modern sensors are designed to withstand the harsh realities of machining: oil, coolant mist, metallic chips, vibration, and extreme temperature fluctuations. Their sealed construction protects their sensitive electronics.
- Repeatability & Precision: They provide incredibly consistent and repeatable switching points. This repeatability, often down to microns, is critical for achieving machining precision and ensuring consistent part quality.
- Safety: Crucial for personnel protection (e.g., guarding interlocks) and preventing catastrophic machine damage due to collisions or unexpected movements. They are the first line of defense against expensive crashes.
Key Applications on Your CNC Machine
Look around any CNC machining center, and you’ll find proximity sensors performing critical roles:
- Tool Setting and Breakage Detection: Sensors verify that a tool is correctly seated in the spindle before machining begins. More sophisticated systems can even detect broken tools by sensing the tool tip’s absence or position during a probe cycle.
- Part Presence/Absence Verification: Ensuring a blank is correctly loaded onto a fixture or pallet before starting the machining cycle is vital. Sensors confirm the workpiece is present and seated.
- Position Verification: Confirming the precise location of machine slides (X, Y, Z axes), rotary tables, pallet changers, or tool carousel positions. This ensures movements start from known, accurate points.
- Axis Limit / Travel Detection: Providing end-of-travel signals to prevent mechanical overtravel damage to ball screws, linear guides, or other components. This is a fundamental safety function.
- Door Interlocks & Safety Guarding: Integrating with safety circuits to ensure doors or guards are closed before dangerous machine movements can commence, protecting operators.
- Coolant Level Monitoring: Capacitive sensors can detect coolant levels in tanks, preventing pump damage due to dry running.
Choosing the Right CNC Proximity Sensor: Key Considerations
Selecting the optimal sensor for a specific CNC application involves several factors:
- Sensing Distance: What is the required distance at which the sensor needs to reliably detect the target? Ensure the nominal sensing range suits the installation gap. Remember factors like target material and size affect the effective range.
- Target Material: Is the target ferrous metal (best for inductive), non-ferrous metal, or non-metallic (requiring capacitive)? Sensor choice hinges on this.
- Output Type: Does the CNC controller require a PNP (sourcing) or NPN (sinking) DC signal? Matching the output type to the controller’s input is critical.
- Environmental Conditions: Consider exposure to cutting fluids (water or oil-based?), washdown potential, temperature extremes, metallic dust, chips, and vibration levels. Choose the appropriate housing material (stainless steel often preferred) and IP rating.
- Housing Size & Shape: Sensors come in cylindrical (threaded barrel), rectangular block, or specialized shapes. Ensure it fits the available mounting space and can be positioned correctly relative to the target.
- Connection Type: Pre-wired cables, quick-disconnect connectors (M8, M12), or terminal blocks? Choose based on ease of installation and maintenance needs.
Maintenance: Simple but Essential
While famed for their reliability, even CNC proximity sensors need basic care:
- Keep Them Clean: Regularly wipe the sensing face with a clean, non-abrasive cloth to remove accumulated oil, coolant residue, or metal chips that can dampen the sensing field and reduce range.
- Ensure Secure Mounting: Check that vibration hasn’t loosened mounting bolts, potentially changing the critical gap between the sensor and its target.
- Inspect Wiring: Look for abrasions, coolant ingress at connection points, or damage from moving machine parts. Secure loose cables.
- Verify Function: Periodically trigger the sensor manually (using the target material) and confirm the machine controller registers the state change correctly during setup or routine checks.
From preventing multi-thousand-dollar crashes to guaranteeing machined parts meet exacting tolerances, CNC proximity sensors are fundamental enablers of modern manufacturing excellence. Their non-contact