square proximity sensor
- time:2025-07-06 03:06:58
- Click:0
The Geometry of Detection: Unpacking the Purpose and Power of Square Proximity Sensors
Why choose a square proximity sensor over the ubiquitous circular design? In the intricate dance of automation and machine safety, where space is often at a premium and precision is non-negotiable, the distinctive square proximity sensor emerges as a specialized solution. Far from being a mere aesthetic choice, this specific geometry addresses unique engineering challenges, offering advantages that make it indispensable in certain applications. Let’s delve into the world of proximity sensing and uncover the rationale behind the square form factor.
Proximity Sensor Fundamentals: Sensing Without Touch
First, a quick recap. Inductive proximity sensors detect the presence or absence of metallic objects using an electromagnetic field generated by a coil. Capacitive proximity sensors, conversely, detect both metallic and non-metallic materials (like liquids, plastics, or wood) by sensing changes in capacitance. The core principle remains the same: non-contact detection enabling automation, counting, position verification, and safety interlocks without physical wear. These proximity sensors are the unseen sentinels in countless industrial machines, consumer electronics, and automotive systems.
The Circular Standard and Its Limitations
The vast majority of inductive proximity sensors and many capacitive proximity sensors feature a cylindrical housing. This shape is inherently strong, easily manufacturable, ideal for omnidirectional sensing fields, and simple to mount through a round hole. It’s the logical default. However, this circular form factor faces limitations in specific scenarios:
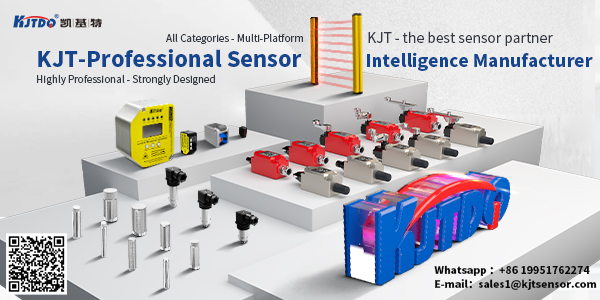
- Tight Spatial Constraints: When mounting space is extremely restricted, particularly in corners or alongside flat surfaces like metal frames or circuit boards, the curved edges of a cylinder can lead to unused space or necessitate larger clearances than desired. A flat-sided sensor can tuck neatly into corners.
- Mounting Surface Compatibility: Integrating sensors directly onto printed circuit boards (PCBs) is common. Square proximity sensors, especially surface-mount device (SMD) variants, are inherently more compatible with PCB panelization and automated assembly processes designed for rectangular components.
- Alignment and Sensing Field Control: While circular sensors typically have a symmetrical sensing field, a square proximity sensor can offer specific advantages depending on its internal design. While often designed for front-facing sensing like round counterparts, the flat sides can sometimes facilitate closer mounting to reference surfaces or influence the field shape near the edges slightly differently.
Enter the Square Proximity Sensor: Solving Spatial Challenges
The square proximity sensor is engineered precisely to mitigate the limitations of its circular counterparts in constrained environments. Its primary strengths lie in form factor optimization:
- Optimized Space Utilization: The flat sides and sharp corners allow a square proximity sensor to fit snugly against adjacent components, machine frames, or into the very corner of an enclosure. This maximizes usable space within densely packed assemblies, like control panels, robotic arms, or miniaturized electronic devices. Efficient packing is critical in modern, compact designs.
- Seamless PCB Integration: Square proximity sensors, particularly SMD types, are the preferred choice for direct mounting onto PCBs. Their rectangular footprint aligns perfectly with standard PCB layouts, solder pads, and automated pick-and-place machinery. This streamlines manufacturing, reduces assembly complexity, and enhances reliability in electronic assemblies. Proximity sensor integration becomes far simpler.
- Stable Mounting: The flat surfaces provide excellent stability when mounted flush against another flat reference surface, reducing vibration or potential misalignment issues compared to a potentially rounded or threaded circular housing edge.
Diverse Industrial Applications for Square Proximity Sensors
Where does this niche geometry shine? Look for them in environments demanding compactness and tight integration:
- Miniature Machinery & Robotics: Inside small robotic arms, automated test equipment, or compact assembly machines where every cubic millimeter counts, square proximity sensors provide reliable position feedback without consuming excessive space.
- Integrated Control Systems: Within PLC panels, motor drives, and power supplies, these sensors are frequently used for detecting cabinet door positions (safety interlocks), component presence on internal slides, or cooling fan operation – all areas where low-profile mounting is essential.
- High-Density Electronics: Consumer electronics, telecommunications equipment, and automotive control units utilize square proximity sensors (often capacitive) for functions like detecting device covers, battery presence, or liquid levels in reservoirs, leveraging their PCB-friendly design.
- Conveyor Systems with Tight Layouts: Alongside conveyors in confined spaces, especially where guide rails or structural supports are close, square sensors can be mounted where round ones might not fit optimally.
Square vs. Round: Performance Nuances
It’s crucial to note that while the form factor is different, the core sensing technology (inductive or capacitive) remains fundamentally the same. The square shape itself doesn’t inherently alter the basic sensing principle or range dramatically compared to an equivalent circular sensor with the same sensing face dimensions. Key performance characteristics like sensing distance, repeatability, and environmental ratings (IP67, etc.) are primarily determined by the internal coil/capacitor design and housing material, not the overall external shape. The choice almost always boils down to mounting constraints and integration requirements, not a fundamental difference in sensing capability.
Selecting the Right Sensor
Choosing between a square proximity sensor and a traditional circular one involves careful consideration:
- Mounting Space: Is there a critical spatial limitation where flat sides and sharp corners offer a significant fit advantage?
- Mounting Method: Will the sensor be panel-mounted in a tight spot, or is it destined for direct PCB assembly?
- Sensing Technology: Does the application require detecting metal (inductive) or various materials (capacitive)? Both types are available in square formats.
- Sensing Range & Specifications: Ensure the chosen proximity sensor meets the required electrical characteristics (e.g., NPN/PNP, NO/NC), operating voltage, and sensing distance for the target object.
Conclusion: A Geometric Solution for Practical Problems
The square proximity sensor stands as a testament to pragmatic engineering. It doesn’t seek to replace the versatile circular sensor but rather complements it by solving specific spatial and integration puzzles. When the design demands a sensor that can hug corners, integrate flawlessly onto PCBs, or occupy an absolute minimum footprint without compromising the core function of reliable non-contact detection, the square form factor proves its indispensable worth. In the relentless pursuit of miniaturization and efficient manufacturing, this geometric outlier proves that sometimes, thinking outside the circle is the most effective approach.