proximity sensor types
- time:2025-07-06 02:48:51
- Click:0
Demystifying Proximity Sensor Types: Your Guide to Non-Contact Detection
Imagine unlocking your smartphone without touching the screen, your car automatically shifting gears, or factory machines stopping before a collision. These everyday marvels are silently powered by proximity sensors, the unsung heroes detecting objects without physical contact. Understanding the diverse proximity sensor types available is crucial for engineers, designers, and tech enthusiasts alike. Whether optimizing an assembly line or building the next smart device, choosing the right sensor hinges on grasping the fundamental principles and key differences among them. Let’s dive into the fascinating world of proximity sensing technology.
What Exactly is a Proximity Sensor?
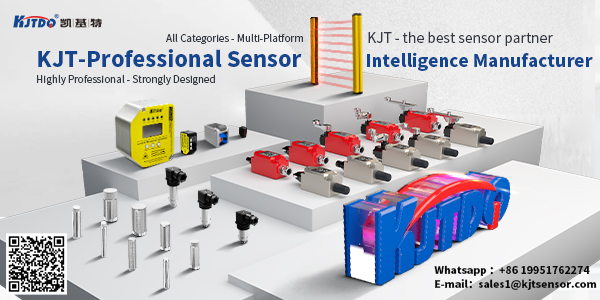
At its core, a proximity sensor is a device that detects the presence or absence of an object (often called the “target”) within a specific range without requiring physical contact. These sensors output a signal – typically a simple ON/OFF switch or a more complex analog value – indicating the target’s status. Their non-contact nature makes them ideal for applications demanding reliability, long service life (no moving parts wear out), and operation in harsh environments (dirt, moisture, extreme temperatures) where physical switches would fail. They form the backbone of position sensing, object counting, speed detection, and safety interlocking across countless industries.
Unveiling the Major Proximity Sensor Types
Several distinct technologies underpin proximity sensing. Each operates on a unique physical principle, leading to specific strengths, limitations, and ideal use cases. Here’s a breakdown of the most prevalent types:
- Inductive Proximity Sensors
- Principle: Detect ferromagnetic metals (like iron and steel). They generate an oscillating electromagnetic field from a coil. When a conductive metal target enters this field, eddy currents are induced within the target, causing a measurable change in the sensor’s oscillation amplitude or frequency.
- Strengths:
- Highly robust and reliable, often with IP67 or IP68 ratings.
- Excellent immunity to dirt, dust, oils, and moisture.
- Capable of high-speed switching.
- Generally unaffected by non-metallic objects between the sensor and target.
- Limitations: Only detect metals (primarily ferrous). Sensing range is relatively short and varies significantly depending on the target metal type and size (e.g., smaller sensing range for non-ferrous metals like aluminium).
- Typical Applications: Machine tooling, position sensing in automotive assembly, metal object detection on conveyor belts, gear tooth counting, cylinder position sensing.
- Capacitive Proximity Sensors
- Principle: Detect any object that has a different dielectric constant than air (which includes almost all materials: metals, plastics, wood, liquids, powders, glass, etc.). They function like an open capacitor. The sensor forms one plate, the target (or ground) forms the other. The approach of the target changes the capacitance within the sensor’s circuit, triggering detection.
- Strengths:
- Detect virtually any material, solid or liquid.
- Can often sense targets through non-metallic container walls (e.g., detecting liquid level inside a plastic tank).
- Useful for applications involving non-conductive materials where inductive sensors fail.
- Limitations: More susceptible to environmental interference than inductive sensors (e.g., humidity changes, dust composition). Sensing range can be influenced by the target material’s properties. Generally have a shorter range than inductive sensors for metallic targets. May require careful calibration for specific materials.
- Typical Applications: Liquid level detection, bulk material level sensing (grains, powders), presence detection of plastic objects, product counting (all materials), touch interfaces (indirectly).
- Ultrasonic Proximity Sensors
- Principle: Use sound waves beyond human hearing (typically 20 kHz to several hundred kHz). They emit ultrasonic pulses and measure the time-of-flight (TOF) for the echo to return after bouncing off a target. Distance is calculated based on the speed of sound.
- Strengths:
- Longer effective sensing ranges compared to inductive or capacitive sensors.
- Can detect various materials (solids, liquids, granular) regardless of color, transparency, or surface texture.
- Effective in challenging environments like smoke, fog, or dust where optical sensors struggle.
- Provide distance measurement, not just presence/absence.
- Limitations: Performance can be affected by temperature and pressure changes (which alter the speed of sound). Soft, sound-absorbing materials (like cloth) or angled surfaces may reflect poorly. Ambient noise at ultrasonic frequencies can cause interference. Slower response times compared to inductive/capacitive sensors.
- Typical Applications: Parking assistance systems, object profiling/level measurement in tanks, pallet detection in logistics, presence detection in automated guided vehicles (AGVs), loop control (e.g., detecting gaps on conveyor belts).
- Optical Proximity Sensors (Photoelectric)
- Principle: Utilize light (visible, infrared, or laser) to detect objects. Common configurations include:
- Through-beam: Separate emitter and receiver; detection occurs when the target breaks the light beam.
- Retro-reflective: Emitter and receiver in one housing; uses a reflector; detection when target blocks the beam.
- Diffuse (Proximity Mode): Emitter and receiver in one housing; detects light reflected directly off the target.
- Strengths:
- Very long sensing ranges possible, especially with laser or focused optics.
- Capable of detecting very small objects.
- Fast response times.
- Allows for precise positioning.
- Limitations: Performance highly dependent on target surface properties (color, reflectivity). Ambient light interference can be a problem (especially sunlight). Dirt, dust, fog, or steam can obstruct the light path and cause false readings. Requires proper alignment (especially through-beam and retro-reflective).
- Typical Applications: Object counting, web break detection, bottle/can presence on filling lines, label detection, security systems (light barriers), elevator door safety.
- Magnetic Proximity Sensors (Reed Switches / Hall Effect)
- Principle:
- Reed Switches: Contain two ferromagnetic reeds sealed in a glass tube. A strong enough magnetic field causes the reeds to flex and make contact, closing the circuit.
- Hall Effect Sensors: Semiconductor devices that generate an output voltage proportional to the strength of an applied magnetic field perpendicular to the current flow. This voltage change indicates proximity.
- Strengths:
- Very low power consumption (especially Hall Effect).
- Can operate through non-magnetic barriers (like plastic, aluminum, stainless steel).
- Reed switches offer simple, contact-based switching. Hall Effect sensors provide solid-state reliability and can output analog signals or digital pulses.
- Limitations: Require a magnet as the target or attached to the moving part being sensed. Sensing range is typically very short. Reed switches have mechanical contacts subject to wear and limited switching speed compared to solid-state sensors. External magnetic fields can interfere.
- Typical Applications: **Door/w