m12 inductive proximity sensor
- time:2025-07-06 00:42:15
- Click:0
M12 Inductive Proximity Sensors: The Compact Powerhouses of Industrial Sensing
Imagine a factory floor buzzing with robotic arms, conveyor belts whirring, and machinery humming – a symphony of modern automation. At the heart of this intricate dance, ensuring precision, safety, and efficiency, lies an often-overlooked hero: the inductive proximity sensor. And among these vital components, the M12 inductive proximity sensor stands out as a workhorse, beloved for its compact size, ruggedness, and unwavering reliability in detecting metallic objects without physical contact. Understanding what makes this specific form factor so indispensable is key to appreciating its dominance across countless industries.
The Essence of Contactless Detection: How M12 Inductive Sensors Work
At their core, M12 inductive proximity sensors operate on a fundamental principle of electromagnetism. Inside the sensor’s housing (defined by the standardized M12 threaded barrel, approximately 12mm in diameter), lies an oscillator circuit generating a high-frequency electromagnetic field. This field radiates outward from the active sensing face. When a ferrous (iron-based) or non-ferrous (like aluminum, brass, copper) metal object enters this field, Eddy currents are induced within the target material. These eddy currents draw energy from the oscillator, causing its amplitude to decrease.
An integrated evaluation circuit within the M12 sensor continuously monitors the oscillator’s strength. The precise moment this amplitude drops below a preset threshold triggers a switching action. This change in the sensor’s output state (typically switching from OFF to ON, or vice-versa, depending on configuration) is the signal sent to the machine’s control system – indicating the presence or absence of the target object. This entire process happens in microseconds and without any physical touch, enabling high-speed detection and eliminating wear and tear associated with mechanical switches. It’s pure electromagnetic interaction at work.
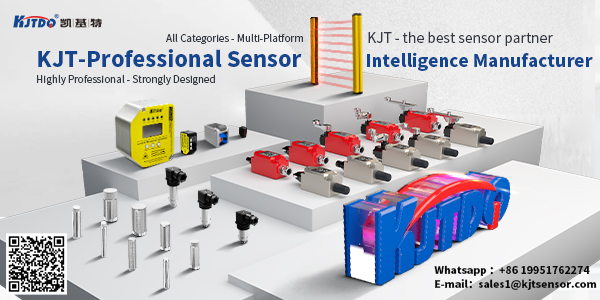
Why M12? The Advantages of a Standardized Powerhouse
The M12 form factor isn’t arbitrary; its widespread adoption is driven by compelling advantages:
- Compact Size & Space Efficiency: In densely packed machinery and complex automation cells, space is premium. The small M12 diameter allows these sensors to fit into tight locations where larger sensors simply couldn’t operate, enabling sophisticated sensing capabilities in constrained spaces.
- Standardization & Versatility: The M12 threaded barrel is a globally recognized standard (often referred to as IEC 60947-5-2). This simplifies installation with corresponding M12 nuts or mounting brackets, streamlines sensor replacement, and ensures compatibility with a vast ecosystem of M12 connectors and cables. This standardization significantly reduces procurement and maintenance complexity.
- Robust Construction & Environmental Durability: Designed for the rigors of industrial environments, M12 inductive proximity sensors typically feature robust housings made from materials like nickel-plated brass or stainless steel. They boast high Ingress Protection (IP) ratings (commonly IP67, IP68, or even IP69K), making them resistant to dust, oil, coolants, washdowns, and even temporary immersion. They can withstand significant shock and vibration.
- Reliable Performance: Shielded designs are predominant, allowing for flush mounting where the sensor face can be embedded in metal without false triggering from the surrounding material. They offer consistent switching distances (ranging typically from 1mm to 4mm for steel targets, depending on the specific model and factor correction for different metals), ensuring dependable object detection cycle after cycle. Advanced models feature short-circuit and reverse polarity protection, enhancing system resilience.
- Broad Application Suitability: The combination of size, durability, and sensing capability makes the M12 inductive sensor incredibly versatile. It comes in various output configurations (NPN, PNP, NO, NC), voltage ranges (commonly 10-30V DC), and connection types (cable or connector variants).
Where M12 Inductive Sensors Shine: Critical Applications
The reliability and compactness of the M12 inductive proximity sensor make them ubiquitous across industrial automation:
- Position Sensing: Verifying the end position of cylinders, slides, clamps, and actuators. Confirming presence/absence of parts on pallets, fixtures, or conveyors.
- Object Counting: Accurately tracking metallic parts moving along a production line or through a process.
- Speed Monitoring: Detecting teeth on gears or markers on rotating shafts to calculate rotational speed. Crucial for motor and conveyor control.
- Liquid Level Control: Detecting the presence of metallic floats within tanks.
- Machine Safety: Implementing presence detection for guarding or interlock systems where metallic components indicate safe/unsafe conditions.
- End-of-Travel Detection: Signaling when a moving mechanism has reached its limit, preventing damage.
- Material Handling: Widely used in packaging, filling, assembly lines, robotic work cells, and CNC machines. Their resilience makes them suitable for harsh environments like automotive manufacturing, food & beverage processing (with appropriate food-grade housing options), and heavy machinery.
Key Considerations When Selecting M12 Inductive Sensors
Choosing the right M12 inductive proximity sensor involves more than just the M12 thread. Key factors include:
- Sensing Distance: The nominal sensing range specified for a standard steel target (usually 2mm, 4mm, or 8mm variants are common within M12). Remember the correction factor required for non-ferrous metals (e.g., aluminum typically requires ~50% of the stated steel sensing distance).
- Target Material: Is the primary target ferrous steel, stainless steel, aluminum, brass, or copper? This significantly impacts achievable sensing distance.
- Shielded vs. Unshielded: Shielded sensors allow for flush mounting in metal. Unshielded sensors offer longer sensing ranges but require an annular non-metallic space around the sensing face.
- Output Type: NPN (sinking) or PNP (sourcing)? Normally Open (NO) or Normally Closed (NC)? Must match the input requirements of your PLC or controller.
- Housing Material: Brass (common, cost-effective), stainless steel (for high corrosion resistance, washdown, chemical exposure), or specialized plastics.
- IP Rating: Ensure the rating (e.g., IP67, IP68, IP69K) meets the environmental demands (dust, moisture, high-pressure cleaning).
- Operating Voltage: Standard DC versions cover 10-30V DC, but confirm compatibility.
- Connection: Pre-cabled lengths and styles, or connector versions (requiring a separate M12 cable assembly).
The Unseen Engine of Precision: M12 in the Automation Ecosystem
From ensuring a robotic arm grips a part correctly to confirming a safety gate is closed before a press activates, the M12 inductive proximity sensor performs millions of critical detection tasks daily. Its compact M12 size, standardized interface, inherent ruggedness, and reliable non-contact operation have cemented its position as a fundamental building block of modern industrial control systems. While advancements in sensing technology continue, the core principles and practical benefits offered by these miniature powerhouses ensure the M12 inductive proximity sensor will remain an indispensable component on the