capacitance distance sensor
- time:2025-07-05 03:06:54
- Click:0
Decoding Distance: How Capacitance Sensors Measure Without Touching
Have you ever wondered how your smartphone screen instantly responds to a light tap, or how sophisticated machinery precisely positions components without making contact? Often invisible yet incredibly powerful, capacitance distance sensors are the unseen workhorses enabling these feats. These remarkable devices offer non-contact distance and proximity sensing, revolutionizing measurement across countless applications by leveraging the fundamental physics of capacitance.
Understanding the Core Principle: It’s All About Capacitance
At its heart, a capacitance sensor measures distance by detecting changes in an electrical property called capacitance. Capacitance describes an object’s ability to store electrical charge. A basic capacitor consists of two conductive plates separated by an insulating material (dielectric). The capacitance (C) depends on three factors:
- Plate Area (A): Larger plates mean more capacitance.
- Distance Between Plates (d): Smaller distances mean higher capacitance.
- Dielectric Constant (ε) of the Material Between Plates: Materials with higher ε increase capacitance.
A capacitance distance sensor cleverly utilizes this relationship, particularly the dependence on distance. The sensor itself acts as one “plate” of a capacitor. The target object – whatever you’re measuring the distance to – acts as the other plate (or alters the sensor’s electric field significantly), with the air gap or other material in between acting as the dielectric.
Here’s How a Capacitance Proximity Sensor Operates:
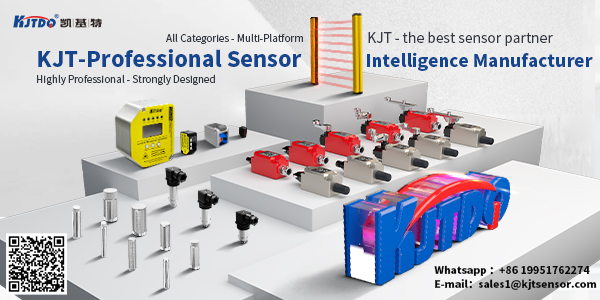
- Generating an Electric Field: The sensor’s active electrode is energized with an oscillating electrical signal, creating an electrostatic field that projects outwards.
- Target Interaction: When a conductive or dielectric target object enters this field, it disturbs the field lines.
- Capacitance Shift: This disturbance causes a detectable change in the capacitance between the sensor electrode and the target.
- Measuring the Change: Sophisticated electronics within the sensor precisely measure this capacitance shift.
- Distance Output: The measured capacitance change is directly correlated to the distance between the sensor and the target object. This distance information is then converted into an electrical signal (e.g., analog voltage, current, or digital output) for the system to use.
Crucially, the magnitude of the capacitance change is inversely proportional to the distance. As the target gets closer, capacitance increases significantly.
Where Capacitance Sensing Shines: Key Applications
The unique characteristics of capacitive distance measurement make it indispensable in diverse fields:
- Industrial Automation & Robotics: Precise positioning of parts, end-of-arm tooling, fill level detection in non-metallic tanks (liquids, plastics, granules), part presence/absence verification, robotic guidance, and wafer handling in semiconductor manufacturing rely heavily on capacitive proximity sensors.
- Consumer Electronics: Touchscreens (sensing finger proximity without pressure), touch-sensitive buttons, and trackpads are ubiquitous applications. Capacitive displacement sensors also ensure proper lid closure on laptops/tablets.
- Automotive: Monitoring fluid levels (brake fluid, washer fluid, coolant), detecting seat occupancy for airbag systems, and controlling touch interfaces within the cabin.
- Medical Devices: Used in breath analyzers, contactless switches on sensitive equipment, and certain types of flow meters. Their non-contact nature is ideal for sterile environments.
- Precision Engineering & Metrology: High-resolution capacitive displacement sensors measure micro-scale vibrations, runout, flatness, and thickness in manufacturing and quality control labs, offering nanometer-level resolution.
- Building Automation & Security: Tamper detection (approach to sensitive panels), touchless faucets and flushers, and occupancy sensing.
The Distinct Advantages of Capacitance Distance Sensing
Why choose a capacitive approach over other methods like ultrasonic, inductive, or optical? Key benefits include:
- True Non-Contact Measurement: No physical touch means zero mechanical wear on the sensor or target, ensuring long sensor life. It eliminates the risk of damaging delicate targets.
- Material Versatility: Can detect conductive targets (metals) and many non-conductive materials (plastics, glass, wood, liquids, ceramics) based on their dielectric constant. This makes them far more versatile than inductive sensors, which only detect metals.
- High Sensitivity and Resolution: Capable of detecting minute distance changes, especially at close ranges. High-end sensors achieve sub-nanometer resolution.
- Robust Performance: Generally unaffected by target surface color, ambient light conditions (unlike optical sensors), or dust/dirt (unless conductive or excessively thick). Performance is primarily dependent on the dielectric properties in the sensing gap.
- Simple Integration: Compact designs and standard electrical outputs (like 0-10V, 4-20mA, IO-Link) simplify integration into control systems.
Important Considerations & Limitations
To select and use these sensors effectively, understanding their boundaries is key:
- Target Material Dependence: Sensitivity varies significantly with the target’s dielectric constant. Conductive materials produce the strongest signal. Sensing low-dielectric materials (like dry wood or foams) requires higher-sensitivity sensors or closer proximity.
- Sensing Range Limitation: Effective sensing distances are typically smaller than ultrasonic or laser sensors, ranging from a few millimeters to tens of millimeters, though specialized sensors exist for longer ranges.
- Environmental Sensitivity: Strong electromagnetic interference (EMI) can affect readings. The sensor can also be influenced by changes in humidity or the presence of conductive contaminants (like water or metal dust) near the sensing field.
- Field Shape & Size: The sensing field extends beyond the sensor face (fringing field). Careful mounting is needed to avoid unintended detection of nearby objects (“side look” or background interference). Shielding helps focus the field.
- Calibration: Calibration for specific target materials might be necessary, especially for precision displacement measurement applications.
Choosing the Right Capacitance Sensor: A Quick Guide
When selecting a capacitance proximity sensor or displacement sensor, consider:
- Required Range: What is the minimum and maximum distance you need to measure?
- Target Material: Is it conductive metal, plastic, liquid, or something else? What is its expected dielectric constant?
- Resolution & Accuracy: How precise do the measurements need to be?
- Output Signal: What type of signal does your control system require (digital switch, analog voltage/current, digital bus)?
- Environmental Conditions: Temperature range, humidity levels, potential for EMI, dust, moisture, or oils.
- Size & Mounting Constraints: Physical space available and mounting configuration.
- Shielding: Shielded sensors are less susceptible to interference and background effects, focused for axial detection. Unshielded sensors have a larger lateral field.
From the seamless interaction with your phone to the complex choreography of industrial robots, capacitance distance sensors provide a vital, non-contact sensing solution. By masterfully harnessing the fundamental properties of capacitance, these devices deliver precise positioning, reliable presence detection, and accurate measurement across an extraordinary range of materials and challenging environments. Understanding their operating principles, strengths, and limitations empowers engineers and designers to leverage their unique capabilities, bringing efficiency and intelligence to countless modern technologies.