liquid proximity sensor
- time:2025-07-05 03:00:52
- Click:0
Liquid Proximity Sensors: The Key to Non-Contact Liquid Detection
Ever fumbled with messy float switches or wrestled with unreliable conductivity probes to detect liquid levels? These traditional methods often fall short in demanding industrial environments. Enter the liquid proximity sensor: a sophisticated, reliable solution revolutionizing how we detect the presence or absence of liquids without direct contact. This technology provides a cleaner, more robust, and often more accurate approach to fluid management across countless applications. Understanding how they work and where they excel is crucial for engineers and system designers seeking reliable automation.
Beyond Standard Proximity Sensors: A Specialized Focus
While standard proximity sensors detect the presence of metals or other objects, liquid proximity sensors are specifically engineered to sense liquids. They achieve this through adaptations in their core sensing principles – primarily capacitive or inductive – making them far more suitable for liquid detection tasks than their general-purpose counterparts. The key differentiator lies in their ability to reliably trigger when liquid enters their detection zone, ignoring empty space or air, and often functioning effectively even within non-metallic tanks or pipes.
Core Operating Principles: Capacitive vs. Inductive
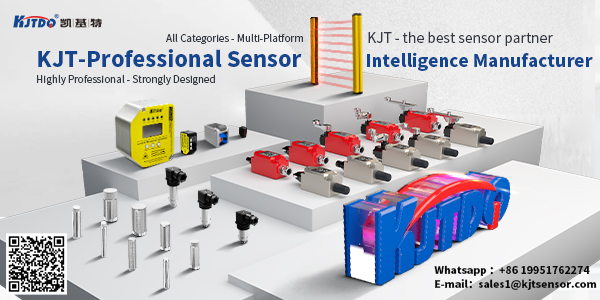
Liquid proximity sensors leverage two main technologies, each with distinct advantages:
- Capacitive Liquid Proximity Sensors: These sensors detect changes in capacitance caused by the presence of a liquid. They essentially consist of two electrodes forming a capacitor. When a liquid (which has a different dielectric constant than air) enters the sensor’s field, it alters the capacitance between the electrodes. This change is detected by the sensor’s electronics, triggering an output signal. Capacitive sensors are highly versatile:
- Detect both conductive and non-conductive liquids (water, oil, solvents, chemicals, adhesives).
- Work effectively through non-metallic container walls (plastic, glass), enabling external mounting.
- Ideal for point level detection (full/empty) in tanks, reservoirs, and pipelines.
- Often feature adjustable sensitivity to handle different liquids or wall thicknesses.
- Inductive Liquid Proximity Sensors (Specially Designed): Traditional inductive sensors detect conductive metals. However, variations exist specifically designed to sense conductive liquids like water, acids, or coolants based on induced eddy currents. These sensors generate a high-frequency electromagnetic field. When a conductive liquid enters this field, it induces tiny eddy currents within the liquid, causing a measurable change in the sensor’s oscillation amplitude or frequency, triggering the output.
- Primarily detect conductive liquids.
- Require direct exposure to the liquid or mounting within a conductive metallic tank wall (as the metal acts as the “target” the liquid displaces).
- Offer excellent performance in harsh environments (high pressure, temperature).
- Immune to factors like color, opacity, or bubbles that might affect optical methods.
Why Choose Liquid Proximity Sensors? Compelling Advantages
The shift towards using dedicated liquid proximity sensors is driven by several significant benefits over traditional contact methods and generic proximity switches:
- Non-Contact Operation: Eliminates the need for moving parts (like floats) or electrodes directly immersed in the fluid. This reduces wear, maintenance requirements, and the risk of contamination. There’s no physical contact to foul or degrade.
- Enhanced Reliability: Without moving parts susceptible to jamming or wear, and sealed solid-state electronics, these sensors offer superior long-term reliability, especially in demanding or continuous operation scenarios.
- Harsh Environment Resilience: Many models boast high IP ratings (e.g., IP67, IP69K), are constructed from chemically resistant materials (like PPS or PVDF), and can withstand extreme temperatures, pressures, vibration, and exposure to aggressive media. They are often rated for high-pressure washdown environments common in food processing.
- Simplified Installation & Maintenance: Mounting externally (capacitive types) or through threaded ports is generally straightforward. The absence of intrusive components simplifies cleaning and significantly lowers maintenance overhead.
- Versatility: Capacitive sensors, in particular, handle a very wide range of liquid types, from water to oils to viscous pastes. Solutions exist for almost any industrial liquid detection challenge.
Where Liquid Proximity Sensors Shine: Key Applications
The robustness and reliability of liquid proximity sensors make them indispensable across numerous sectors:
- Industrial Automation & Process Control: Monitoring coolant levels in machining centers, detecting lubricant presence, controlling fill levels in reservoirs, preventing pump dry-run, leak detection.
- Food and Beverage Production: Ensuring correct liquid levels in mixing tanks, detecting product flow in pipelines (e.g., milk, juice), verifying bottle/can filling, preventing overflow in CIP (Clean-in-Place) systems. Hygienic design and washdown capability are critical.
- Chemical & Pharmaceutical Manufacturing: Precise detection of aggressive solvents, acids, bases, and pharmaceutical ingredients within reactors, storage tanks, and transfer lines. Chemical compatibility of wetted materials is paramount.
- Water & Wastewater Management: Monitoring water levels in tanks, basins, and sumps, detecting pump dry-run protection, verifying flow presence in pipes.
- HVAC Systems: Monitoring boiler water levels, detecting condensate in drain pans, ensuring chiller fluid presence.
- Mobile Hydraulics & Machinery: Checking hydraulic oil reservoirs, coolant levels in engines and transmissions, windshield washer fluid levels.
Critical Considerations for Selection and Implementation
Choosing the right liquid proximity sensor requires careful evaluation:
- Liquid Properties: Is it conductive or non-conductive? Viscous? Oily? Foamy? Aggressive? This primarily determines the choice between capacitive or inductive types and material compatibility.
- Container Material: Can the sensor be mounted externally (capacitive through plastic/glass) or does it need internal mounting (often inductive)? Metal tanks may favor inductive sensors sensing the displaced tank wall.
- Environment: Consider temperature extremes, pressure ratings, potential for condensation, washdown requirements, and exposure to chemicals or cleaning agents. Select the appropriate IP rating and housing material.
- Required Function: Point level detection (full/empty) is the most common. Some capacitive sensors offer short-range continuous level approximation.
- Output Type: Common outputs include PNP, NPN (switching), or analog (4-20mA, 0-10V) signals. Choose based on your PLC or control system requirements.
- Mounting: Ensure the chosen sensor has a suitable thread size or mounting configuration for your application location. Proper sealing is vital for internally mounted sensors.
Embracing Precision Liquid Sensing
Liquid proximity sensors represent a fundamental leap forward in fluid detection technology. By offering reliable, non-contact operation in challenging environments, they eliminate many of the headaches associated with older methods. Whether ensuring a CNC machine doesn’t run without coolant, preventing costly overflows in a chemical reactor, or verifying product flow in a beverage line, these robust devices deliver consistent performance. Understanding the nuances between capacitive and inductive technologies, along with careful consideration of application specifics, empowers engineers to implement the optimal sensing solution. The result is enhanced process reliability, reduced downtime, and improved overall system efficiency across a vast spectrum of industries.