8mm inductive proximity sensor
- time:2025-07-05 00:36:14
- Click:0
The Mighty Miniature: Why 8mm Inductive Proximity Sensors Dominate Automation
Imagine a factory floor humming with activity. Robotic arms weld with precision, conveyor belts transport components swiftly, and automated machines assemble products flawlessly. Yet, beneath this orchestrated chaos lies a silent, critical workforce – tiny sensors ensuring everything happens in the right place, at the right time. Among these unsung heroes, the 8mm inductive proximity sensor stands out as a remarkably versatile and indispensable component. Its compact size belies its significant impact, providing reliable, non-contact detection for countless applications where space is at a premium and precision is paramount.
Understanding the Power Within: How They Work
At its core, an inductive proximity sensor operates on a simple yet elegant electromagnetic principle. It contains an oscillator circuit generating a high-frequency electromagnetic field radiating from its active face (the sensing surface). When a ferrous (iron-based) or non-ferrous metal target (like aluminum, brass, or copper) enters this field, eddy currents are induced on the target’s surface. These eddy currents draw energy from the sensor’s oscillator, causing its amplitude to decrease. An internal circuit, typically including a demodulator and trigger stage, detects this amplitude change. Once the change exceeds a predetermined threshold – the switching point – the sensor’s output state flips, signaling the presence of the target. Crucially, this detection happens without any physical contact, making it ideal for harsh environments with dirt, oil, vibration, or where rapid cycling is required.
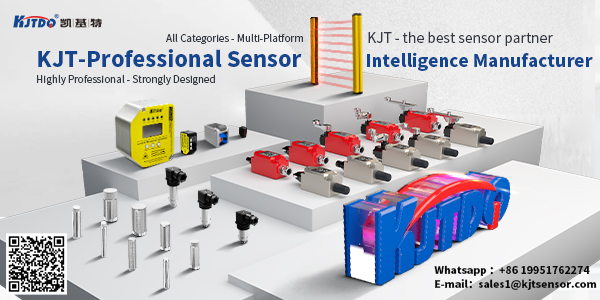
Why 8mm? The Advantage of Compactness
The “8mm” designation refers to the cylindrical barrel diameter of the sensor’s housing. This specific size strikes an exceptional balance between performance and space constraints:
- Space Optimization: In modern machinery and compact automation cells, every millimeter counts. The slim 8mm profile allows installation in locations inaccessible to larger sensors, enabling denser component packing and more elegant designs. Think robotic grippers, small actuators, tool changers, miniature slides, and PCBA handling.
- Sufficient Sensing Range: Despite its small size, a standard 8mm inductive sensor typically offers a nominal sensing range (Sn) of 1-2mm for steel targets*. While this range is shorter than larger sensors (e.g., 18mm or 30mm barrels), it’s perfectly adequate for detecting small parts (screws, nuts, pins), verifying tool presence, confirming end positions on miniature cylinders, or monitoring thin metal sheets/shims. Some specialized models might offer slightly higher ranges for non-ferrous metals.
- Robustness in Miniature: Don’t let the size fool you. Quality 8mm inductive sensors are engineered to be incredibly rugged. They boast high resistance to shock and vibration, essential for dynamic machinery. Standard IP67 or IP68 ratings mean they are protected against harsh industrial contaminants like dust, coolants, and oils, and often can withstand temporary immersion. Their non-contact nature inherently eliminates wear and tear on both the sensor and the target.
- Cost-Effectiveness: Their widespread use and standardized manufacturing processes make 8mm sensors highly economical, providing excellent value and reliability for automation budgets.
Where the Miniature Powerhouse Shines: Key Applications
The versatility of the 8mm inductive sensor makes it ubiquitous across numerous sectors:
- Miniature Pneumatic Cylinders: Detecting piston rod position (end-of-stroke) in compact cylinders is a classic application. The 8mm size fits perfectly alongside or within cylinder mounts.
- Robotics & Grippers: Verifying successful part pickup or release within tight gripper jaws; confirming tool changer position; monitoring joint limits.
- Conveyor Systems & Sorting: Detecting the presence or absence of small metal parts, cans, or caps on lanes; verifying correct orientation.
- Machine Tools & CNC: Tool presence/absence detection in turrets or spindles; monitoring coolant flow via metal vanes; guarding safety doors.
- Small Assembly Machines: Part verification at assembly stations; checking for component presence before a process step (like welding or fastening); detecting jams.
- Packaging Machinery: Confirming the presence of metal foil seals, lids, or metallic components on packaging lines.
- Semiconductor & Electronics Handling: Detecting metal carriers, clamps, or fixtures in precise handling equipment.
Choosing and Using the Right 8mm Sensor
Selecting the optimal 8mm sensor involves considering several factors beyond just size:
- Flush or Non-Flush Mounting: Shielded (Flush Mount) sensors can be installed flush within metal brackets without affecting their sensing field, maximizing space utilization. Non-Shielded (Non-Flush Mount) sensors offer longer sensing ranges but require clearance around the sensing face (no surrounding metal).
- Sensing Range (Sn): Verify the required distance to the target and ensure the sensor’s Sn meets or exceeds it for your target material. Remember, Sn is typically calibrated for mild steel; non-ferrous metals require a correction factor (reduction).
- Output Configuration: NPN (sinking) or PNP (sourcing) transistor outputs are standard. Choose based on the input requirements of your controller (PLC, microcontroller). Some sensors offer Normally Open (NO) or Normally Closed (NC) switching logic.
- Connector Type: Common options include integrated fixed cables, M5/M8/M12 quick-disconnect connectors, or bare wires. Choose based on environmental needs and ease of maintenance.
- Environmental Specifications: Ensure the sensor’s operating temperature range, IP rating, and resistance to chemicals (if applicable) meet your application’s demands.
- Material & Build Quality: Look for sensors built with high-grade materials (e.g., stainless steel housing, PBT sensing face) for long-term reliability.
Installation Tips:
- Ensure the target approaches the sensor perpendicularly to the active face for reliable triggering.
- Maintain the recommended installation distances from surrounding metal as specified by the manufacturer, especially for non-flush types.
- Avoid mounting sensors directly facing each other without sufficient distance to prevent mutual interference.
- Secure wiring properly to prevent strain on the cable or connector.