keyence capacitive sensor
- time:2025-07-05 00:30:12
- Click:0
Unlocking Precision: How Keyence Capacitive Sensors Revolutionize Non-Contact Detection
In the dynamic world of industrial automation, precision, reliability, and efficiency aren’t just ideals; they are necessities for staying competitive. When materials are delicate, environments are challenging, or processes demand non-intrusive monitoring, capacitive sensors rise as a critical solution. And within this domain, Keyence capacitive sensors have consistently set benchmarks, offering an unparalleled blend of innovation, robustness, and application versatility. This article explores the core principles, unique advantages, and transformative applications of these remarkable sensing devices.
The Core Principle: Sensing Without Touching
At their foundation, capacitive sensors operate on a simple yet powerful electrical principle. They generate an electrostatic field emanating from their sensing face. When any object enters this field – whether conductive like metal or non-conductive like plastic, glass, wood, or liquid – it alters the capacitance of the system. The sensor’s sophisticated internal circuitry detects this minute change in capacitance, triggering a highly reliable output signal (ON/OFF). This fundamental capability makes capacitive sensors inherently non-contact, eliminating wear and tear on both the sensor and the target, a critical advantage over mechanical switches.
Why Keyence Elevates Capacitive Sensing
While the basic principle is universal, Keyence engineers have pushed the boundaries, transforming standard capacitive technology into advanced solutions. Here’s what distinguishes Keyence capacitive sensors:
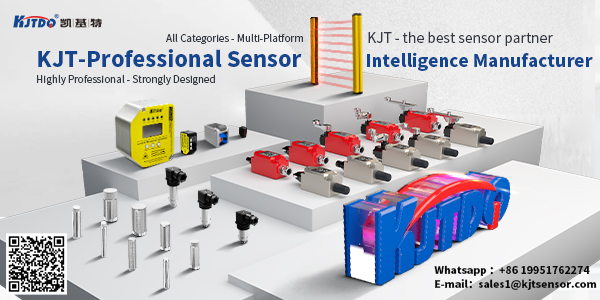
- Unmatched Sensitivity & Stability: Keyence sensors are renowned for their ability to detect minute objects or subtle changes through various barriers. They achieve remarkable stability, minimizing false triggers often caused by changes in temperature, humidity, or electrical noise. Advanced signal processing algorithms are key to this consistent performance.
- Extremely Long Sensing Distances: Compared to many standard capacitive sensors, Keyence models typically offer significantly longer effective sensing ranges relative to their size. This provides greater flexibility in mounting and simplifies integration into complex machinery or tight spaces.
- Exceptional Noise Immunity: Industrial environments are electrically noisy. Keyence designs incorporate robust noise resistance, ensuring reliable operation even near variable frequency drives (VFDs), large motors, or welding equipment, where other sensors might falter.
- Intelligent Teach Functionality: Many Keyence capacitive sensors feature an intuitive Teach function. Simply presenting the target and pressing a button automatically configures the optimal sensing point and sensitivity. This eliminates tedious manual potentiometer adjustments, drastically reducing setup time and potential errors.
- Compact & Rugged Design: Keyence emphasizes miniaturization without compromising durability. Their sensors often feature incredibly compact housings while boasting excellent resistance to water, oils, and chemicals (high IP ratings), making them suitable for harsh washdown or outdoor settings.
- Diverse Range for Specific Needs: Understanding diverse application demands, Keyence offers a broad portfolio. This includes standard cylindrical sensors, flat-pack designs for flush mounting, high-temperature variants, specialized models for fluid detection, incredibly tiny models (under M3 thread!), and sensors specifically tuned for detecting fill levels in non-conductive containers.
Transforming Industries: Key Applications
The unique strengths of Keyence capacitive sensors make them indispensable across countless sectors:
- Level Detection: Continuously monitoring the presence or absence of liquids, powders, granules, or pellets within non-metallic containers (bottles, tubes, tanks, hoppers) is a core application. They excel at detecting both high and low levels, preventing overflows or dry running.
- Object Presence/Absence: Verifying the presence, absence, or correct positioning of components on assembly lines – whether PCBs, plastic parts, labels, caps, or even small electronic chips – is crucial for quality control and process flow.
- Material Thickness Measurement: In processes involving films, paper, textiles, or coatings, these sensors can detect subtle variations in material thickness or layers, ensuring consistent product quality.
- Warpage & Warp Detection: Detecting subtle bends or deformations in materials like wafers, panels, or sheets during production or handling.
- Liquid Presence: Confirming the presence of liquids in clear tubes or verifying the filling in opaque containers is simple and reliable.
- Position Verification: Ensuring parts are seated correctly in fixtures or jigs before critical operations like machining or welding proceed.
Tangible Benefits: Driving Operational Excellence
Integrating Keyence capacitive sensors delivers significant ROI beyond reliable detection:
- Reduced Downtime: Non-contact operation means no mechanical wear, leading to significantly longer service life and less unplanned maintenance. Their robustness minimizes failures caused by environmental factors.
- Enhanced Quality Control: Consistent, high-precision detection ensures defects are caught early, reducing scrap rates and upholding stringent quality standards.
- Increased Production Speed: Reliable detection allows machinery to operate safely at optimal speeds without the risk of jams or missed detections.
- Simplified Setup & Maintenance: The user-friendly Teach function and rugged design drastically reduce commissioning time and ongoing maintenance requirements.
- Versatility: The ability to detect such a wide range of materials through barriers solves complex application challenges that might otherwise require multiple sensor types or custom solutions.
Selecting the Right Keyence Capacitive Sensor
Choosing the optimal sensor involves considering key factors:
- Target Material: Is it conductive or non-conductive?
- Required Sensing Distance: How far away can the sensor be mounted?
- Mounting Constraints: Is space limited? Flush mounting required?
- Environmental Conditions: Temperature extremes, humidity, exposure to water/oil/chemicals?
- Detection Task: Presence, absence, level, thickness?
- Output Type Required: NPN, PNP, Analog?
Keyence’s extensive range and detailed technical documentation make this selection process straightforward. Consulting their catalogs or application engineers is highly recommended for complex scenarios.
Conclusion
Keyence capacitive sensors represent far more than just proximity detectors. They embody a powerful fusion of sophisticated technology, exceptional engineering, and user-centric innovation. Their ability to reliably detect virtually any material through non-conductive barriers, coupled with long ranges, high noise immunity, and ruggedness, makes them a cornerstone solution for modern automation. By enhancing precision, boosting reliability, and streamlining processes, these sensors unlock significant value, driving efficiency and quality across a multitude of demanding industrial applications.