inductive ring sensor
- time:2025-07-04 03:25:03
- Click:0
The Essential Guide to Inductive Ring Sensors: Principles, Applications, and Selection
Imagine a critical bolt missing in a high-speed automotive assembly line, or a piece of metal contaminant slipping into food packaging. These costly errors and safety hazards are precisely what inductive ring sensors are designed to prevent. Operating with whisper-quiet vigilance, these robust workhorses of industrial automation provide non-contact, reliable detection of metallic objects passing through their core, forming an invisible yet impenetrable gatekeeper for quality and safety.
Demystifying the Core Technology: How Inductive Ring Sensors Work
At their heart, inductive ring sensors leverage the fundamental principles of electromagnetic induction. Here’s the breakdown:
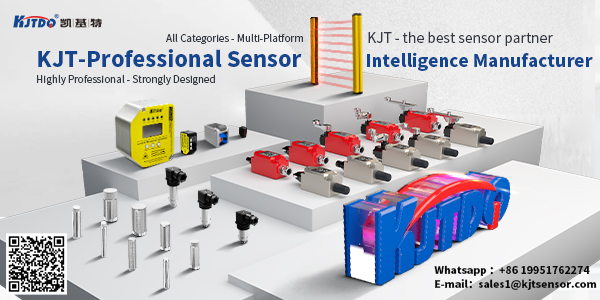
- Generating the Field: An electrical coil wound around a ferrite core within the sensor ring is energized with an alternating current. This current generates a high-frequency oscillating electromagnetic field that radiates outwards from the coil, effectively filling the aperture of the ring.
- The Target’s Influence: When a metallic object (the “target”) enters this active electromagnetic field, it disrupts the field lines. This disturbance isn’t passive; it induces small circulating electrical currents within the metal target itself, known as eddy currents.
- Detection Mechanism: These eddy currents consume energy from the sensor’s original oscillating field. This energy loss causes a measurable change in the sensor’s internal characteristics – typically a reduction in the amplitude of the oscillation or a shift in its frequency.
- Signal Processing & Output: Sophisticated internal electronics within the inductive sensor continuously monitor these electrical parameters. When the change exceeds a predefined threshold (indicating the presence of a suitable metal target within the sensing range), the sensor triggers its switching output. This output signal (often PNP/NPN transistor, NO/NC contacts, or analog) is then used to alert a control system like a PLC, trigger an action (stop a conveyor, reject a part, start counting), or simply provide a status indication.
This entire process happens without any physical contact between the sensor and the target object. This inherent non-contact nature is a primary reason for their exceptional reliability, long operational life, and minimal maintenance requirements.
Where Inductive Ring Sensors Shine: Key Applications
Their unique form factor and detection principle make inductive ring sensors indispensable across numerous sectors. Key applications include:
- Presence/Absence Verification: Confirming the passage or presence of metal parts or components through an assembly line, machine, or packaging system (e.g., verifying bolts in automotive assemblies, checking lids on jars).
- Counting: Accurately tallying metallic objects (pipes, cans, fasteners, tools) as they pass through the ring’s aperture. High-speed counting is a common strength.
- Contamination Detection: Protecting equipment and product integrity by detecting unwanted metal particles within non-metallic substances or packaging. Widely used in food & beverage, pharmaceutical, and plastic industries to screen for tramp metal before it causes damage or contamination.
- Position Sensing / Control: Monitoring the position of metal components actuated through the ring, such as pistons, valves, or slides. Ideal for end-of-stroke detection.
- Speed Monitoring: Detecting the teeth of metallic gears or sprockets rotating through the ring to determine rotational speed.
- Security: Acting as a non-intrusive metal detector gate in security screening applications (though often distinct from walk-through arches).
Choosing the Right Inductive Ring Sensor: Critical Considerations
Selecting the optimal inductive ring sensor requires careful evaluation of application parameters:
- Aperture Size (Internal Diameter): This is paramount. The ring’s inner diameter must be large enough to allow the target object to pass through freely, but not so large that detection becomes inconsistent or the sensing field is too weak. Measure the largest cross-section of the object needing detection.
- Sensing Distance / Range: Defined as the maximum distance from the sensing face (inside the ring bore) at which a standard target can be reliably detected. Ensure the sensor’s specified sensing distance accommodates your target size and the speed/vibration of the application. Note that detection capability often decreases slightly towards the center of very large bore rings.
- Target Material: While inductive sensors primarily detect ferrous metals (like iron and steel), they can also detect non-ferrous metals (like aluminum, copper, brass) but typically at reduced sensing ranges. Confirm the sensor’s specifications match your primary target material.
- Target Size & Shape: Smaller targets require sensors with higher sensitivity or need to pass closer to the sensing area. Thin targets (e.g., wires) can be challenging for some sensors.
- Environmental Factors: Consider operating temperature, potential exposure to chemicals/coolants/oil (requiring specific IP ratings like IP67 or IP69K), presence of strong electromagnetic fields, or physical shocks/vibration.
- Output Type & Electrical Requirements: Match the sensor’s output signal (e.g., PNP, NPN, NO, NC, analog voltage/current) and voltage supply (e.g., 10-30V DC) to your control system’s inputs. IO-Link capability is increasingly valuable for Industry 4.0 integration, diagnostics, and parameterization.
- Mounting & Installation: Ensure adequate clearance around the sensor body for installation and consider protection against mechanical damage. Pay attention to recommendations regarding the distance to surrounding metal (“flush” or “non-flush” mounting characteristics can apply to the ring’s external structure).
The Quiet Enabler of Efficiency and Quality
From safeguarding our food supply to ensuring the precision of high-value manufacturing, inductive ring sensors operate as silent sentinels. Their ability to provide robust, non-contact detection of metallic objects passing through their core, combined with inherent reliability and trouble-free operation, makes them a cornerstone technology in countless automated processes. Understanding their operating principles and key selection criteria empowers engineers and system integrators to leverage these powerful sensors effectively, driving greater operational efficiency, enhanced product quality, and uncompromising safety standards on the factory floor and beyond. As industries push towards greater automation and connectivity, the role of these dependable rings in enabling smart manufacturing environments only continues to grow.