infrared laser distance sensor
- time:2025-07-04 01:54:38
- Click:0
Unlocking Precision: The Essential Guide to Infrared Laser Distance Sensors
Ever wondered how robots navigate warehouses with uncanny accuracy, how self-driving cars perceive obstacles, or how your smartphone measures rooms instantly? The invisible magic powering these feats often lies with a remarkably sophisticated yet compact device: the infrared laser distance sensor. This technological marvel quietly underpins countless modern applications, delivering precision where traditional methods falter. Understanding its capabilities unlocks a world of automation, safety, and efficiency.
At its core, an infrared laser distance sensor is an active optical measurement device. It operates by emitting a focused beam of invisible infrared laser light towards a target object. The sensor doesn’t rely on ambient light; instead, it generates its own illumination. The key principle involves analyzing the light’s interaction with the target:
- Time-of-Flight (ToF): This highly prevalent method measures the exact time it takes for the laser pulse to travel to the target and reflect back to the sensor. Since the speed of light (
c
) is a constant (approximately 3x10^8 m/s), the distance (d
) is calculated using the simple formula d = (c * t) / 2
, where t
is the measured time. ToF sensors excel in measuring longer ranges and offer fast update rates.
- Triangulation: Primarily used for shorter ranges and higher precision. The laser emitter projects a point onto the target. A separate receiver (like a small camera) positioned at a known angle observes the position of this laser spot. As the target distance changes, the location of the spot on the receiver shifts. Sophisticated algorithms calculate the distance based on this shift using trigonometric principles. Triangulation sensors achieve remarkable sub-millimeter accuracy.
Why has infrared light become the standard bearer for these sensors?
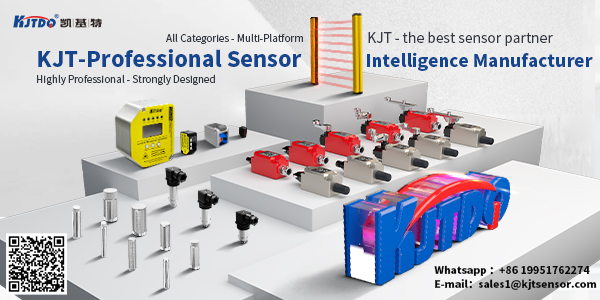
- Invisibility & Safety: The infrared spectrum used (typically near-infrared, NIR, around 850nm or 940nm) is invisible to the human eye. This eliminates visual distraction, glare, and potential safety hazards associated with visible lasers. It also allows for covert operation.
- Compactness & Efficiency: Infrared laser diodes are incredibly small, efficient, and relatively inexpensive to manufacture, enabling the creation of compact, low-power modules easily integrated into diverse devices.
- Environmental Stability: Infrared light is less susceptible to interference from ambient visible light compared to visible laser solutions, leading to more stable performance in varying lighting conditions.
- Focus & Range: Infrared lasers can be focused into very narrow, coherent beams, allowing for precise targeting over significant distances.
The versatility of infrared laser distance sensors has driven their adoption across a breathtakingly wide spectrum of industries:
- Industrial Automation & Robotics: This is a powerhouse application. Sensors guide robots for material handling, assembly verification (is the part in the right position?), coordinate measurement machines (CMMs), and ensure precise positioning on conveyors. Automated Guided Vehicles (AGVs) and autonomous mobile robots (AMRs) rely heavily on them for collision avoidance, navigation, localization, and docking.
- Consumer Electronics: Experience seamless functionality daily. They power smartphone apps for room scanning and interior design. Robot vacuum cleaners use IR laser sensors for mapping environments and detecting cliffs like stair edges. Proximity sensors in phones and tablets often utilize infrared lasers.
- Building & Construction: Modern laser distance meters and laser rangefinders have replaced cumbersome tape measures. Architects, surveyors, and DIY enthusiasts use them for quick, accurate measurements of distances, areas, and volumes indoors and outdoors.
- Automotive: While LiDAR (Light Detection and Ranging) often involves visible or near-IR lasers scanned across a field, the fundamental technology shares DNA with IR laser distance sensors. Essential for Advanced Driver-Assistance Systems (ADAS) like adaptive cruise control and automated emergency braking, and fundamental for the perception systems of autonomous vehicles. Parking assistance systems also commonly use IR laser sensors.
- Logistics & Warehousing: Inventory management systems leverage these sensors for pallet dimensioning, volume calculation, and optimizing storage space. Forklift safety systems use them to prevent collisions in narrow aisles.
- Security: Integrated into perimeter protection systems, intrusion detection setups, and automatic door sensors to detect the presence of objects or people.
- Drones (UAVs): Critical for altitude hold, terrain following, and obstacle avoidance during autonomous flight.
The compelling advantages driving this widespread adoption are clear:
- Non-Contact Measurement: Ideal for measuring delicate, hot, moving, or inaccessible objects without physical interaction.
- High Speed & Precision: Capable of taking thousands of measurements per second with millimeter-level accuracy or even better (especially triangulation).
- Compact Size & Robustness: Their small form factor allows integration into space-constrained devices, and many are built to withstand harsh industrial environments.
- Long Range Capabilities: Depending on the model and power, some sensors can reliably measure distances exceeding 100 meters.
- Reliability: Less prone to interference from surface color, texture, or ambient sound compared to ultrasonic sensors.
Of course, no technology is without its considerations:
- Target Properties: Highly reflective surfaces can cause signal saturation, while very dark or matte surfaces might absorb too much light, reducing signal strength and effective range. Transparent materials like glass or liquids can pose significant challenges as the laser beam may pass through or refract unpredictably.
- Ambient Light Interference: Although designed to be stable, extremely intense direct sunlight or other powerful infrared sources can potentially overwhelm the sensor’s receiver in outdoor applications.
- Cost: While costs have decreased significantly, higher precision and longer-range IR laser sensors can still be more expensive than ultrasonic alternatives.
The future of infrared laser distance sensing is vibrant. We are witnessing advancements in single-photon avalanche diode (SPAD) sensors enabling even longer ranges and better performance in sunlight. Integration with Artificial Intelligence (AI) allows for smarter interpretation of sensor data and enhanced object recognition. Sensor fusion, combining laser data with cameras, IMUs, and radar, creates more robust perception systems. Furthermore, relentless innovation continues to drive down costs and power consumption while enhancing miniaturization and performance envelopes.
From the precise assembly of microelectronics to the safe navigation of autonomous vehicles in complex urban environments, the infrared laser distance sensor has become an indispensable tool. Its unique blend of speed, accuracy, compactness, and versatility makes it the go-to solution for applications demanding reliable spatial awareness. As technology continues its relentless march forward, these intelligent eyes, operating silently in the infrared spectrum, will only become more sophisticated, further embedding themselves into the fabric of our automated and interconnected world.