m12 proximity sensor
- time:2025-07-04 00:18:10
- Click:0
Unlocking Efficiency: The Transformative Role of M12 Proximity Sensors in Industrial Automation
Ever wonder how factories seem to “sense” the presence of parts flying down a conveyor, or how robotic arms know exactly where to pick up an object without touching it? Often, the unsung heroes behind this seamless, non-contact detection are M12 proximity sensors. These compact, rugged devices are fundamental building blocks of modern automation, offering reliable, high-speed object detection critical for efficiency and safety. Understanding their design, capabilities, and applications unlocks significant potential for optimizing industrial processes.
The M12 Advantage: Compact Size, Industrial Strength
The “M12” designation refers to the sensor’s standardized 12mm threaded cylindrical housing. This ubiquitous form factor offers crucial benefits:
- Standardization: Ensures easy installation and replacement using common M12 connectors and mounting nuts across countless devices and control systems.
- Robustness: Typically constructed from nickel-plated brass or stainless steel, the housing provides excellent mechanical durability against vibration and accidental impacts common in harsh industrial settings.
- Environmental Protection: Most M12 proximity sensors boast high IP (Ingress Protection) ratings, such as IP67 or IP69K, meaning they are highly resistant to dust and water ingress, even surviving high-pressure washdowns in food and beverage or pharmaceutical applications.
- Space Efficiency: Their small diameter allows installation in tight spaces where larger sensors simply wouldn’t fit, enabling more compact machine designs.
Core Function: Non-Contact Detection
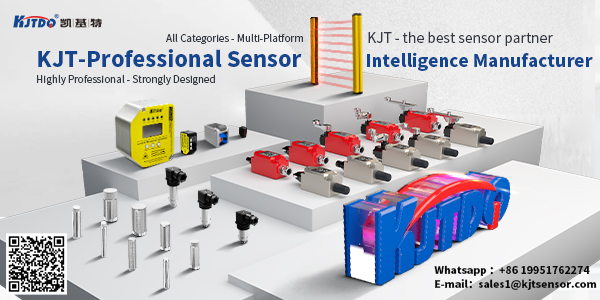
At their heart, M12 proximity sensors detect the presence or absence of a target object without physical contact. This is achieved primarily through two magnetic field-based technologies:
- Inductive Proximity Sensors: These are the most common M12 variant. They generate an electromagnetic field. When a metallic target (ferrous or non-ferrous) enters this field, it induces eddy currents within the target, causing a detectable change in the sensor’s internal oscillation circuit. The sensor then switches its output state (e.g., from OFF to ON or vice versa).
- Key Strength: Reliable detection of metal objects, unaffected by dust, oil, or non-metallic contaminants.
- Limitation: Primarily detects metal only. The effective sensing range varies depending on the target metal type.
- Capacitive Proximity Sensors: These sensors generate an electrostatic field. Any object (metal, plastic, wood, liquid, powder) entering this field alters the sensor’s capacitance, triggering an output switch.
- Key Strength: Detects a wide variety of materials, making them ideal for detecting non-metallic objects like plastic bottles, cardboard boxes, or liquid levels through tank walls (within specific limits).
- Limitation: Generally shorter sensing ranges than inductive types and can be more susceptible to environmental factors like humidity or buildup of material on the sensor face.
Why M12 Proximity Sensors Are Industrial Staple
Beyond their physical form, M12 proximity sensors deliver performance characteristics essential for demanding automation:
- High Switching Frequencies: They can detect objects moving at very high speeds, making them perfect for monitoring fast-paced production lines.
- Long Service Life: With no moving parts and robust construction, they offer exceptional reliability and longevity, minimizing downtime and maintenance costs.
- Resistance to Environmental Challenges: Their sealed design protects against dirt, dust, cutting fluids, coolants, and washdown processes.
- Electrical Noise Immunity: Well-designed M12 sensors exhibit strong resistance to common electrical interference found in industrial environments.
- Simple Integration: Standard PNP (sourcing) or NPN (sinking) output configurations with 3 or 4 wires easily interface with PLCs (Programmable Logic Controllers), robots, and other control systems.
Critical Considerations for Optimal Selection
Choosing the right M12 proximity sensor is vital for application success. Key factors include:
- Target Material: Is the object metal? If so, an inductive sensor is usually best. If detecting plastic, wood, glass, or liquids, a capacitive sensor is required.
- Required Sensing Distance (Sn): The nominal operating distance specified for a standard target. Ensure this suits your application clearance needs. Remember, actual range can be less for non-ferrous metals (inductive) or non-standard targets (capacitive).
- Mounting Constraints: Ensure the sensor’s physical size (body length, flush or non-flush mounting style) fits the available space. Standard M12 threaded bodies come in various lengths. Non-flush mount inductive sensors offer longer ranges but require space around the face; flush-mount types can be embedded in metal.
- Environmental Conditions: Verify the required IP rating (e.g., IP67 for dust and temporary water immersion, IP69K for high-pressure washdown). Consider temperature extremes, chemical exposure, and physical shock/vibration levels.
- Output Configuration: PNP (sourcing) or NNP (sinking)? Normally Open (NO) or Normally Closed (NC)? This must match the input requirements of your controller.
- Connector Style: Integral cable or detachable M12 connector? Detachable connectors offer easier replacement.
Ubiquitous Applications: Where You’ll Find M12 Proximity Sensors
The versatility and reliability of M12 proximity sensors make them indispensable across countless industries and applications:
- Assembly Lines: Detecting presence/absence of parts on conveyors, verifying component insertion, counting objects.
- Packaging Machinery: Monitoring carton flap closure, detecting filled bottles/cans, controlling fill levels (capacitive).
- Material Handling: Confirming pallet position, detecting objects at ends of conveyor belts (end-of-travel detection), monitoring robotic arm positions.
- Machine Tooling: Tool breakage detection, verifying part clamping, monitoring turret positions on CNC machines.
- Robotics: End-effector position confirmation, detecting workpiece pickup/drop-off.
- Automotive Manufacturing: Position sensing of cylinders and valves, detecting components through various stages of assembly.
- Food & Beverage: Sanitary processing areas (often requiring stainless steel housings and high IP ratings), detecting containers through packaging, level sensing.
The Engine of Unseen Automation
From the simplest position verification to complex robotic guidance, M12 proximity sensors are the silent, dependable workhorses powering modern industry. Their compact, rugged M12 form factor, combined with reliable non-contact sensing principles (inductive or capacitive), high speed, and environmental resilience, makes them an essential component for achieving efficiency, reliability, and safety in automated systems. By carefully selecting the right M12 sensor based on material, distance, environment, and output needs, engineers and technicians can build more robust, efficient, and intelligent machinery, driving productivity forward one detection point at a time.