micro inductive sensor
- time:2025-07-03 03:49:06
- Click:0
Micro Inductive Sensors: Empowering Precision in Miniature Applications
Imagine intricate machinery self-monitoring its components, robotic arms sensing infinitesimally small positional shifts, or medical devices detecting micro-movements with unwavering reliability – all within spaces where traditional sensors simply wouldn’t fit. This is the domain where micro inductive sensors excel, offering non-contact, robust sensing solutions in incredibly compact packages. Understanding their unique capabilities is key to unlocking advanced automation and monitoring possibilities.
At their core, micro inductive sensors operate on the fundamental principle of electromagnetic induction, the same physics that powers transformers and electric generators. These compact devices contain a miniature coil energized by an alternating current, generating a high-frequency electromagnetic field. When a metallic target object enters this field, eddy currents are induced within the metal. The critical interaction occurs because these eddy currents create their own opposing electromagnetic field, which interacts with the original field generated by the sensor’s coil.
This interaction causes a measurable change in the sensor’s internal circuit – typically a shift in the energy consumption of the oscillator circuit generating the field or a specific voltage change. Sophisticated electronics within the sensor detect this shift. Once the change exceeds a predefined threshold (the sensing point), the sensor’s output switches state. This output is usually a simple digital signal (e.g., changing from “OFF” to “ON,” or vice versa), making integration with control systems like PLCs remarkably straightforward. Crucially, this entire sensing process occurs without any physical contact between the sensor and the target.
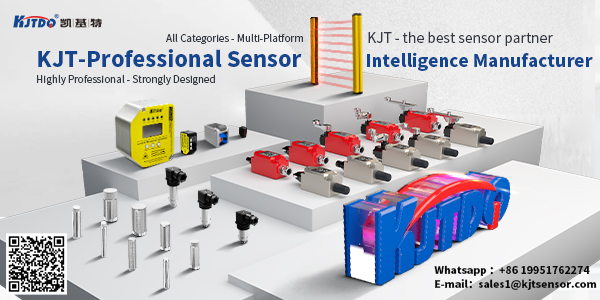
The defining characteristic and primary advantage of micro inductive sensors is their extremely small size. We’re talking about sensors often measuring just a few millimeters in diameter and length. This miniaturization isn’t just about saving space; it enables entirely new applications:
- Integration into Compact Machinery: Fitting sensors inside miniature actuators, small robotic joints, or dense electronic assemblies where space is at an absolute premium.
- PCB Mounting: Surface-mount (SMD) micro sensors can be directly integrated onto printed circuit boards for tasks like component presence detection inside devices.
- Precision Positioning in Tight Tolerances: Sensing tiny metallic parts, valve positions, or piston movements in mechanisms with very little clearance.
- Wearable Tech & Medical Devices: Enabling position sensing in miniaturized medical instruments or diagnostic equipment.
- Semiconductor Manufacturing: Detecting ultra-small components or tool positions within highly controlled, compact fabrication environments.
Beyond their diminutive size, micro inductive sensors inherit significant advantages from their larger inductive cousins:
- Exceptional Durability & Long Life: The absence of moving parts and physical contact with the target makes them highly resistant to wear and tear. They are built to withstand millions of switching cycles.
- Robust Performance in Harsh Environments: Immunity to dust, oil, moisture, vibration, and temperature fluctuations (within specified ranges) makes them ideal for industrial floors, automotive applications, and outdoor equipment. Their sealed construction contributes significantly to this resilience.
- High Switching Speeds: Capable of detecting very rapid target movements, essential for high-speed automation and counting applications.
- Non-Contact Operation: Eliminates friction, wear on targets, and potential damage to delicate objects. Only the electromagnetic field interacts with the target.
- Reliable Detection: Highly consistent and repeatable switching, unaffected by surface finish (within limits) on most common metals.
While incredibly versatile, effective implementation hinges on understanding their specific characteristics:
- Ferrous vs. Non-Ferrous Targets: Standard micro inductive sensors typically have a longer sensing range for ferrous metals (like iron, steel) compared to non-ferrous metals (like aluminum, copper, brass). Factor Reduction (FR) specified in datasheets indicates the reduced sensing distance for non-ferrous metals compared to steel. Choosing a sensor with sufficient range for the target material is crucial. “All-metal” variants exist with more consistent detection across metal types but often at a higher cost.
- Shielded vs. Unshielded:
- Shielded Micro Sensors: The coil is encapsulated in a ferrous metal housing that directs the sensing field primarily out of the front face. This allows for flush mounting in metal surrounds, a significant advantage in many compact designs. However, their sensing range is generally shorter.
- Unshielded Micro Sensors: The coil is not surrounded by the shielding metal. This provides a longer sensing range but requires a non-metallic zone around the sensor barrel during installation to prevent interference from surrounding metal.
- Sensing Range: Due to their size, micro sensors inherently have shorter nominal sensing ranges (Sn), often measured in fractions of a millimeter (e.g., 0.3mm, 0.8mm, 1.5mm). Precision positioning requires careful selection based on the required gap and target material.
- Output Configuration: Available in NPN (sourcing) or PNP (sinking) transistor outputs, typically Normally Open (NO) or Normally Closed (NC), to match the input requirements of the control system. Some offer analog outputs (current or voltage proportional to distance) for precise position measurement.
- Operating Frequency: Critical for high-speed applications, indicating how quickly the sensor can detect targets passing by.
- Environmental Ratings: Pay close attention to IP (Ingress Protection) ratings for dust and moisture resistance, and temperature ranges, especially for challenging environments.
Selecting the right micro inductive sensor requires a clear definition of the application needs:
- Target Material: What metal (steel, aluminum, stainless steel, etc.) needs detection?
- Required Sensing Distance: What is the maximum air gap between the sensor face and the target?
- Mounting Constraints: Can the sensor be flush-mounted, or is there space around it? Does surrounding metal pose an issue?
- Size Limitations: What are the absolute maximum dimensions allowed?
- Environmental Conditions: Exposure to liquids, chemicals, extreme temperatures, or intense vibration?
- Electrical Interface: Needed output type (NPN/PNP, NO/NC), voltage supply?
- Performance Needs: Required switching speed? Analog feedback required?
Driven by the relentless demand for miniaturization and smarter automation, micro inductive sensor technology continues to evolve. We see trends towards even smaller form factors, improved sensing ranges relative to size, enhanced resilience to extreme conditions, integrated IO-Link communication for advanced diagnostics and parameterization, and the development of specialized variants for unique challenges. Their unique blend of robustness, contactless operation, and miniaturization ensures they will remain fundamental components in the intricate dance of modern precision engineering, finding roles wherever reliable detection in the smallest spaces is paramount. From ensuring the correct assembly of minuscule electronics to guaranteeing the precise alignment of components in complex machinery, these tiny powerhouses deliver big on performance. Choosing wisely means matching the sensor’s specific capabilities – its size, shielding, sensing range, material compatibility, and environmental ratings – to the precise demands of the task at hand.