m4 proximity sensor
- time:2025-07-03 00:36:19
- Click:0
The M4 Proximity Sensor: Tiny Titan of Industrial Precision
In the relentless drive for efficiency, safety, and precision within modern manufacturing and automation, minute components often hold monumental importance. Tucked away on assembly lines, robotic arms, and intricate machinery, a small but potent force works ceaselessly: the M4 proximity sensor. This diminutive device, defined by its miniature 4mm threaded barrel, is the epitome of “small package, big impact.” Forget cumbersome switches; the M4 offers non-contact, wear-free detection, becoming the silent sentinel enabling countless applications demanding reliability and compactness.
Unlocking the M4: More Than Just a Size
The designation “M4” primarily refers to the sensor’s compact threaded housing size – specifically, an M4 x 0.5 metric thread. This standardized miniature form factor allows these sensors to be installed in incredibly tight spaces where larger sensors simply wouldn’t fit. They are predominantly inductive proximity sensors, meaning they detect metallic targets without physical contact.
- The Core Principle: Internally, an M4 inductive sensor houses an oscillator circuit generating a high-frequency electromagnetic field emanating from its active face. When a metallic object (ferrous metals like iron, steel, or non-ferrous like aluminum, copper, brass) enters this field, eddy currents are induced within the target. This interaction dampens the oscillator’s amplitude. An integrated circuit monitors this change, triggering the sensor’s solid-state output (like an NPN or PNP transistor) to switch state (ON/OFF). This signal is then used by the control system (PLC, microcontroller) to confirm presence, position, or count.
Key Features and Capabilities: Why M4 Reigns Supreme in Miniature
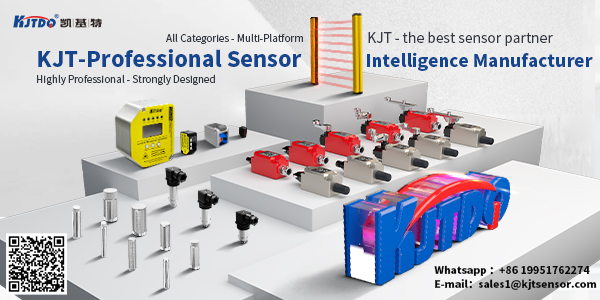
The value proposition of the M4 proximity sensor lies in its unique combination of attributes:
- Ultra-Compact Size (M4 x 0.5 Thread): This is the defining feature. Installation in confined spaces – tight machinery housings, small robotic grippers, compact linear actuators, PCB handling equipment – is where M4 sensors excel. They enable detection where no alternative exists.
- Non-Contact Operation: Eliminates mechanical wear and tear on both the sensor and the target, ensuring exceptional long-term reliability and virtually maintenance-free operation. This is critical in high-cycle applications.
- High Switching Frequency: Despite their size, quality M4 sensors boast impressive response speeds, often capable of detecting targets thousands of times per minute. This makes them ideal for high-speed counting, positioning, and automation tasks.
- Robust Construction: Designed for industrial environments, they typically feature stainless steel housing, offering resistance to corrosion, impacts, and vibration. High IP67 or IP68 ratings are common, providing excellent protection against dust, oil, coolants, and water ingress.
- Variety of Sensing Ranges: While inherently short-range due to their size (typically 1mm to 2mm nominal sensing distance for steel), this precision is exactly what’s needed for close-proximity detection in compact mechanisms.
- Output Options: Available with standard NPN (sinking) or PNP (sourcing) outputs (NO/NC configurations), and often rated for voltages like 10-30V DC, ensuring compatibility with most industrial control systems.
- LED Status Indicator: Most feature a built-in LED providing clear visual feedback on the sensor’s operating state (power, target detection), aiding rapid commissioning and troubleshooting.
Where the M4 Shines: Critical Applications
The compactness and reliability of the M4 proximity sensor make it indispensable across numerous demanding sectors:
- Miniature Robotics & Cobots: End-effector tooling detection, gripper position confirmation, and collision avoidance within the compact joints of collaborative robots. Precision is paramount here.
- Semiconductor & Electronics Manufacturing: Detecting tiny components on PCBs during assembly, placement, and testing; verifying micro-connector or chip presence in high-density packaging equipment. M4 size is non-negotiable at this scale.
- Medical Device Assembly: Ensuring precise positioning of small parts (syringes, implants, micro-fluidic components) within sterile and compact automated production lines. Reliability impacts patient safety.
- Precision CNC Machining & Tooling: Tool breakage detection on ultra-small drills/end mills, confirming spindle tool presence, monitoring micro-part positioning on pallets or fixtures.
- Small Part Counting & Sorting: Verifying the passage or presence of tiny metallic items like screws, pins, springs, or electronic components in vibratory feeders and sorting mechanisms. High-frequency capability is key.
- Textile & Packaging Machinery: Monitoring thread breaks, needle position, foil presence, or small actuator positions where space is severely limited.
- Valve & Actuator Position Feedback: Confirming open/closed states or end positions of miniature pneumatic or hydraulic cylinders.
Selecting the Right M4 Proximity Sensor: Key Considerations
Choosing the optimal M4 sensor requires careful attention to application specifics:
- Target Material: Standard models offer optimal range for ferrous steel. If detecting non-ferrous metals (aluminum, brass, copper) or stainless steel is required, specify sensors designed for reduced sensing ranges on these materials.
- Sensing Distance (Sn): Determine the required nominal operating distance. Remember the actual usable distance can be less, especially for non-ferrous. Factor in mounting tolerances.
- Output Configuration: Does your control system require NPN or PNP? Normally Open (NO) or Normally Closed (NC) logic? Wire sourcing (3-wire) is standard.
- Voltage Range: Ensure compatibility with your DC power supply (e.g., 12V DC, 24V DC).
- Environmental Factors: Confirm the required IP rating (IP67 for harsh washdowns, IP68 for submersion), temperature range, and resistance to specific chemicals, oils, or coolants.
- Housing Material: Stainless steel (V2A, V4A/AISI 303, 304, 316) is standard and highly recommended for industrial durability. Nickel-plated brass may be found in less demanding applications.
- Electrical Connection: Options include pre-wired cables (commonly PUR or PVC sheathed) or compact connectors (M5, M8). Choose based on your cabling infrastructure and space.
A Foundation for Smarter Automation
The M4 proximity sensor exemplifies how engineering ingenuity packs powerful functionality into a minuscule form. More than just a small switch, it is a fundamental building block for precision, reliability, and efficiency in modern automated systems where space is at an absolute premium. By providing non-contact, wear-free detection of metallic objects with impressive speed and ruggedness, the M4 ensures that even the smallest components and closest tolerances are managed with absolute certainty. Understanding their operation, capabilities, and selection