vibration proximity sensor
- time:2025-07-02 03:49:13
- Click:0
The Silent Watchdog: How Vibration Proximity Sensors Detect Presence Without Sight or Sound
Imagine machinery operating in a pitch-black, dusty environment. Optical sensors are blinded. Ultrasonic sensors are muffled by debris. How do you reliably detect the approach of an object or monitor critical machine health? Enter the often-overlooked but incredibly robust vibration proximity sensor – a technology that “feels” its surroundings, offering unique advantages where others falter. These ingenious devices translate physical oscillations into actionable data, providing a dependable solution for presence detection and condition monitoring in challenging industrial landscapes.
Unlike traditional optical proximity sensors that rely on light beams or ultrasonic variants that use sound waves, vibration proximity sensors operate on a fundamentally different principle: they detect the physical vibrations generated by an approaching object or emanating from a machine itself. They are essentially tuned ears for mechanical movement. Typically featuring a piezoelectric element or a sophisticated MEMS (Micro-Electro-Mechanical Systems) accelerometer, these sensors convert minute mechanical oscillations – vibrations – into proportional electrical signals. When an object moves near the sensor, its mass and movement induce vibrations in the surrounding medium (air, structure), which the sensor picks up. Similarly, internal machine vibrations caused by rotation, imbalance, or impending failure become distinct signatures the sensor can identify.
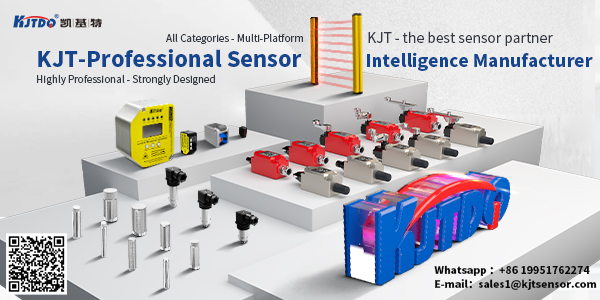
What makes vibration proximity sensors exceptionally valuable are their unique strengths:
- Immunity to Environmental Interference: This is perhaps their most significant advantage. They are largely unaffected by visual obstructions like dust, smoke, fog, or steam that plague optical sensors. They are also not confused by changes in target color, reflectivity, or transparency. Acoustic noise or air turbulence, problematic for ultrasonic sensors, typically has minimal impact on their ability to detect distinct vibration patterns. This makes them the go-to choice for harsh industrial settings like mining, foundries, construction sites, food processing plants with high humidity, and washdown environments.
- Non-Contact Detection: Vibration proximity sensors provide true non-contact detection. They don’t require physical touch with the target object, avoiding wear and tear or potential interference with the moving part itself. They sense the effects of the object’s presence or movement through induced vibrations in the surrounding environment or structure.
- Machine Health Monitoring Prowess: Beyond simple presence detection, high-sensitivity vibration sensors are indispensable tools for predictive maintenance. By continuously monitoring the vibration signature of machinery – bearings, motors, pumps, gearboxes – they can detect subtle changes indicative of wear, imbalance, misalignment, or lubrication failure long before catastrophic breakdown occurs. This proactive approach significantly reduces downtime and maintenance costs.
- Simplicity and Reliability: With fewer dependencies on pristine environmental conditions, vibration proximity sensors often boast high reliability and require less frequent calibration or maintenance compared to optical or ultrasonic counterparts. Their core technology is mechanically robust, especially MEMS-based sensors.
Implementing vibration proximity sensors effectively requires consideration of several factors:
- Mounting: The sensor must be securely mounted directly onto the structure whose vibration you wish to monitor (e.g., a machine frame) or very near the area where object-induced vibrations are expected. Proper mounting ensures optimal vibration transfer and signal quality.
- Sensitivity Adjustment: Most sensors feature sensitivity controls. This is crucial for tuning out background vibrations (e.g., plant floor rumble) while remaining responsive to the specific target vibration signature or proximity event. Vibration threshold settings define the level at which the sensor triggers its output.
- Frequency Range: Different vibration sources generate distinct frequency spectrums. Selecting a sensor tuned to the relevant frequency range (e.g., low frequencies for large structural movements, higher frequencies for bearing defects) enhances detection accuracy and signal-to-noise ratio.
- Output Type: Sensors offer various outputs: simple switches (on/off based on a threshold), analog outputs (proportional to vibration amplitude), or digital outputs (like IO-Link) transmitting richer data streams for advanced analysis.
The applications for vibration proximity sensors are vast and critical:
- Harsh Environment Detection: Detecting the presence or approach of vehicles, trolleys, or personnel in mines, quarries, steel mills, and chemical plants where dirt and fumes are prevalent.
- Conveyor Monitoring: Identifying jams, missing parts, or verifying object passage points on conveyor lines filled with dust or product debris.
- Machine Guarding: Providing an extra layer of safety by detecting unexpected vibrations indicating unintended machine operation or tampering.
- Predictive Maintenance (PdM): The cornerstone of modern PdM strategies. Monitoring vibration levels on motors, pumps, fans, and compressors to detect early signs of bearing wear, imbalance, eccentricity, looseness, or resonance issues. This enables condition-based maintenance rather than reactive fixes.
- Security Systems: Detecting intruders by sensing vibrations induced on fences, walls, or sensitive structures.
- Structural Health Monitoring: Assessing the integrity of bridges, buildings, or pipelines by analyzing their vibration response.
As technology evolves, vibration proximity sensing is benefiting from advancements in MEMS technology, making sensors smaller, more affordable, and capable of measuring complex multi-axis vibrations. Integration with Industrial IoT (IIoT) platforms is becoming seamless, allowing for remote monitoring, sophisticated data analytics through edge computing, and integration into broader smart factory ecosystems. Wireless vibration sensor nodes further enhance flexibility and reduce installation complexity.
In essence, the vibration proximity sensor is the silent sentinel of the industrial world. Where sight and sound fail, it thrives by feeling the subtle pulses of movement and machinery. Its robustness against environmental chaos, combined with its dual capability for reliable proximity detection and invaluable machine health insights, makes it an indispensable component for ensuring safety, optimizing efficiency, and preventing costly failures in the most demanding settings. When reliability amidst adversity is paramount, the solution often lies not in seeing or hearing, but in feeling the vibration.